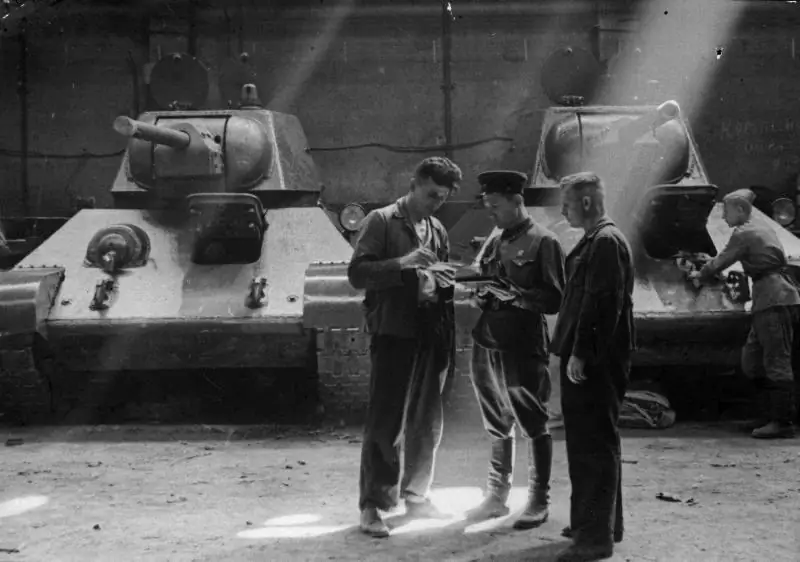
Alles zum Krieg mit einem Knall
Der hochfeste homogene 8C-Panzerstahl, der zum wichtigsten für den mittleren Panzer T-34 wurde, führte zu vielen Schwierigkeiten im Produktionsprozess. Es sei darauf hingewiesen, dass eine solche solide Panzerung während des gesamten Zweiten Weltkriegs nur in der Sowjetunion bei Panzern verwendet wurde. Und dabei gab es natürlich sowohl positive als auch negative Aspekte. In den vorherigen Teilen des Zyklus haben wir bereits die zahlreichen Risse besprochen, die das Schweißen der Rümpfe und Türme sowjetischer mittlerer Panzer begleiten. Gleichzeitig wurde dies schweren KV und dann IS vorenthalten: Die duktilere Panzerung mittlerer Härte verträgt Überspannungen beim Schweißen von Teilen viel leichter. Seit Anfang 1942 haben die Ingenieure des Armored Institute eine Reihe von Maßnahmen vorgeschlagen, um die Herstellung gepanzerter Hüllen zu vereinfachen und die Schweißtechnik zu modernisieren. Es wurde beschlossen, einige Knoten überhaupt nicht zu schweißen: Zum Beispiel wurde die Befestigung des Heck- und Frontrahmens auf das Nieten übertragen. In vielerlei Hinsicht war dies eine Anleihe nach einem gründlichen Studium deutscher Panzerfahrzeuge.
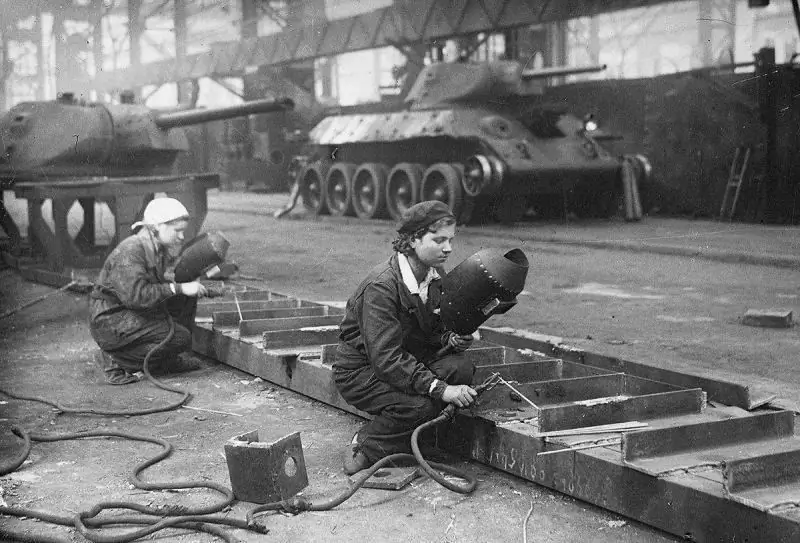
Die Front- und Seitenteile des Tanks wurden nun auf Wunsch von TsNII-48 nur noch mit Austenitelektroden geschweißt, besser geeignet für schwer schweißbare Eisensorten. Insgesamt waren nun bis zu 10 % (oder mehr) aller Elektroden, die für ein gepanzertes Fahrzeug verbraucht wurden, Austenit. Wenn Sie sich auf die Daten in Nikita Melnikovs Buch "Panzerindustrie der UdSSR während des Großen Vaterländischen Krieges" konzentrieren, wurden für einen T-34-76 etwa 400 Elektroden verbraucht, von denen 55 Austenit waren. Zu den Anforderungen für die Verwendung solcher Elektroden gehörte ein Verbot ihres Betriebs im Hochstrommodus - bis zu 320 A. Bei Überschreitung dieses Indikators droht eine starke Erwärmung des Schweißbereiches mit anschließender Verformung beim Abkühlen und Rissbildung. Bitte beachten Sie, dass ähnliche Funktionen wie das inländische "Panzerinstitut" in Deutschland von der 6. Abteilung der Rüstungsdirektion der Bodentruppen wahrgenommen wurden. Ihm sollten die Panzerfabriken die Verfahren zum Schweißen von Rümpfen und Türmen schriftlich zur Genehmigung vorlegen. Spezialisten der 6. Abteilung überprüften wiederum die eingereichten Materialien auf Einhaltung der temporären Spezifikationen für Schweißpanzer T. L.4014, T. L.4028 und T. L.4032. Diese Anforderungen wurden für das Schweißen deutscher Panzer mit einer Dicke von 16 bis 80 mm berechnet. Wie bereits im Artikel "Schweißen von Panzerpanzern: Deutsche Erfahrung" erwähnt, wurde in Deutschland kein automatisches Schweißen verwendet. Dies verlangsamte natürlich die Geschwindigkeit der deutschen Panzerindustrie erheblich, aber es gab einige Probleme mit Schweißmaschinen in der Sowjetunion. Die Automatisierung des Schweißens erforderte neben der unbestritten hohen Qualität der Schweißung hochwertige Zusatzwerkstoffe und die strikte Einhaltung der Arbeitstechnik. Dies war jedoch ein unvermeidlicher Preis für die Einführung einer revolutionären Produktionsmethode, die einen so großen Einfluss auf die Qualität und Geschwindigkeit der Tankmontage hatte.
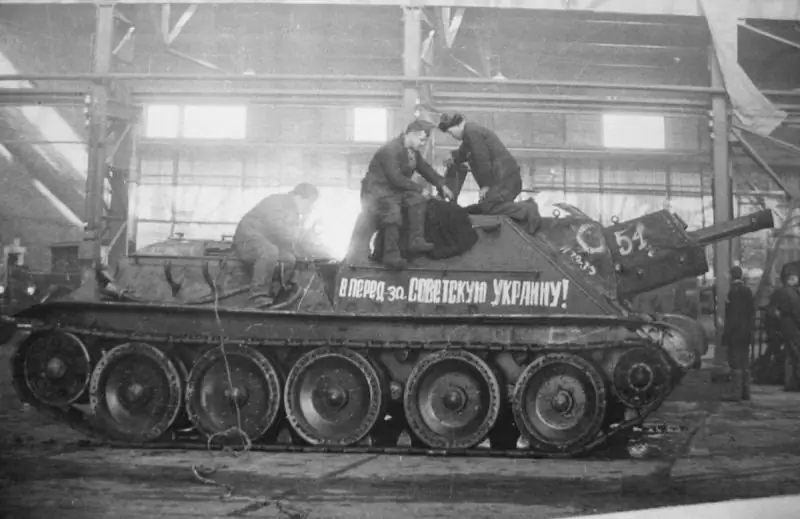
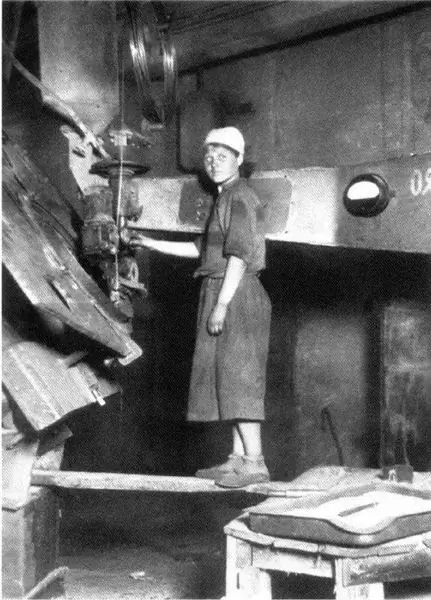
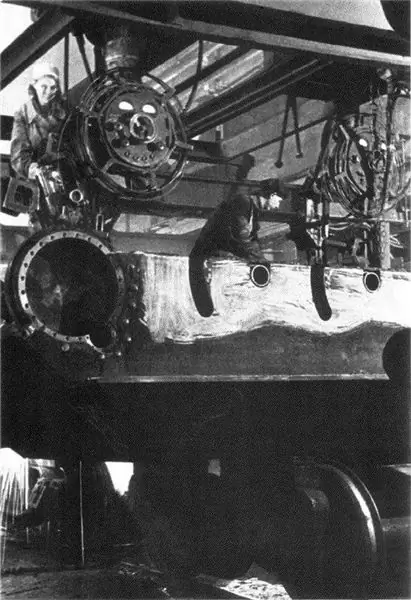
Wenn sich herausstellte, dass Hauptelektrode und Zusatzdraht zu stark mit Schwefel, Kohlenstoff und Phosphor verunreinigt waren (oder umgekehrt Mangan oder Manganoxid fehlten), führte dies direkt in der Schweißnaht zur Rissbildung. Es war wichtig, die zu schweißenden Produkte sorgfältig unter Flussmittel vorzubereiten. Die Anforderungen waren hoch: Die Teile müssen die richtigen Abmessungen haben, ohne Toleranzverletzungen. Ansonsten musste zum Schweißen das Teil auf der Helling "gezogen" werden, wodurch starke Eigenspannungen entstehen. Und eine einfache Nichtbeachtung der Stärke und Spannung des Schweißstroms führte zur Fehlerhaftigkeit der Nähte: Porosität, Nasenlöcher und fehlende Durchdringung. Angesichts des geringen Qualifikationsniveaus der Arbeiter, die Zugang zu Schweißmaschinen haben, ist es leicht, an die Möglichkeit solcher Mängel zu glauben. Alle hochqualifizierten Schweißer waren im Handschweißen tätig und konnten die Schweißqualität der "Paton-Maschinen" nicht beeinflussen. Obwohl sie an der Behebung von Defekten an Schweißmaschinen beteiligt waren.
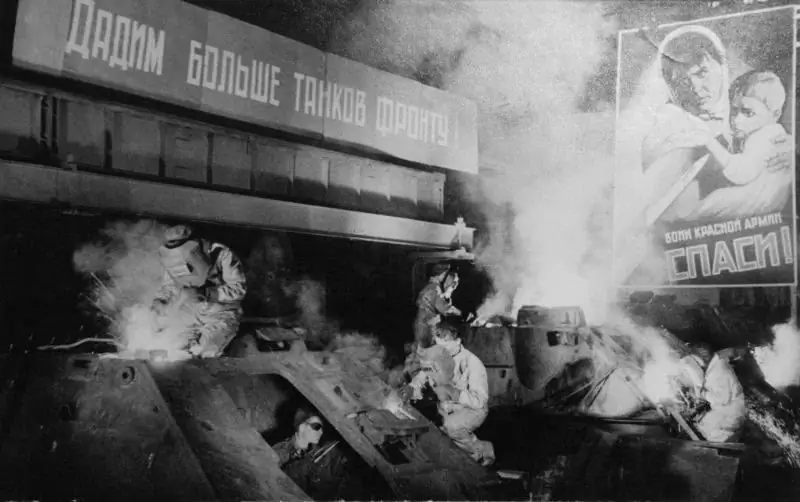
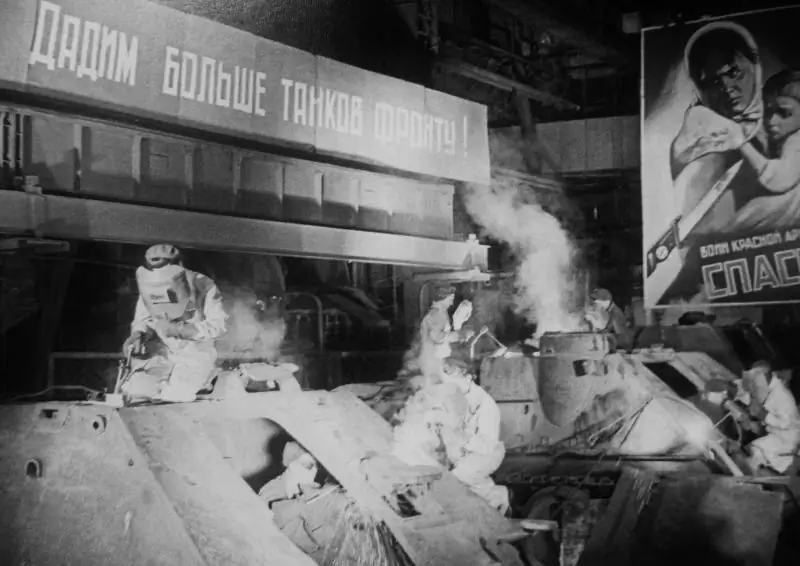
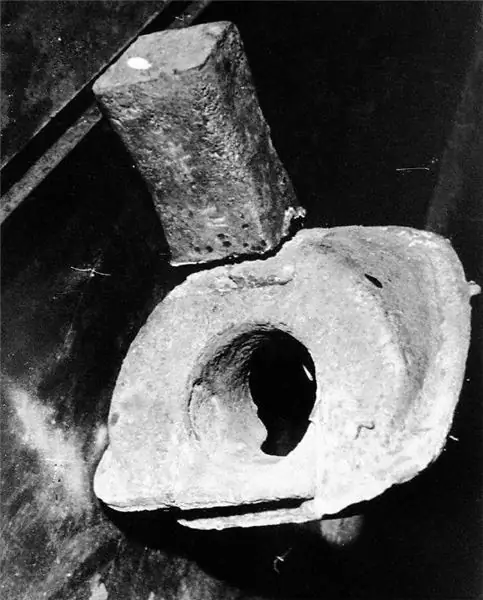
Die dramatische Steigerung der Produktivität der Panzerfabriken führte 1943 zu einem unerwarteten Problem. Es stellte sich heraus, dass die restliche Produktion nicht immer mit dem Panzerbau Schritt hielt. Die Maschinen arbeiteten auf Verschleiß, teilweise fehlten Amperemeter zur Kontrolle der Stromstärke an den Maschinen, es fehlten an hochwertigen Schweißelektroden. All dies führte zu periodischen "Ausbrüchen" von Rissen unter den seriellen T-34. Um diese Heiratswellen auszulöschen, mussten die Einsatzkräfte der Anlagentechniker und Ingenieure von TsNII-48 durchgeführt werden.
Überarbeitung des Designs
Die harte Panzerung und Risse darin zwangen die Ingenieure, nicht nur die automatische Schweißtechnik, sondern auch die manuelle Vorgehensweise zu ändern. Große Schweiß- und Wärmebelastungen erfuhren insbesondere die oberen Frontpartien, als während der Montage der Schutz des DT-Maschinengewehrs, Ösen, eine Schlaufe der Fahrerluke, ein Schutzbügel und andere Kleinigkeiten darauf geschweißt wurden. Rund um den Maschinengewehrschutz, der sehr sorgfältig verbrüht wurde, gab es oft bis zu 600 mm lange Risse! Das Schweißen war im Bereich des Bugs der Seiten voluminös, wo sie mit kräftigen doppelseitigen Nähten mit den vorderen Ober- und Unterplatten sowie mit Faultierhalterungen befestigt wurden. Oft entsprach der Spalt zwischen den Teilen in diesen Teilen nicht den normativen, und daher war es notwendig, eine besonders massive Schweißnaht einzubringen, die starke innere Spannungen hinterließ. Es war erforderlich, die Steifigkeit einiger Knoten zu reduzieren und den Gesamtanteil des Schweißens in den Verbindungen zu reduzieren, was von TsNII-48-Spezialisten in kürzester Zeit durchgeführt wurde. Insbesondere wurde die Art der Verbindung der Radlaufverkleidungen mit dem vorderen Teil des Rumpfdachs geändert. Mit Hilfe einer speziellen "Puffer"-Leiste aus Baustahl, die zuvor mit der Kotflügelverkleidung verschweißt wurde, konnte die Endspannung innerhalb der Naht und um die Panzerung reduziert werden. Als nächstes haben wir die oben erwähnte "Infrastruktur" auf der Frontplatte des Panzers herausgefunden. Nach den neuen technischen Gegebenheiten war es nun möglich, die Augenschrauben, den Schutz des Maschinengewehrs und die Lukenscharniere nur noch mit 5-6 mm Elektroden in mehreren Lagen zu schweißen: mindestens vier! In ähnlicher Weise wurden die Kotflügel mit dem Dach, die Frontplatte mit den Seiten, die Kotflügel und das Dach verbunden. Alles andere wurde in 2-3 Durchgängen mit 7-10 mm Elektroden gekocht.
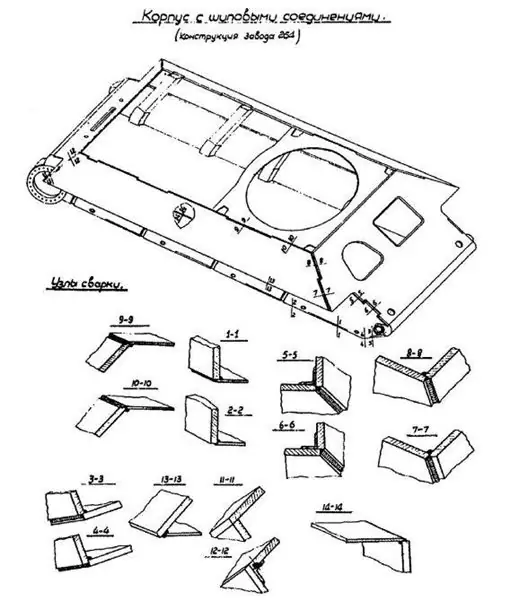
Die Technologie zum Verbinden von Teilen des Rumpfes des T-34-Panzers wurde ebenfalls geändert. Anfänglich wurden alle Verbindungen, bis auf die Schnittstelle des VLD und NLD, in einem Viertel wie zeichnungsgemäß hergestellt. Aber bald nach Kriegsbeginn wurden sie in einen Spike umgewandelt, was sich jedoch auch nicht rechtfertigte - an den Stellen, an denen die Nähte geschnitten wurden, traten zu viele Risse auf. Auch wegen der starken lokalen Schrumpfspannungen nach dem Schweißen war die Spikeverbindung für hochharte Panzerungen nicht ganz geeignet. Was für die deutsche Plastikpanzerung gut war, war für heimische T-34 nicht geeignet. Erst 1943 erschienen auf dem "Siegpanzer" die endgültigen Artikulationsoptionen, die die TsNII-48-Spezialisten zufrieden stellten - überlappend und Rücken an Rücken.
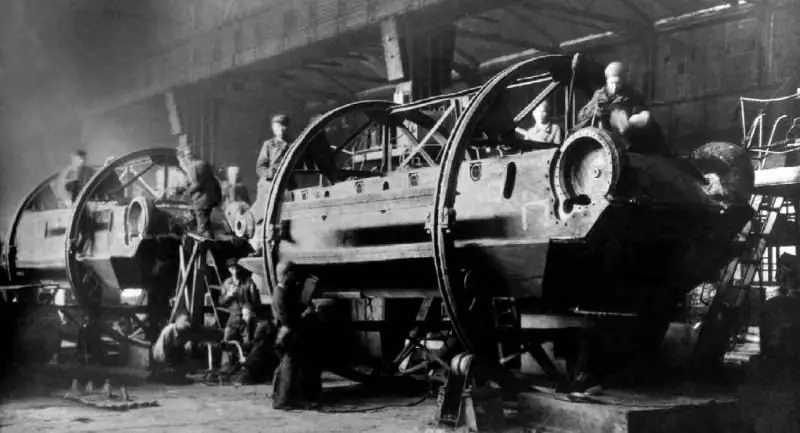
Die Rümpfe schwerer sowjetischer Panzer durchliefen den einfachsten Prozess der Optimierung der Schweißvorgänge. Die Verbindung der Panzerplatten in einem Viertel am KV wurde unverändert belassen, jedoch wurden die inneren Verstärkungsbögen durch innere Kehlnähte ersetzt. Bereits mitten im Krieg wurden für schwere Panzer die optimalsten Konfigurationen der zusammenpassenden Panzerplatten gewählt (zuerst durch Beschuss). Wenn der Verbindungswinkel nahe 90 Grad lag, war es besser, die Methode "in einem Dorn" oder in einem Viertel und in allen anderen Varianten - in einer Wirbelsäule oder in einem Zahn - zu verwenden. Als Ergebnis dieser Studien wurde in TsNII-48 eine besondere Form des oberen Teils der Buganordnung des IS-2-Panzers geboren, als die Panzerung mit einer Dicke von 100-110 mm einen Rundumschutz gegen. bot 88-105-mm-Projektile. Das Zusammenfügen der Teile in dieser soliden Konstruktion war eine einfache Überraschung.