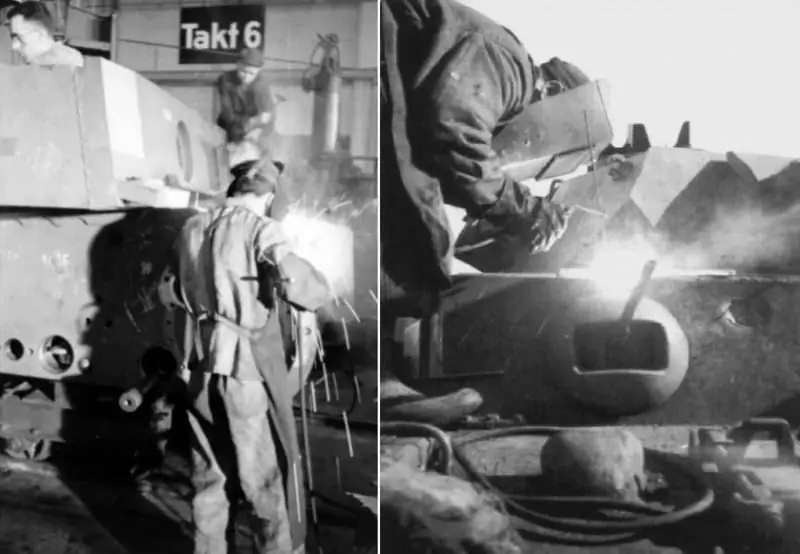
Deutscher Ansatz
Im ersten Teil des Materials über Schweißtechnologien während des Großen Vaterländischen Krieges wurde erwähnt, dass eine der wichtigsten Errungenschaften sowjetischer Technologen und Wissenschaftler die Einführung der Automatisierung des Schweißens von Panzerrümpfen und -türmen war. In Nazi-Deutschland wurde in Panzerfabriken kein automatisches Schweißen verwendet. Dafür gab es eine sehr wichtige Erklärung: Während der Hauptkriegszeit herrschte in der Panzerindustrie des Dritten Reiches kein Mangel an hochqualifizierten Arbeitskräften, einschließlich Schweißern. Und in der Sowjetunion ging bei der Evakuierung großer Unternehmen nach Osten für die Industrie wertvolles Personal verloren, was nicht nur die Qualität der Panzermontage, sondern sogar die Möglichkeit der Produktion gefährdete. In Deutschland kam es dazu, dass beim Schweißen der Rümpfe von "Panthers" und "Tigers" einzelne Schweißer getrennten Nähten zugeordnet wurden! Ingenieur V. V. Ardentov schreibt darüber im Material "Deutsche Erfahrung beim Schneiden von Panzern und Schweißen von Panzerrümpfen" im "Bulletin der Panzerindustrie" im siegreichen 1945-Jahr. Grundlage seiner Arbeit war die Untersuchung zweier Panzerrumpffabriken in Kirchmeser und Brandenburg. Offensichtlich konnten sich diese Fabriken bis in die letzten Kriegsmonate einen solchen technologischen Luxus in Form von separaten Schweißern für separate Nähte leisten.
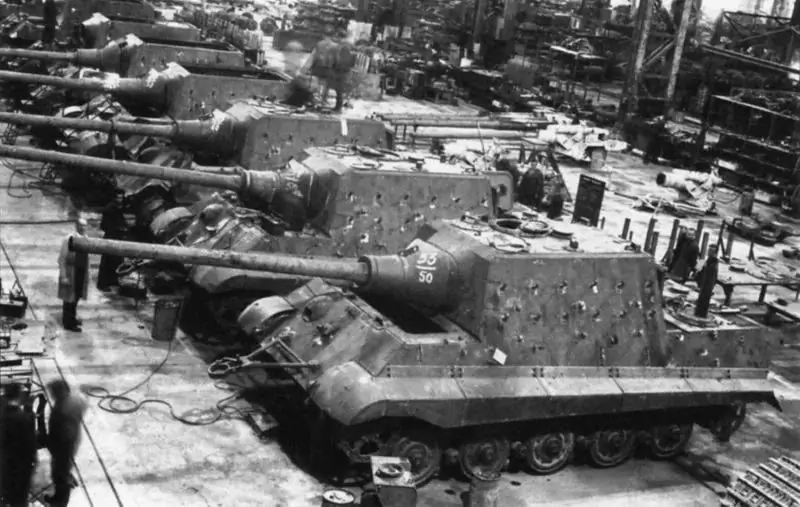
Vor dem Schweißen der Rümpfe wurden die Panzerplatten geschnitten, was bis 1942 maschinell erfolgte. Zum Ausschneiden von Panzerplatten für Dorn-in-Dorn-Verbindungen war es viel bequemer, das Acetylen-Sauerstoff-Schneiden zu verwenden, das auch in ähnlichen Situationen in der sowjetischen Panzerindustrie verwendet wurde. Hier waren die Deutschen unseren Panzerbauern sowohl in der Effizienz als auch in der Schnittqualität voraus. Dies ist im Wesentlichen auf den Einsatz hochwertiger Werkzeuge (Brennschneidmaschinen Messer und Grisheim) mit der Möglichkeit der Feinabstimmung der Panzerplattenstärke zurückzuführen. Außerdem verwendeten die Deutschen Sauerstoff mit einem hohen Reinheitsgrad - mehr als 99%. Schließlich benutzten die Deutschen beim Durchtrennen der Rüstung mehrere Fackeln, unter anderem zum Anfasen. Der Brennschneidprozess selbst wurde automatisiert - dadurch konnte der Prozess beschleunigt und wesentlich genauer gestaltet werden.
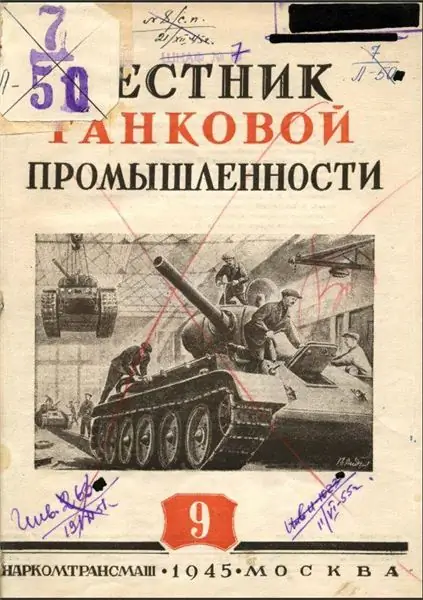
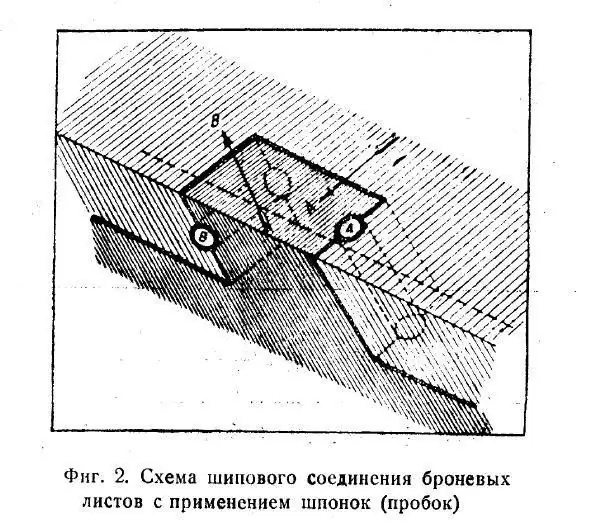
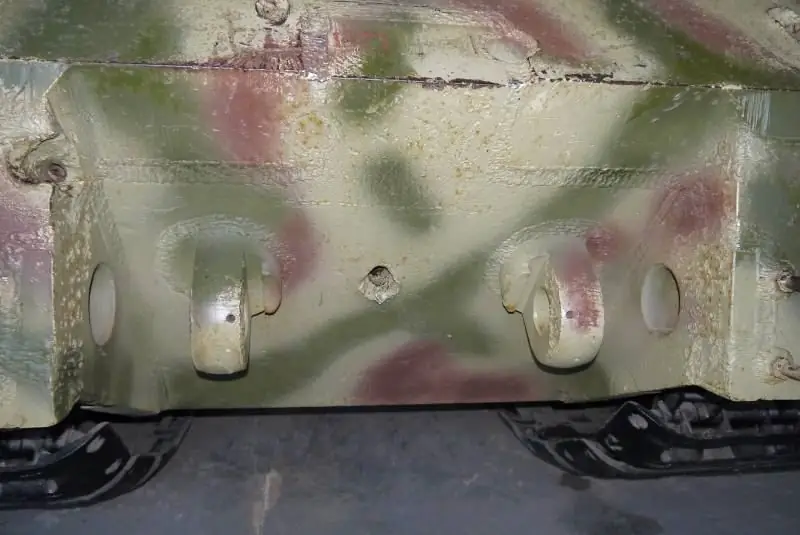
[Center]
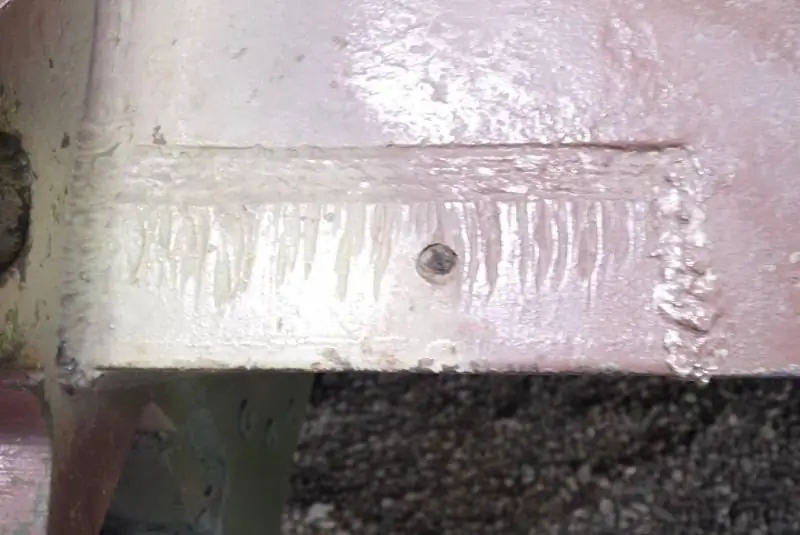
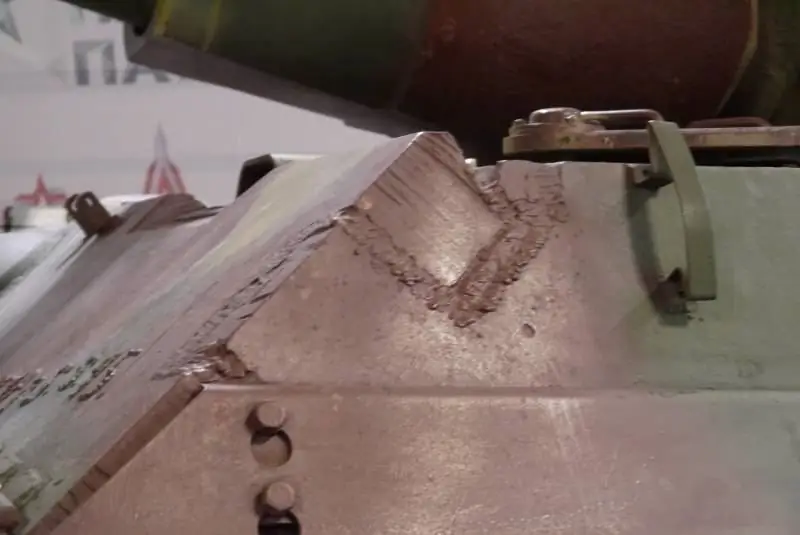
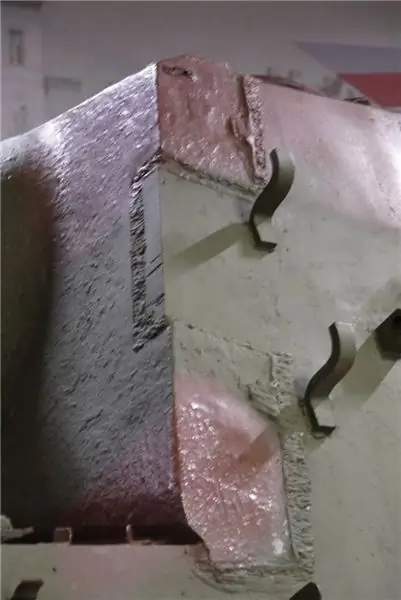
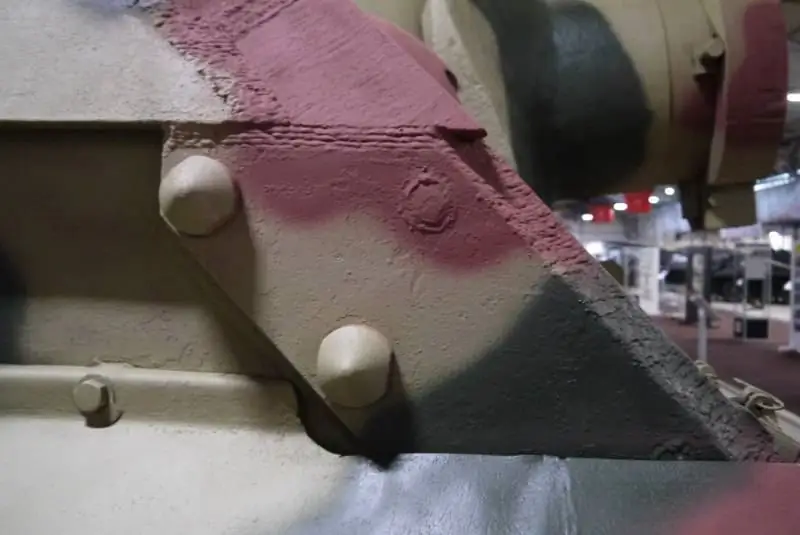
[/Center]
Wie Sie wissen, war eines der Unterscheidungsmerkmale der Rümpfe deutscher Panzer aus dem Jahr 1942 die Dornverbindung von Panzerplatten mit einem rechteckigen oder schrägen Dorn. Dabei beschränkten sich die Deutschen nicht auf eine einfache Artikulation - zusätzlich wurden aus Festigkeitsgründen zylindrische Schlüssel oder Dübel in die Gelenke eingeführt. Dies war insbesondere bei mittleren Panzern "Panther", Selbstfahrlafetten "Ferdinand", Türmen schwerer "Tiger" und einigen Korps "Maus" üblich. Solche Stopfen waren Stahlrollen mit einem Durchmesser von bis zu 80 mm, die nach dem Zusammenfügen zum Schweißen in die Verbindungen der zu verbindenden Bleche eingesetzt wurden. Die Stopfen wurden in der Ebene der Kanten des Dorns der Panzerplatten platziert - für jede Verbindung wurde ein Paar benötigt. Tatsächlich wurde die Spikeverbindung nach der Installation der Schlüssel noch vor dem Schweißen einteilig. In diesem Fall wurden die Dübel oberflächenbündig mit der Panzerung montiert und entlang des Umfangs des Sockels verschweißt. Durch die Spike-Verbindung der Panzerplatten der Panzerrümpfe wurde der ballistische Schutz sowohl der Schweißnähte als auch der Panzerung deutlich verbessert. Dies wurde zunächst durch eine Erhöhung der Gesamtlänge der Schweißnaht, bestehend aus einzelnen Segmenten, sichergestellt, was die Rissausbreitung etwas reduzierte.
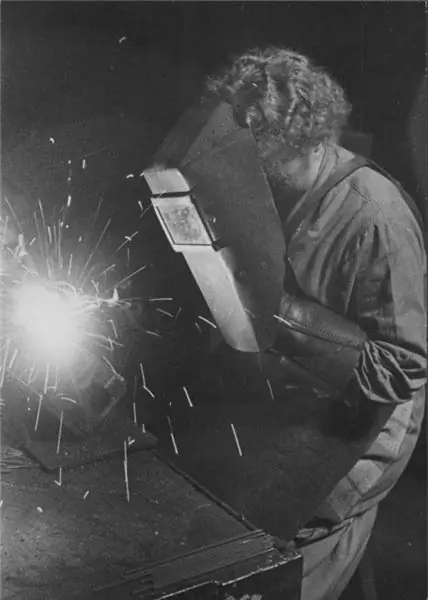
Eines der Probleme bei der Herstellung der Rümpfe deutscher Panzer war die Herstellung von Ausschnitten und Löchern (zum Beispiel für die oben erwähnten Panzerverbindungen). Es war unmöglich, sie mit Gas zu schneiden, also wurde gebohrt. Für Stähle der Güteklassen E-18 und E-19, die oberflächengehärtet wurden, war es zunächst in der Regel unmöglich, einen geeigneten Bohrer zu finden, da sich die äußere Schicht der Panzerung als so hart herausstellte. Beim Bohren eines Lochs vor dem Abschrecken bildete sich im Bereich des Lochs ein ungleichmäßiges Abschrecken, gefolgt von Verformung und radialer Rissbildung. Ja, und es gab Risse an den deutschen Panzern, und zwar beträchtliche, und die deutschen Bemühungen, sie zu vermeiden, werden später erörtert. Teilweise wurde das Problem der ungleichmäßigen Aushärtung der Panzerung im Bereich der Löcher durch eine spezielle feuerfeste Paste gelöst, mit der die Löcher vor dem Versand in den Ofen abgedeckt wurden. Aber auch dies hat das Problem nur teilweise gelöst. Erst Ende 1944 am Elektrothermischen Institut in Essen wurde dieses Problem durch ein lokales Anlassverfahren am gehärteten Bereich der Panzerung gelöst. Die von den Deutschen entwickelte Einheit wird in seinem Artikel des Gewinners des Stalin-Preises, des Kandidaten für technische Wissenschaften A. A. Shmykov, beschrieben. Das Material wurde Ende 1945 in der für die damalige Zeit geheimen und uns bekannten Fachausgabe „Bulletin of Tank Industry“veröffentlicht. In den Nachkriegsjahren waren die Seiten des Vestnik reich an detaillierten Analysen der Ingenieurtricks deutscher Ingenieure, da es genügend erbeutete Ausrüstung gab.
Aber zurück zur lokalen Freigabe der Panzerung, wo die Löcher gebohrt wurden. Basis der Anlage war eine an die Bohrstelle angeschlossene Graphitelektrode, durch die ein elektrischer Strom von 220 Ampere und eine Spannung von 380 Volt geleitet wurde. Dadurch wurde die Panzerung auf die Anlasstemperatur erhitzt. Je nach Panzerstärke und Lochdurchmesser dauerte dies 7 bis 15 Minuten. Nach dem Anlassvorgang nahm die Härte der Panzerung um das 2-2,5-fache ab. Bemerkenswert ist, dass die heimische Industrie (einschließlich der Tankindustrie) auch das Stahlvergüten durch Erhitzen mit Strom einsetzte - das "Know-how" der Deutschen lag nur in der Verwendung einer Graphitelektrode.
Deutsche und Elektroden
Die Deutschen nutzten den Urlaub auch beim Schweißen von Blechen ihrer hochharten Rüstung mit einem Kohlenstoffgehalt im Bereich von 0,40 bis 0,48 %. Dies wurde den Spezialisten des TsNII-48 (Armored Institute) während des Krieges bekannt, als metallurgische Ingenieure nach Rezepten suchten, um Risse in der Panzerung des T-34 zu reduzieren. Wie sich herausstellte, gaben die Deutschen die Panzerplatten bei Temperaturen von 500-600 Grad (hoher Urlaub) frei und schweißten dann die auf 150-200 Grad vorgewärmte Panzerung in mehreren Durchgängen. Schweißer verwendeten keine Elektroden mit einem Durchmesser von mehr als 5 mm - kaum zu glauben angesichts der Dicke der Panzerung deutscher Panzer. Elektroden mit einem Durchmesser von 4 mm arbeiteten mit einem Strom von 120-140 Ampere, mit einem Durchmesser von 5-6 mm - 140-160 Ampere. Diese Technologie ermöglichte es, den Schweißbereich nicht zu überhitzen. Dadurch wurde eine kleinere Härte- und Anlasszone erhalten. Außerdem kühlte die Naht nach dem Schweißen sehr langsam ab - all dies ermöglichte es den Deutschen schließlich, Risse an den Stellen der Schweißverbindungen mehr oder weniger erfolgreich zu beseitigen. Darüber hinaus wurden überwiegend austenitische Elektroden verwendet, die zu einer hohen Duktilität der Schweißnaht und ihrem verlängerten Übergang in einen spröden martensitischen Zustand führten. Die Ingenieure von TsNII-48 haben die Merkmale des technologischen Zyklus des Panzerschweißens von Panzern sehr sorgfältig studiert, was es ermöglichte, diese Techniken erfolgreich auf den Produktionszyklus des T-34 zu übertragen. Ein so aufwendiges mehrlagiges Aufbringen von Schweißnähten im gesamten Tankrumpf konnte sich natürlich niemand in der Panzerindustrie leisten, das deutsche „Know-how“wurde nur in den kritischsten rissgefährdeten Nähten eingesetzt.
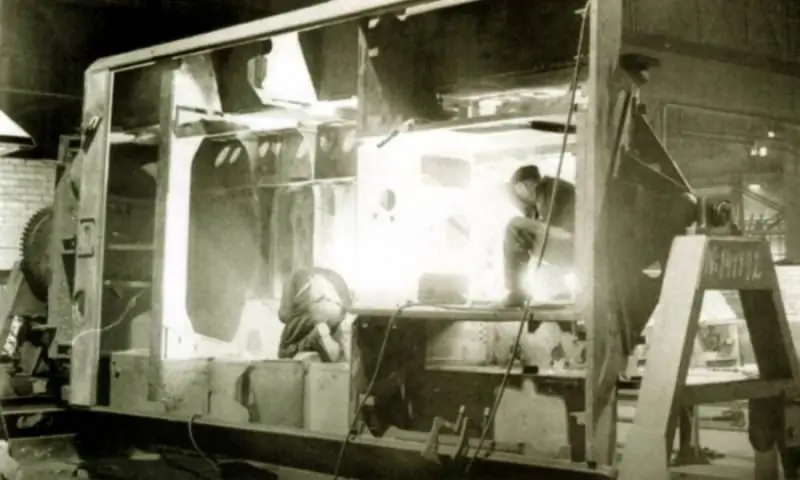
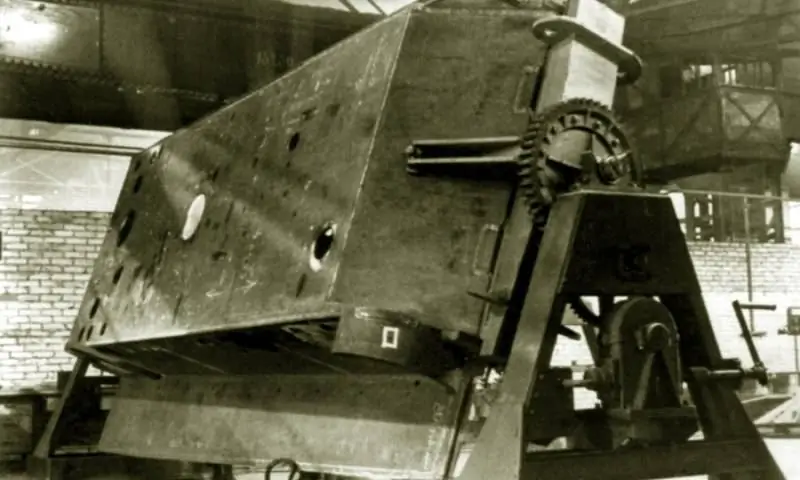
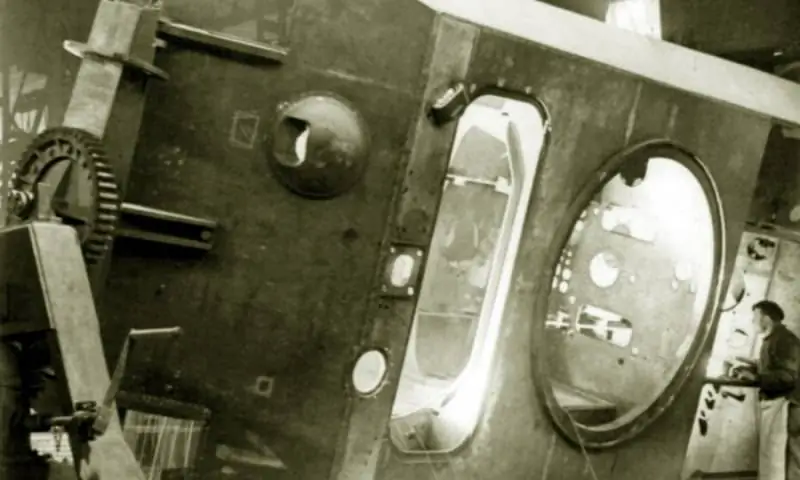
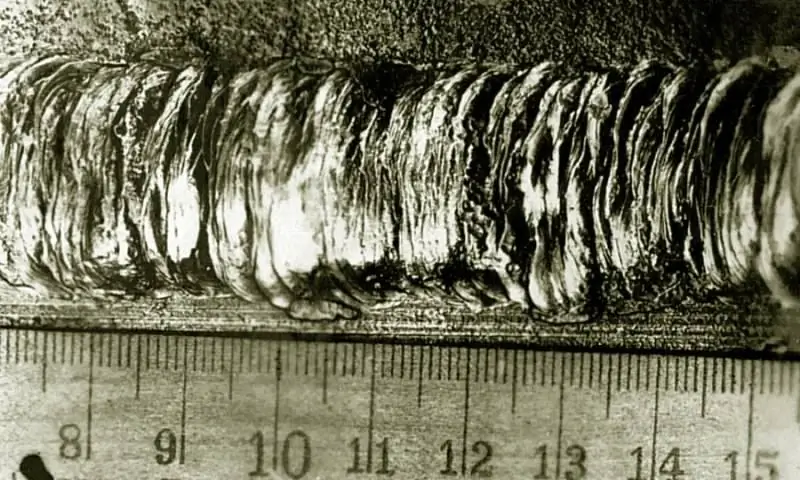
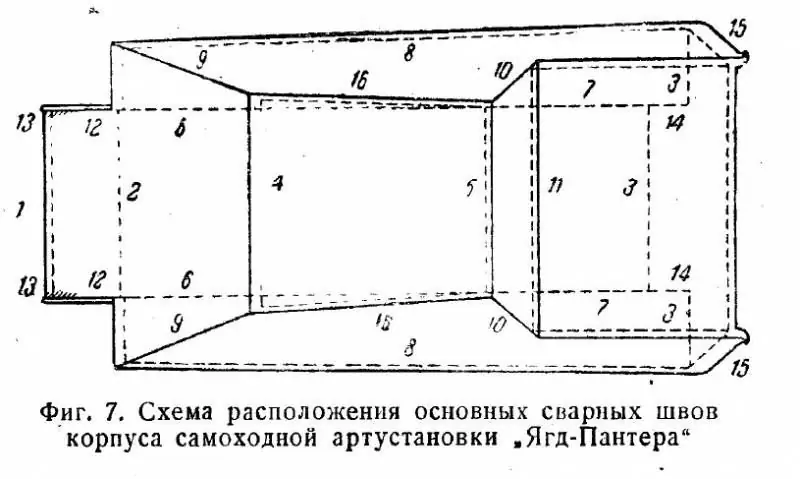
Die Deutschen führten das Schweißen von Panzerrümpfen unter recht komfortablen Bedingungen auf riesigen Kippern ohne vorherige Heftzwecke durch (obwohl sie in einigen Fällen noch über die gesamte Länge der Verbindung durch eine 5-mm-Elektrode gingen). Der Kipper war eine Konstruktion, auf der sich wie auf einem Spieß die Karkasse eines deutschen Panzers um die Längsachse drehte. Der Antrieb war entweder manuell oder elektrisch. Aufgrund der hohen Schnittgenauigkeit überschritten die Abstände zwischen den am Rotator montierten Körperteilen (zumindest in der Hauptkriegszeit) 3-4 mm nicht. Ansonsten wurden Prozessdichtungen aus Stahl verwendet. Lange Nähte wurden von Schweißern in mehrere kleine gebrochen und gleichzeitig in eine Richtung geschweißt. Auch die Schließnähte wurden von zwei Schweißern synchron zueinander verschweißt. Dies gewährleistete eine minimale Härtespannung des Stahls und eine möglichst gleichmäßige Verteilung. Nach einer der von Alexander Volgin im Material "Rahmen für die deutsche Menagerie" geäußerten Legenden war das Gehalt der Schweißer in einigen Unternehmen des Dritten Reiches Akkord - für die auf dem Panzer abgelagerte Metallmasse.
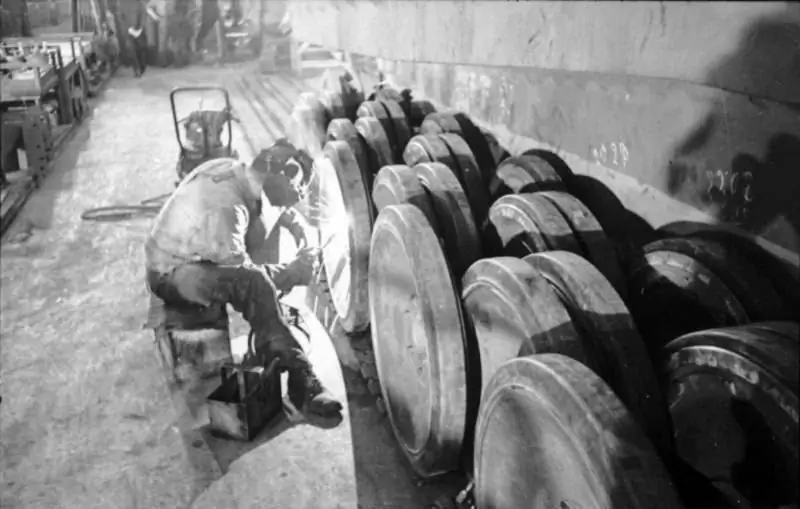
Über besondere Regeln für die Schweißnahtkontrolle in der deutschen Panzerindustrie braucht man nicht zu sprechen - es gab kein Röntgen, keine magnetische Fehlererkennung, kein primitives Bohren. Und es gab Risse in den Nähten! Waren sie bis zu 100 mm lang, wurden sie geschliffen und geschweißt, bei mehr wurden sie mit einem Lichtbogen geschmolzen und auch geschweißt. Dasselbe taten sie auch mit visuell erkannten Rissen in der Hauptpanzerung. Im Laufe der Zeit gelang es den Deutschen übrigens, den Anteil der Risse in Schweißnähten durch neue Elektrodenzusammensetzungen von 30-40% auf 10-20% zu reduzieren. Auch der Stichwechsel bei Mehrlagenschweißungen mit austenitischen und ferritischen Elektroden wurde eingesetzt.