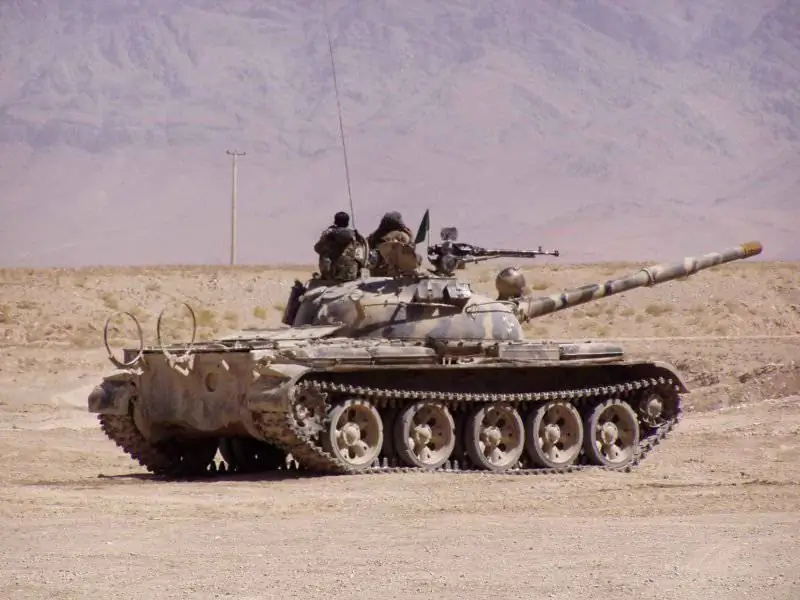
Im Jahr 1955 wurde die Entscheidung der Regierung getroffen, ein Konstruktionsbüro für spezielle Dieseltechnik im Kharkov Transport Engineering Plant zu schaffen und einen neuen Tankdieselmotor zu entwickeln. Professor A. D. Charomsky wurde zum Chefdesigner des Designbüros ernannt.

Die Wahl des Konstruktionsschemas des zukünftigen Dieselmotors wurde hauptsächlich von der Erfahrung mit der Arbeit an 2-Takt-Dieselmotoren OND TsIAM und dem U-305-Motor sowie dem Wunsch bestimmt, die Anforderungen der Konstrukteure des neuen T. zu erfüllen -64-Panzer, entwickelt in diesem Werk unter der Leitung des Chefkonstrukteurs AA … Morozov: um die minimalen Abmessungen des Dieselmotors, insbesondere in der Höhe, in Kombination mit der Möglichkeit zu gewährleisten, ihn quer zwischen den Bordplanetengetrieben im Tank zu platzieren. Es wurde ein Zweitakt-Dieselschema mit einer horizontalen Anordnung von fünf Zylindern mit entgegengesetzt bewegten Kolben gewählt. Es wurde beschlossen, einen Motor mit Aufblasen und Nutzung der Abgasenergie in einer Turbine zu bauen.
Was war der Grund für die Wahl eines 2-Takt-Dieselmotors?
Früher, in den 1920er bis 1930er Jahren, wurde die Entwicklung eines 2-Takt-Dieselmotors für Luft- und Landfahrzeuge aufgrund vieler ungelöster Probleme, die mit dem Wissen, der Erfahrung und den Fähigkeiten der einheimischen Industrie, die von diese Zeit.
Die Untersuchung und Forschung von 2-Takt-Dieselmotoren einiger ausländischer Firmen führte zu dem Schluss, dass es erhebliche Schwierigkeiten bei deren Beherrschung in der Produktion gibt. So zeigte zum Beispiel eine Studie des Central Institute of Aviation Motors (CIAM) in den 30er Jahren des von Hugo Juneckers entworfenen Jumo-4-Dieselmotors erhebliche Probleme im Zusammenhang mit der Entwicklung solcher Motoren bei der Herstellung solcher Motoren durch den Inland Industrie dieser Zeit. Es war auch bekannt, dass England und Japan, die eine Lizenz für diesen Dieselmotor erworben hatten, bei der Entwicklung des Junkers-Motors scheiterten. Gleichzeitig wurden in den 30er und 40er Jahren in unserem Land bereits Forschungsarbeiten an 2-Takt-Dieselmotoren durchgeführt und Versuchsmuster solcher Motoren hergestellt. Die führende Rolle bei diesen Arbeiten gehörten den CIAM-Spezialisten und insbesondere dem Department of Oil Engines (OND). CIAM entwarf und fertigte Muster von 2-Takt-Dieselmotoren verschiedener Abmessungen: OH-2 (12/16, 3), OH-16 (11/14), OH-17 (18/20), OH-4 (8/ 9) und eine Reihe anderer Originalmotoren.
Unter ihnen war das FED-8-Triebwerk, das unter der Leitung der prominenten Triebwerkswissenschaftler B. S. Stechkin, N. R. Briling, A. A. Bessonov entwickelt wurde. Es handelte sich um einen 2-Takt-16-Zylinder-Flugdieselmotor in X-Form mit Ventil-Kolben-Gasverteilung, der Dimension 18/23 mit einer Leistung von 1470 kW (2000 PS). Einer der Vertreter der 2-Takt-Dieselmotoren mit Aufladung ist ein sternförmiger 6-Zylinder-Turbo-Kolben-Dieselmotor mit einer Leistung von 147 … 220 kW (200 … 300 PS), der bei CIAM unter der Leitung von BS Stechkin. Die Leistung der Gasturbine wurde über ein geeignetes Getriebe auf die Kurbelwelle übertragen.
Die damals getroffene Entscheidung bei der Entwicklung des FED-8-Triebwerks hinsichtlich der Idee selbst und des Konstruktionsschemas bedeutete dann einen bedeutenden Fortschritt. Das Arbeitsverfahren und insbesondere das Verfahren des Gaswechsels bei hohem Druck und Schlaufenblasen sind jedoch noch nicht ausgearbeitet. Daher wurde der FED-8-Diesel nicht weiterentwickelt und 1937 wurde die Arbeit daran eingestellt.
Nach dem Krieg ging die deutsche technische Dokumentation in den Besitz der UdSSR über. Sie fällt in A. D. Charomsky als Entwickler von Flugzeugtriebwerken und interessiert sich für Junkers Koffer.
Junkers 'Koffer - eine Reihe von Flugzeug-Zweitakt-Turbo-Kolben-Motoren Jumo 205 mit gegenläufig bewegten Kolben wurde in den frühen 30er Jahren des 20. Jahrhunderts entwickelt. Die Eigenschaften des Jumo 205-C-Motors sind wie folgt: 6-Zylinder, 600 PS. Hub 2 x 160 mm, Hubraum 16,62 Liter, Verdichtung 17:1 bei 2.200 U/min
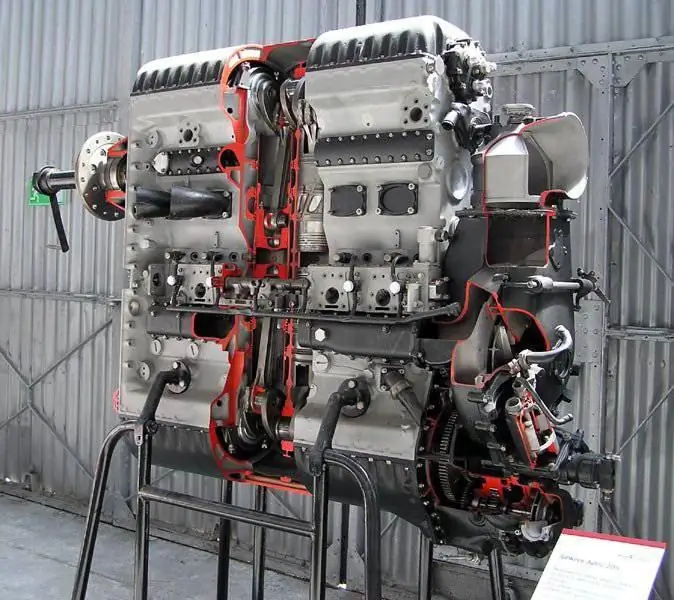
Jumo 205-Motor
Während des Krieges wurden etwa 900 Motoren hergestellt, die erfolgreich auf Do-18, Do-27 Wasserflugzeugen und später auf Hochgeschwindigkeitsbooten eingesetzt wurden. Schon bald nach dem Ende des Zweiten Weltkriegs im Jahr 1949 entschloss man sich, solche Motoren auf den bis in die 60er Jahre im Einsatz befindlichen Ostdeutschen Patrouillenbooten einzubauen.
Auf der Grundlage dieser Entwicklungen schuf AD Charomsky 1947 in der UdSSR einen Zweitakt-Flugzeugdiesel M-305 und einen Einzylinderraum dieses Motors U-305. Dieser Dieselmotor entwickelte eine Leistung von 7350 kW (10.000 PS). mit geringem spezifischem Gewicht (0, 5 kg / PS) und niedrigem spezifischen Kraftstoffverbrauch -190 g / kWh (140 g / PS). Es wurde eine X-förmige Anordnung von 28 Zylindern (vier 7-Zylinderblöcken) verwendet. Die Dimension des Motors wurde gleich 12/12 gewählt. Für hohen Schub sorgte ein mechanisch mit der Dieselwelle verbundener Turbolader. Um die im M-305-Projekt festgelegten Hauptmerkmale zu überprüfen, den Arbeitsprozess und die Konstruktion von Teilen zu erarbeiten, wurde ein Versuchsmodell des Motors mit dem U-305-Index gebaut. G. V. Orlova, N. I. Rudakov, L. V. Ustinova, N. S. Zolotarev, S. M. Shifrin, N. S. Sobolev sowie Technologen und Arbeiter der CIAM-Pilotanlage und der OND-Werkstatt.
Das Projekt des Full-Size-Flugzeugdiesels M-305 wurde nicht umgesetzt, da sich die Arbeit der CIAM, wie die gesamte Luftfahrtindustrie des Landes, bereits damals auf die Entwicklung von Turbojet- und Turboprop-Triebwerken und den Bedarf an einem 10.000-PS-Dieselmotor für die Luftfahrt verschwunden.
Die hohen Werte des Dieselmotors U-305: Liter Motorleistung 99 kW / l (135 PS / l), Literleistung aus einem Zylinder von fast 220 kW (300 PS) bei einem Ladedruck von 0,35 MPa; hohe Drehzahl (3500 U/min) und Daten aus mehreren erfolgreichen Langzeittests des Motors - bestätigten die Möglichkeit, einen effektiven kleinen 2-Takt-Dieselmotor für Transportzwecke mit ähnlichen Anzeigen und Konstruktionselementen zu schaffen.
1952 wurde das Labor Nr. 7 (ehemals OND) des CIAM durch einen Regierungsbeschluss in das Forschungslabor für Motoren (NILD) umgewandelt, das dem Ministerium für Verkehrstechnik unterstellt war. Eine Initiativgruppe von Mitarbeitern - hochqualifizierte Spezialisten für Dieselmotoren (G. V. Orlova, N. I. Rudakov, S. M. Shifrin usw.), die von Professor A. D. Charomsky geleitet wird, befindet sich bereits im NILD (später - NIID). der 2-Takt-Motor U-305.
Diesel 5TDF
1954 machte A. D. Charomsky der Regierung den Vorschlag, einen 2-Takt-Tankdieselmotor zu entwickeln. Dieser Vorschlag deckte sich mit der Forderung des Chefkonstrukteurs des neuen Panzers A. A. Morozov und A. D. Charomsky wurde zum Chefdesigner der Anlage ernannt. V. Malyshev in Charkow.
Da das Konstruktionsbüro für Panzermotoren dieser Fabrik hauptsächlich in Tscheljabinsk, A. D. Charomsky musste ein neues Konstruktionsbüro gründen, eine experimentelle Basis schaffen, eine Pilot- und Serienproduktion aufbauen und Technologien entwickeln, die das Werk nicht hatte. Die Arbeit begann mit der Herstellung einer Einzylindereinheit (OTsU), ähnlich dem U-305-Motor. Am OTsU wurden die Elemente und Prozesse des zukünftigen Full-Size-Tank-Dieselmotors erarbeitet.
Die Hauptbeteiligten an dieser Arbeit waren A. D. Charomsky, G. A. Volkov, L. L. Golinets, B. M. Kugel, M. A., Meksin, I. L. Rovensky und andere.
1955 nahmen NILD-Mitarbeiter an der Konstruktionsarbeit im Dieselwerk teil: G. V. Orlova, N. I. Rudakov, V. G. Lavrov, I. S. Elperin, I. K. Lagovsky und andere NILD-Spezialisten L. M. Belinsky, LI Pugachev, LSRoninson, SM Shifrin führten experimentelle Arbeiten durch an der OTsU im Kharkov Transport Engineering Plant. So sieht die sowjetische 4TPD aus. Es war ein funktionierender Motor, aber mit einem Nachteil - die Leistung betrug knapp über 400 PS, was für einen Panzer nicht ausreichte. Charomsky setzt einen weiteren Zylinder auf und bekommt 5TD.
Die Einführung eines zusätzlichen Zylinders hat die Dynamik des Motors stark verändert. Es entstand eine Unwucht, die starke Torsionsschwingungen im System verursachte. An seiner Lösung sind die führenden wissenschaftlichen Kräfte von Leningrad (VNII-100), Moskau (NIID) und Charkow (KhPI) beteiligt. 5TDF wurde EXPERIMENTELL durch Versuch und Irrtum auf den Zustand gebracht.
Die Dimension dieses Motors wurde gleich 12/12 gewählt, d.h. das gleiche wie beim U-305-Motor und OTsU. Um die Gasannahme des Dieselmotors zu verbessern, wurde beschlossen, Turbine und Verdichter mechanisch mit der Kurbelwelle zu verbinden.
Diesel 5TD hatte die folgenden Eigenschaften:
- hohe Leistung - 426 kW (580 PS) bei relativ kleinen Gesamtabmessungen;
- erhöhte Geschwindigkeit - 3000 U/min;
- Effizienz der Druckbeaufschlagung und Nutzung der Abgasenergie;
- geringe Höhe (weniger als 700 mm);
- 30-35% weniger Wärmeübertragung im Vergleich zu bestehenden 4-Takt-Dieselmotoren (Saugmotor) und folglich ein geringerer Volumenbedarf für das Kühlsystem des Kraftwerks;
- zufriedenstellende Kraftstoffeffizienz und die Möglichkeit, den Motor nicht nur mit Dieselkraftstoff, sondern auch mit Kerosin, Benzin und ihren verschiedenen Mischungen zu betreiben;
- Nebenabtrieb von beiden Enden und seine relativ geringe Länge, die es ermöglicht, den MTO-Tank mit einer Queranordnung eines Dieselmotors zwischen zwei Bordgetrieben in einem viel kleineren Raumbedarf zu montieren als bei einer Längsanordnung von der Motor und das Zentralgetriebe;
- erfolgreiche Platzierung solcher Einheiten wie Hochdruck-Luftkompressor mit eigenen Systemen, Starter-Generator usw.
Nach Beibehaltung der Queranordnung des Motors mit einem Zweiwege-Nebenantrieb und zwei Planeten-Bordgetrieben auf beiden Seiten des Motors verlagerten sich die Konstrukteure auf die freien Plätze an den Seiten des Motors, parallel zu den Getrieben, der Kompressor und die Gasturbine, die zuvor in 4TD oben auf dem Motorblock montiert waren. Das neue Layout ermöglichte es, das Volumen des MTO im Vergleich zum T-54-Panzer zu halbieren, und traditionelle Komponenten wie das Zentralgetriebe, das Getriebe, die Hauptkupplung, die Bordplanetenschwingmechanismen, die Achsantriebe und die Bremsen wurden davon ausgeschlossen. Wie später im GBTU-Bericht erwähnt, sparte der neue Getriebetyp 750 kg Masse und bestand aus 150 bearbeiteten Teilen statt wie bisher 500.
Alle Motorservicesysteme waren über dem Dieselmotor verriegelt und bildeten den "zweiten Stock" des MTO, dessen Schema "zweistufig" genannt wurde.
Die hohe Leistung des 5TD-Motors erforderte die Verwendung einer Reihe neuer grundlegender Lösungen und spezieller Materialien in seiner Konstruktion. Der Kolben für diesen Diesel beispielsweise wurde mit einem Heizkissen und einem Distanzstück hergestellt.
Der erste Kolbenring war ein kontinuierlicher Flammenring vom Lippentyp. Die Zylinder waren aus Stahl, verchromt.
Die Möglichkeit, den Motor mit hohem Entspannungsdruck zu betreiben, wurde durch den Leistungskreis des Motors mit tragenden Stahlbolzen, einem von Gaskräften entlasteten Aluminiumgussblock und dem Fehlen eines Gasgelenks gewährleistet. Die Verbesserung des Spül- und Füllvorgangs der Zylinder (und das ist bei allen 2-Takt-Dieselmotoren ein Problem) wurde bis zu einem gewissen Grad durch das gasdynamische Schema unter Ausnutzung der kinetischen Energie der Abgase und des Ausstoßeffekts erleichtert.
Das Strahl-Wirbel-Gemischbildungssystem, bei dem Art und Richtung der Brennstoffstrahlen auf die Luftbewegungsrichtung abgestimmt sind, sorgte für eine effektive Verwirbelung des Brennstoff-Luft-Gemisches, was zur Verbesserung des Wärme- und Stoffübergangsprozesses beitrug.
Durch die speziell gewählte Form der Brennkammer konnte zudem der Misch- und Verbrennungsprozess verbessert werden. Die Hauptlagerdeckel wurden durch Stahlschrauben mit dem Kurbelgehäuse zusammengezogen, wobei die Last aus den auf den Kolben wirkenden Gaskräften genommen wurde.
An einem Ende des Kurbelgehäuseblocks wurde eine Platte mit einer Turbine und einer Wasserpumpe befestigt, und an der gegenüberliegenden Seite wurden eine Platte des Hauptgetriebes und Abdeckungen mit Antrieben für Kompressor, Regler, Drehzahlmesser, Hochdruckkompressor und Luftverteiler angebracht Ende.
Im Januar 1957 wurde der erste Prototyp des 5TD-Tankdieselmotors für Prüfstandsversuche vorbereitet. Am Ende der Prüfstandstests wurde der 5TD im selben Jahr für Objekt- (See-)Erprobungen in einen Versuchstank "Objekt 430" überführt und bestand bis Mai 1958 die abteilungsübergreifenden staatlichen Tests mit einer guten Note.
Trotzdem wurde entschieden, den 5TD-Diesel nicht in die Massenproduktion zu überführen. Grund waren erneut die geänderten Anforderungen des Militärs an neue Panzer, die erneut eine Leistungssteigerung erforderlich machten. Unter Berücksichtigung der sehr hohen technischen und wirtschaftlichen Kennwerte des 5TD-Motors und der darin enthaltenen Reserven (die auch durch Tests nachgewiesen wurden) ein neues Kraftwerk mit einer Leistung von etwa 700 PS. beschlossen, auf seiner Grundlage zu erstellen.
Die Schaffung eines solchen Originalmotors für das Werk für Verkehrstechnik in Kharkov erforderte die Herstellung bedeutender technologischer Geräte, eine große Anzahl von Prototypen eines Dieselmotors und wiederholte Langzeittests. Es ist zu beachten, dass die Konstruktionsabteilung des Werks später zum Konstruktionsbüro für Maschinenbau in Kharkov (KHKBD) wurde und die Motorenproduktion nach dem Krieg praktisch von Grund auf neu geschaffen wurde.
Gleichzeitig mit der Konstruktion des Dieselmotors wurde im Werk ein großer Komplex von Versuchsständen und verschiedenen Installationen (24 Einheiten) geschaffen, um die Elemente seiner Konstruktion und seines Arbeitsablaufs zu testen. Dies half sehr, die Konstruktionen von Aggregaten wie Kompressor, Turbine, Kraftstoffpumpe, Abgaskrümmer, Zentrifuge, Wasser- und Ölpumpen, Blockkurbelgehäuse usw. zu überprüfen und auszuarbeiten, aber ihre Entwicklung ging weiter.
Im Jahr 1959 wurde es auf Wunsch des Chefkonstrukteurs des neuen Panzers (AA Morozov), für den dieser Dieselmotor zu diesem Zweck entwickelt wurde, als notwendig erachtet, seine Leistung von 426 kW (580 PS) auf 515 kW (700.) zu erhöhen PS).). Die erzwungene Version des Motors wurde 5TDF genannt.
Durch die Erhöhung der Drehzahl des Ladekompressors wurde die Literleistung des Motors erhöht. Durch den forcierten Dieselmotor traten jedoch neue Probleme auf, vor allem in der Zuverlässigkeit von Komponenten und Baugruppen.
Die Konstrukteure von KhKBD, NIID, VNIITransmash, Technologen der Anlagen und Institute VNITI und TsNITI (seit 1965) haben viel Berechnungs-, Forschungs-, Konstruktions- und Technologiearbeit geleistet, um die erforderliche Zuverlässigkeit und Betriebsdauer des 5TDF-Dieselmotors zu erreichen.
Als schwierigste Probleme erwiesen sich die Probleme der Erhöhung der Zuverlässigkeit der Kolbengruppe, der Kraftstoffausrüstung und des Turboladers. Jede, auch nur unwesentliche Verbesserung war nur durch eine ganze Reihe gestalterischer, technologischer, organisatorischer (Produktions-) Maßnahmen gegeben.
Die erste Charge von 5TDF-Dieselmotoren zeichnete sich durch große Instabilität in der Qualität der Teile und Baugruppen aus. Ein bestimmter Teil der Dieselmotoren aus der produzierten Serie (Charge) hat die etablierte Garantielaufzeit (300 Stunden) erreicht. Gleichzeitig wurde ein erheblicher Teil der Motoren aufgrund bestimmter Mängel vor der Garantielaufzeit von den Ständen entfernt.
Die Besonderheit eines schnelllaufenden 2-Takt-Dieselmotors liegt in einem komplexeren Gaswechselsystem als bei einem 4-Takt, erhöhtem Luftverbrauch und einer höheren Wärmebelastung der Kolbengruppe. Daher Steifigkeit und Vibrationsfestigkeit der Struktur, strengere Einhaltung der geometrischen Form einer Reihe von Teilen, hohe Anti-Seize-Eigenschaften und Verschleißfestigkeit der Zylinder, Hitzebeständigkeit und mechanische Festigkeit der Kolben, sorgfältige dosierte Zufuhr und Entfernung von Zylinderschmiermittel und eine Verbesserung der Qualität der Reibflächen erforderlich. Um diesen Besonderheiten von 2-Takt-Motoren Rechnung zu tragen, mussten komplexe konstruktive und technologische Probleme gelöst werden.
Eines der kritischsten Teile für die präzise Gasverteilung und den Schutz der Kolbendichtringe vor Überhitzung war ein dünnwandiger Manschettenflammring aus Stahl mit Gewinde und einer speziellen Gleitbeschichtung. Bei der Verfeinerung des 5TDF-Dieselmotors ist das Problem der Funktionsfähigkeit dieses Rings zu einem der Hauptprobleme geworden. Bei der Feinabstimmung kam es lange Zeit zu Fressen und Brüchen der Flammringe durch Verformung ihrer Auflagefläche, suboptimale Konfiguration sowohl des Rings selbst als auch des Kolbenkörpers, ungenügende Verchromung der Ringe, unzureichende Schmierung, ungleichmäßige Kraftstoffzufuhr durch Düsen, Abplatzen von Zunder und Salzablagerungen an der Kolbenauskleidung sowie durch Staubabrieb bei unzureichender Reinigung der vom Motor angesaugten Luft.
Nur als Ergebnis langer und harter Arbeit vieler Spezialisten der Anlagen und Forschungs- und Technologieinstitute wurden die Konfiguration des Kolbens und des Flammrings verbessert, die Fertigungstechnologie verbessert, die Elemente der Brennstoffausrüstung verbessert, die Die Schmierung wird verbessert, der Einsatz effektiverer Gleitbeschichtungen sowie die Verfeinerung des Luftreinigungssystems Fehler im Zusammenhang mit dem Betrieb des Flammrings wurden praktisch eliminiert.
Durch die Reduzierung des Axialspiels zwischen Ring und Kolbennut, die Verbesserung des Materials, die Änderung des Querschnitts des Rings (von trapez- auf rechteckig umgestellt) und die Weiterentwicklung der Technik wurden Ausfälle von trapezförmigen Kolbenringen beseitigt zur Herstellung der Ringe. Brüche der Kolbenbüchsenschrauben wurden durch erneutes Einfädeln und Verriegeln, Anziehen von Fertigungskontrollen, Anziehen der Drehmomentgrenzen und Verwendung eines verbesserten Schraubenmaterials repariert.
Die Stabilität des Ölverbrauchs wurde durch eine Erhöhung der Steifigkeit der Zylinder, eine Verringerung der Ausschnitte an den Enden der Zylinder und eine straffere Kontrolle bei der Herstellung von Ölsammelringen erreicht.
Durch Feinabstimmung der Elemente der Brennstoffausrüstung und Verbesserung des Gasaustauschs wurde eine gewisse Verbesserung der Brennstoffeffizienz und eine Verringerung des maximalen Flash-Drucks erreicht.
Durch die Verbesserung der Qualität des verwendeten Gummis und die Straffung des Spaltes zwischen Zylinder und Block wurden Fälle von Kühlmittelaustritt durch die Gummidichtringe eliminiert.
In Verbindung mit einer deutlichen Erhöhung der Übersetzung von der Kurbelwelle zum Lader zeigten einige 5TDF-Dieselmotoren Mängel wie Schlupf und Verschleiß der Reibkupplungsscheiben, Ausfälle des Laderrades und Ausfall seiner Lager, die bei der 5TD-Dieselmotor. Um sie zu eliminieren, waren Maßnahmen wie die Wahl des optimalen Anzugs des Reibkupplungsscheibenpakets, die Erhöhung der Anzahl der Scheiben im Paket, die Eliminierung von Spannungskonzentratoren im Kompressorlaufrad, das Vibrieren des Rades, die Erhöhung der Dämpfungseigenschaften von Unterstützung und Auswahl besserer Lager. Dadurch konnten die Mängel, die sich aus der Kraftübertragung des Dieselmotors ergaben, beseitigt werden.
Die Erhöhung der Zuverlässigkeit und Betriebsdauer des 5TDF-Dieselmotors hat maßgeblich dazu beigetragen, höherwertige Öle mit speziellen Additiven zu verwenden.
An den Ständen von VNIITransmash wurden unter Beteiligung von KKBD- und NIID-Mitarbeitern umfangreiche Untersuchungen zum Betrieb des 5TDF-Dieselmotors unter realen Staubbedingungen der Ansaugluft durchgeführt. Sie gipfelten schließlich in einem erfolgreichen "Staub"-Test des Motors über 500 Betriebsstunden. Dies bestätigte den hohen Entwicklungsstand der Zylinder-Kolben-Gruppe des Dieselmotors und des Luftreinigungssystems.
Parallel zur Feinabstimmung des Diesels selbst wurde dieser immer wieder in Verbindung mit den Kraftwerkssystemen getestet. Gleichzeitig wurden die Systeme verbessert, die Frage nach ihrer Vernetzung und ihrem zuverlässigen Betrieb im Tank gelöst.
L. L. Golinets war der Chefkonstrukteur des KHKBD in der entscheidenden Phase der Feinabstimmung des 5TDF-Dieselmotors. Der ehemalige Chefdesigner A. D. Charomsky ging in den Ruhestand und war weiterhin als Berater am Feinschliff beteiligt.
Die Entwicklung der Serienproduktion des 5TDF-Dieselmotors in neuen, speziell gebauten Werkstätten des Werks mit neuen Kadern von Arbeitern und Ingenieuren, die an diesem Motor studierten, verursachte viele Schwierigkeiten, die Teilnahme von Spezialisten anderer Organisationen.
Bis 1965 wurde der 5TDF-Motor in separaten Serien (Losen) produziert. Jede Folgeserie beinhaltete eine Reihe von Maßnahmen, die an den Ständen entwickelt und getestet wurden, um Mängel zu beseitigen, die bei der Erprobung und im Probebetrieb in der Bundeswehr festgestellt wurden.
Die tatsächliche Betriebszeit der Triebwerke überschritt jedoch 100 Stunden nicht.
Ein bedeutender Durchbruch bei der Verbesserung der Zuverlässigkeit des Diesels erfolgte Anfang 1965. Zu diesem Zeitpunkt wurden zahlreiche Änderungen an Design und Technologie der Herstellung vorgenommen. Diese in die Produktion eingeführten Änderungen ermöglichten es, die Betriebszeit der nächsten Motorenserie auf bis zu 300 Stunden zu erhöhen. Langzeittests von Panzern mit Motoren dieser Baureihe bestätigten die deutlich erhöhte Zuverlässigkeit von Dieselmotoren: Alle Motoren arbeiteten während dieser Tests 300 Stunden, und einige von ihnen (selektiv) arbeiteten in Fortsetzung der Tests jeweils 400 … 500 Stunden.
1965 wurde schließlich eine Einbaucharge von Dieselmotoren gemäß der korrigierten technischen Zeichnungsdokumentation und Technik für die Serienfertigung freigegeben. Im Jahr 1965 wurden insgesamt 200 Serienmotoren hergestellt. Der Produktionshochlauf begann und erreichte 1980 seinen Höhepunkt. Im September 1966 bestand der 5TDF-Dieselmotor abteilungsübergreifende Tests.
In Anbetracht der Entstehungsgeschichte des 5TDF-Dieselmotors ist der Fortschritt seiner technologischen Entwicklung als völlig neuer Motor für die Produktion des Werks zu erwähnen. Fast zeitgleich mit der Herstellung von Prototypen des Motors und seiner konstruktiven Verfeinerung wurde seine technologische Entwicklung und der Bau neuer Produktionsanlagen des Werks und deren Ausstattung mit Ausrüstung durchgeführt.
Nach den überarbeiteten Zeichnungen der ersten Motormuster begann bereits 1960 die Entwicklung der Konstruktionstechnologie für die Herstellung von 5TDF, und 1961 begann die Erstellung der technologischen Arbeitsdokumentation. Die Konstruktionsmerkmale eines 2-Takt-Dieselmotors, die Verwendung neuer Materialien, die hohe Genauigkeit seiner Einzelteile und Komponenten erforderten von der Technologie grundlegend neue Verfahren bei der Verarbeitung und sogar beim Zusammenbau des Motors. Die Gestaltung der technologischen Prozesse und ihrer Ausrüstung wurde sowohl von den technologischen Diensten des Werks unter der Leitung von A. I. Isaev, V. D. Dyachenko, V. I. Doschechkin und anderen als auch von Mitarbeitern der technologischen Institute der Industrie durchgeführt. Spezialisten des Central Research Institute of Materials (Direktor F. A. Kupriyanov) waren an der Lösung vieler metallurgischer und materialwissenschaftlicher Probleme beteiligt.
Der Bau neuer Werkstätten für die Motorenproduktion des Kharkov Transport Engineering Plant wurde nach dem Projekt des Sojusmashproekt-Instituts (Hauptprojektingenieur S. I. Shpynov) durchgeführt.
Während 1964-1967. Die neue Dieselproduktion wurde mit der Ausrüstung (insbesondere Sondermaschinen - mehr als 100 Einheiten) vervollständigt, ohne die die Serienproduktion von Dieselteilen praktisch nicht zu organisieren wäre. Dies waren Diamantbohr- und Mehrspindelmaschinen für die Blockbearbeitung, spezielle Dreh- und Schlichtmaschinen für die Bearbeitung von Kurbelwellen usw. Vor der Inbetriebnahme neuer Werkstätten und Testbereiche und der Fehlersuche in der Fertigungstechnik für eine Reihe von Hauptteilen sowie der Fertigung von Einbauchargen und der ersten Serie des Motors wurden temporär Rümpfe großer Diesellokomotiven in der Produktion organisiert Websites.
Die Inbetriebnahme der Hauptkapazitäten der neuen Dieselproduktion erfolgte abwechselnd im Zeitraum 1964-1967. In den neuen Werkstätten wurde ein vollständiger Zyklus der 5TDF-Dieselproduktion bereitgestellt, mit Ausnahme der Platinenproduktion am Hauptstandort des Werks.
Bei der Bildung neuer Produktionsstätten wurde viel Wert auf die Erhöhung des Niveaus und der Organisation der Produktion gelegt. Die Produktion eines Dieselmotors wurde nach dem Linien- und Gruppenprinzip organisiert, wobei die neuesten Errungenschaften dieser Zeit auf diesem Gebiet berücksichtigt wurden. Es wurden die fortschrittlichsten Mittel zur Mechanisierung und Automatisierung der Teilebearbeitung und Montage verwendet, die die Schaffung einer umfassend mechanisierten Produktion des 5TDF-Dieselmotors gewährleisteten.
Im Prozess der Umformproduktion wurde eine große gemeinsame Arbeit von Technologen und Konstrukteuren durchgeführt, um die Herstellbarkeit des Dieselmotors zu verbessern, wobei die Technologen dem KHKBD etwa sechstausend Vorschläge unterbreiteten, von denen sich ein erheblicher Teil in der Konstruktionsdokumentation des Motors.
Auf technischem Niveau übertraf die neue Dieselproduktion die Indikatoren der Industrieunternehmen, die bis dahin vergleichbare Produkte herstellten, deutlich. Der Ausrüstungsfaktor der 5TDF-Dieselproduktionsverfahren hat einen hohen Wert erreicht - 6, 22. In nur 3 Jahren wurden mehr als 10 Tausend technologische Prozesse entwickelt, mehr als 50 Tausend Ausrüstungsgegenstände entworfen und hergestellt. Eine Reihe von Unternehmen des Wirtschaftsrates von Charkow waren an der Herstellung von Geräten und Werkzeugen beteiligt, um das Werk Malyshev zu unterstützen.
In den Folgejahren (nach 1965) arbeiteten die technologischen Dienste des Werks und TsNITI bereits im Zuge der Serienproduktion des 5TDF-Dieselmotors an der weiteren Verbesserung der Technologien, um die Arbeitsintensität zu reduzieren, die Qualität und Zuverlässigkeit der Motor. Mitarbeiter von TsNITI (Direktor Ya. A. Shifrin, Chefingenieur B. N. Surnin) in den Jahren 1967-1970. mehr als 4500 technologische Vorschläge wurden entwickelt, die eine Reduzierung der Arbeitsintensität um mehr als 530 Standardstunden und eine signifikante Reduzierung der Verluste durch Schrott während der Produktion ermöglichen. Gleichzeitig konnten durch diese Maßnahmen die Anzahl der Montagevorgänge und das selektive Fügen von Teilen mehr als halbiert werden. Das Ergebnis der Umsetzung eines Komplexes von konstruktiven und technologischen Maßnahmen war ein zuverlässigerer und hochwertigerer Betrieb des Motors im Betrieb mit einer garantierten Betriebszeit von 300 Stunden. Aber die Arbeit der Technologen des Werks und von TsNITI zusammen mit den Designern des KHKBD ging weiter. Es war notwendig, die Betriebszeit des 5TDF-Motors um das 1,5 … 2,0-fache zu erhöhen. Auch diese Aufgabe ist gelöst. Der 2-Takt-Tankdieselmotor 5TDF wurde modifiziert und im Kharkov Transport Engineering Plant in Produktion genommen.
Eine sehr wichtige Rolle bei der Organisation der Produktion von Diesel 5TDF spielte der Direktor des Werks O. A. Soich sowie eine Reihe von Branchenführern (D. F. Ustinov, E. P. Shkurko, I. F. Dmitriev usw.), die ständig den Fortschritt und die Entwicklung von Dieselproduktion sowie diejenigen, die direkt an der Lösung technischer und organisatorischer Probleme beteiligt waren.
Autonome Fackelheizungen und Öleinspritzsysteme ermöglichten erstmals (1978) einen Kaltstart eines Tankdieselmotors bei Temperaturen bis -20 Grad C (von 1984 bis -25 Grad C). Später (1985) war es mit Hilfe des PVV-Systems (Ansaugluftheizung) möglich, einen Kaltstart eines Viertakt-Dieselmotors (V-84-1) an T-72-Tanks durchzuführen, jedoch nur bis zu eine Temperatur von -20 Grad C und nicht mehr als zwanzig Starts innerhalb der Garantieressource.
Am wichtigsten ist, dass 5TDF bei den Dieseln der 6TD-Reihe (6TD-1… 6TD-4) mit einem Leistungsbereich von 1000-1500 PS reibungslos auf eine neue Qualität umgestellt wurde.und Übertreffen ausländischer Analoga in einer Reihe von grundlegenden Parametern.
INFORMATIONEN ZUM MOTORBETRIEB
Angewandte Betriebsmittel
Der Hauptkraftstoff zum Antrieb des Motors ist Kraftstoff für schnelllaufende Dieselmotoren GOST 4749-73:
bei einer Umgebungstemperatur von nicht weniger als + 5 ° С - Marke DL;
bei Umgebungstemperaturen von +5 bis -30 ° С - DZ-Marken;
bei einer Umgebungstemperatur unter -30 ° С - Marke DA.
Bei Bedarf darf DZ-Kraftstoff bei Umgebungstemperaturen über + 50 ° C verwendet werden.
Neben Kraftstoff für schnelllaufende Dieselmotoren kann der Motor mit Düsentreibstoff TC-1 GOST 10227-62 oder Motorbenzin A-72 GOST 2084-67 sowie mit Kraftstoffgemischen in beliebigen Anteilen betrieben werden.
Öl M16-IHP-3 TU 001226-75 wird zur Motorschmierung verwendet. In Abwesenheit dieses Öls ist die Verwendung von MT-16p-Öl zulässig.
Beim Ölwechsel muss das Restöl aus dem Kurbelgehäuse des Motors und dem Öltank der Maschine abgelassen werden.
Das Vermischen der verwendeten Öle untereinander sowie die Verwendung von Ölen anderer Marken ist untersagt. Es ist erlaubt, im Ölsystem die nicht ablaufenden Rückstände einer Ölmarke mit einer anderen zu mischen, die nachgefüllt wird.
Beim Ablassen darf die Öltemperatur nicht unter +40 °C liegen.
Um den Motor bei einer Umgebungstemperatur von mindestens + 5 ° C zu kühlen, wird reines Frischwasser ohne mechanische Verunreinigungen verwendet, das durch einen speziellen Filter geleitet wird, der dem EC der Maschine zugeführt wird.
Um den Motor vor Korrosion und Säurebildung zu schützen, wird dem durch den Filter geleiteten Wasser 0,15% eines Dreikomponenten-Additivs (0,05% jeder Komponente) zugesetzt.
Das Additiv besteht aus Trinatriumphosphat GOST 201-58, Kaliumchrompeak GOST 2652-71 und Natriumnitrit GOST 6194-69 muss zuerst in 5-6 Liter Wasser gelöst werden, das durch einen chemischen Filter geleitet und auf eine Temperatur von 60-80 ° C erhitzt wird °C. Beim Auftanken von 2-3 Litern darf (einmalig) Wasser ohne Zusätze verwendet werden.
Gießen Sie Korrosionsschutzadditiv nicht direkt in das System.
In Abwesenheit eines Dreikomponenten-Additivs darf ein reiner Chrompeak von 0,5% verwendet werden.
Bei einer Umgebungstemperatur unter + 50 ° C sollte eine Flüssigkeit mit niedrigem Frost (Frostschutzmittel) von „40“oder „65“GOST 159-52 verwendet werden. Frostschutzmarke "40" wird bei Umgebungstemperaturen bis -35 ° C verwendet, bei Temperaturen unter -35 ° C - Frostschutzmarke "65".
Befüllen Sie den Motor mit Kraftstoff, Öl und Kühlmittel unter Beachtung der Maßnahmen, um das Eindringen von mechanischen Verunreinigungen und Staub sowie Feuchtigkeit in Kraftstoff und Öl zu verhindern.
Es wird empfohlen, mit Hilfe spezieller Tankwagen oder einer regulären Betankungsvorrichtung (bei Betankung aus separaten Behältern) zu tanken.
Kraftstoff muss über einen Seidenfilter nachgefüllt werden. Es wird empfohlen, das Öl mit Hilfe von speziellen Ölfüllern einzufüllen. Füllen Sie Öl, Wasser und Flüssigkeit mit niedrigem Gefrierpunkt durch einen Filter mit Maschen Nr. 0224 GOST 6613-53.
Befüllen Sie die Systeme bis zu den in der Betriebsanleitung der Maschine angegebenen Füllständen.
Um die Volumina der Schmier- und Kühlsysteme vollständig zu füllen, starten Sie den Motor nach dem Auftanken 1-2 Minuten lang, überprüfen Sie dann die Füllstände und betanken Sie die Systeme ggf.
Während des Betriebs ist es erforderlich, die Kühlmittel- und Ölmenge in den Motorsystemen zu kontrollieren und deren IB-Werte innerhalb der angegebenen Grenzen zu halten.
Lassen Sie den Motor nicht laufen, wenn sich weniger als 20 Liter Öl im Motorschmiertank befinden.
Wenn der Kühlmittelstand durch Verdunstung sinkt oder in das Kühlsystem austritt, Wasser bzw. Frostschutzmittel nachfüllen.
Lassen Sie Kühlmittel und Öl durch die speziellen Ablassventile des Motors und der Maschine (Heizkessel und Öltank) mit einem Schlauch mit Anschlussstück mit offenen Einfüllöffnungen ab. Um das restliche Wasser vollständig aus dem Kühlsystem zu entfernen und ein Einfrieren zu vermeiden, wird empfohlen, das System mit 5-6 Litern Flüssigkeit mit niedrigem Gefrierpunkt zu verschütten.
Merkmale des Motorbetriebs mit verschiedenen Kraftstoffarten
Der Motorbetrieb mit verschiedenen Kraftstoffarten wird durch einen Kraftstoffzufuhr-Steuerungsmechanismus ausgeführt, der zwei Positionen zum Einstellen des Multi-Kraftstoff-Hebels hat: Betrieb mit Kraftstoff für schnelllaufende Dieselmotoren, Kraftstoff für Düsentriebwerke, Benzin (mit Leistungsabfall) und deren Mischungen in beliebigen Anteilen; nur mit Benzin arbeiten.
Der Betrieb mit anderen Kraftstoffarten mit dieser Hebelstellung ist strengstens untersagt.
Der Einbau der Kraftstoffzufuhrsteuerung aus der Position „Betrieb mit Dieselkraftstoff“in die Position „Betrieb mit Benzin“erfolgt durch Drehen der Einstellschraube des Multi-Brennstoffhebels im Uhrzeigersinn bis zum Anschlag und aus der Position „Betrieb ein Benzin" auf die Position "Betrieb mit Dieselkraftstoff" - indem Sie die Mehrkraftstoffhebel-Einstellschraube gegen den Uhrzeigersinn bis zum Anschlag drehen.
Merkmale zum Starten und Betreiben des Motors beim Betrieb mit Benzin. Mindestens 2 Minuten vor dem Anlassen des Motors ist es notwendig, die BCN-Pumpe der Maschine einzuschalten und den Kraftstoff mit der manuellen Ansaugpumpe der Maschine intensiv zu pumpen; In jedem Fall, unabhängig von der Umgebungstemperatur, vor dem Start zweimal Öl in die Zylinder einspritzen.
Die Benzinkreiselpumpe der Maschine muss während des gesamten Betriebs des Motors mit Benzin, seinen Gemischen mit anderen Kraftstoffen und bei kurzen Stillstandszeiten (3-5 Minuten) der Maschine eingeschaltet bleiben.
Die minimale konstante Leerlaufdrehzahl bei Benzinbetrieb beträgt 1000 pro Minute.
BEDIENUNGSMERKMALE
S. Suvorov erinnert in seinem Buch "T-64" an die Vor- und Nachteile dieses Motors.
Bei den seit 1975 produzierten T-64A-Panzern wurde auch die Panzerung des Turms durch die Verwendung von Korundfüller verstärkt.
Bei diesen Maschinen wurde auch das Fassungsvermögen der Kraftstofftanks von 1093 Liter auf 1270 Liter erhöht, wodurch auf der Rückseite des Turms eine Kiste zum Verstauen von Ersatzteilen erschien. Bei Maschinen früherer Versionen wurden Ersatzteile und Zubehör in Kästen auf den rechten Kotflügeln platziert, wo zusätzliche Kraftstofftanks installiert und an das Kraftstoffsystem angeschlossen wurden. Wenn der Fahrer das Kraftstoffverteilerventil an einer beliebigen Tankgruppe (hinten oder vorne) installierte, wurde der Kraftstoff hauptsächlich aus den externen Tanks hergestellt.
Im Kettenspannmechanismus wurde ein Schneckengetriebe verwendet, das einen wartungsfreien Betrieb während der gesamten Lebensdauer des Panzers ermöglichte.
Die Leistungsmerkmale dieser Maschinen wurden stark verbessert. So wurde beispielsweise der Versuch vor dem nächsten Nummerndienst von 1500 bzw. 3000 km auf 2500 bzw. 5000 km für T01 bzw. TO erhöht. Zum Vergleich: Beim T-62 TO1 wurde der TO2-Panzer nach 1000 und 2000 km Lauf und beim T-72-Panzer nach 1600-1800 bzw. 3300-3500 Laufkilometern durchgeführt. Die Garantiezeit für den 5TDF-Motor wurde von 250 auf 500 Stunden erhöht, die Garantiezeit für die gesamte Maschine betrug 5.000 km.
Aber die Schule ist nur ein Auftakt, der Haupteinsatz begann bei der Truppe, wo ich nach meinem Abitur 1978 landete. Kurz vor dem Abschluss wurde uns der Befehl des Oberbefehlshabers der Bodentruppen mitgeteilt, dass die Absolventen unserer Schule nur an die Verbände verteilt werden sollten, in denen es T-64-Panzer gibt. Dies war darauf zurückzuführen, dass es in der Truppe Fälle von Massenversagen von T-64-Panzern gab, insbesondere von 5TDF-Motoren. Der Grund - Unkenntnis des Materials und der Betriebsregeln dieser Tanks. Die Einführung des T-64-Panzers war vergleichbar mit dem Übergang in der Luftfahrt von Kolbenmotoren zu Düsentriebwerken - Luftfahrtveteranen erinnern sich daran, wie es war.
Was den 5TDF-Motor angeht, gab es zwei Hauptgründe für sein Versagen bei den Truppen - Überhitzung und Staubverschleiß. Beide Gründe waren auf Unkenntnis oder Vernachlässigung der Betriebsvorschriften zurückzuführen. Der Hauptnachteil dieses Motors ist, dass er nicht für Idioten ausgelegt ist, manchmal erfordert es, dass sie das tun, was in der Bedienungsanleitung steht. Als ich bereits Kommandant einer Panzerkompanie war, begann einer meiner Zugführer, ein Absolvent der Panzerschule Tscheljabinsk, die Offiziere für T-72-Panzer ausbildete, irgendwie das Kraftwerk des T-64-Panzers zu kritisieren. Der Motor und die Häufigkeit seiner Wartung gefielen ihm nicht. Aber als ihm die Frage gestellt wurde "Wie oft haben Sie in sechs Monaten die Dächer des MTO auf Ihren drei Trainingstanks geöffnet und in den Motor-Getriebe-Raum geschaut?" Es stellte sich heraus, dass nie. Und die Panzer gingen, boten Kampftraining an.
Und so weiter der Reihe nach. Eine Überhitzung des Motors trat aus mehreren Gründen auf. Zuerst vergaß der Mechaniker, die Matte vom Kühler zu entfernen und schaute dann nicht auf die Instrumente, was aber sehr selten und in der Regel im Winter passierte. Die zweite und wichtigste ist das Befüllen mit Kühlmittel. Laut Anleitung soll Wasser (während der Sommerbetriebszeit) mit einem Dreikomponenten-Additiv eingefüllt werden, und Wasser muss durch einen speziellen Sulfofilter eingefüllt werden, mit dem alle Early-Release-Maschinen ausgestattet waren, und auf neue Maschinen wurde pro Firma (10-13 Panzer) ein solcher Filter ausgegeben. Triebwerke fielen aus, hauptsächlich der Panzer der Ausbildungsgruppe des Einsatzes, die an mindestens fünf Tagen in der Woche betrieben wurden und sich in der Regel auf Schießständen in Feldparks befinden. Gleichzeitig konnten es sich die Fahrer-Mechanik-"Lehrbücher" (die sogenannten Mechaniker von Trainingsmaschinen), in der Regel harte Arbeiter und gewissenhafte Typen, die aber die Feinheiten des Motors nicht kannten, manchmal leisten, Wasser hineinzugießen das Kühlsystem direkt aus dem Wasserhahn, zumal der Sulfofilter (der pro Unternehmen einer ist) normalerweise im Winterquartier irgendwo im Spind des Chief Technical Officer des Unternehmens aufbewahrt wurde. Die Folge sind Kesselsteinbildung in den dünnen Kanälen des Kühlsystems (im Bereich der Brennräume), fehlende Flüssigkeitszirkulation im heißesten Teil des Motors, Überhitzung und Motorausfall. Die Kalkbildung wurde dadurch verstärkt, dass das Wasser in Deutschland sehr hart ist.
In einer benachbarten Einheit angekommen, wurde der Motor wegen Überhitzung durch Verschulden des Fahrers ausgebaut. Nachdem er auf Anraten eines der "Experten" ein kleines Kühlmittelleck aus dem Kühler gefunden hatte, um dem System Senf hinzuzufügen, kaufte er im Laden eine Packung Senf und goss alles in das System ein - Verstopfung von Kanälen und Motorausfall.
Auch beim Kühlsystem gab es weitere Überraschungen. Plötzlich beginnt es Kühlmittel aus dem Kühlsystem durch ein Dampf-Luft-Ventil (PVK) auszustoßen. Einige, die nicht verstehen, worum es geht, versuchen, es vom Schlepper aus zu starten - das Ergebnis der Zerstörung des Motors. So machte mir der stellvertretende Chef meines Bataillons ein "Geschenk" für das neue Jahr, und ich musste am 31. Dezember den Motor wechseln. Ich hatte vor Neujahr Zeit, weil Der Austausch des Motors an einem T-64-Tank ist kein sehr kompliziertes Verfahren und erfordert vor allem keine Ausrichtung beim Einbau. Die meiste Zeit beim Austausch eines Motors an einem T-64-Tank, wie bei allen Haushaltstanks, wird durch das Ablassen und Auftanken von Öl und Kühlmittel benötigt. Wenn unsere Panzer Anschlüsse mit Ventilen anstelle von Durit-Anschlüssen hätten, wie bei Leoparden oder Leclercs, dann würde der rechtzeitige Austausch des Motors bei T-64- oder T-80-Panzern nicht länger dauern als der Austausch des gesamten Triebwerks bei den westlichen Panzern. An jenem denkwürdigen Tag, dem 31. Dezember 1980, zum Beispiel, „warrant Officer E. Sokolov“und ich, nachdem wir Öl und Kühlmittel abgelassen hatten, den Motor in nur 15 Minuten aus dem MTO „warfen“.
Der zweite Grund für den Ausfall von 5TDF-Motoren ist Staubverschleiß. Luftreinigungssystem. Wenn Sie den Kühlmittelstand nicht rechtzeitig kontrollieren, sondern vor jedem Austritt der Maschine überprüfen sollten, kann es vorkommen, dass sich im oberen Teil des Kühlmantels keine Flüssigkeit befindet und es zu einer lokalen Überhitzung kommt. Der schwächste Punkt ist in diesem Fall die Düse. In diesem Fall brennen die Injektordichtungen oder der Injektor selbst versagt, dann durchbrechen Gase aus den Zylindern durch Risse oder verbrannte Dichtungen in das Kühlsystem und unter ihrem Druck wird die Flüssigkeit durch das PVCL ausgestoßen. All dies ist nicht tödlich für den Motor und wird beseitigt, wenn sich eine sachkundige Person im Gerät befindet. Bei herkömmlichen Reihen- und V-Motoren in einer ähnlichen Situation "führt" die Zylinderkopfdichtung, und in diesem Fall wird mehr Arbeit anfallen.
Wenn in einer solchen Situation der Motor gestoppt wird und keine Maßnahmen ergriffen werden, beginnen sich die Zylinder nach einiger Zeit mit Kühlmittel zu füllen, der Motor ist ein Trägheitsgitter und ein Zyklonluftfilter. Der Luftfilter wird laut Bedienungsanleitung bei Bedarf gespült. Bei Panzern des Typs T-62 wurde es im Winter nach 1000 km und im Sommer nach 500 km gewaschen. Auf einem T-64-Panzer - nach Bedarf. Hier kommt der Stolperstein ins Spiel - manche hielten es für die Tatsache, dass man ihn gar nicht waschen muss. Die Notwendigkeit entstand, als Öl in die Zyklone gelangte. Und wenn mindestens einer der 144 Zyklone Öl enthält, dann muss der Luftfilter gespült werden, denn durch diesen zyklon gelangt ungereinigte luft mit staub in den motor, und dann werden wie schmirgel die zylinderlaufbuchsen und kolbenringe gelöscht. Der Motor verliert an Leistung, der Ölverbrauch steigt und startet dann ganz.
Es ist nicht schwer, das Eindringen von Öl in die Zyklone zu überprüfen - schauen Sie sich einfach die Zykloneinlässe am Luftfilter an. Normalerweise haben sie sich das Staubableitungsrohr des Luftfilters angesehen, und wenn Öl darauf gefunden wurde, haben sie sich den Luftfilter angesehen und ihn gegebenenfalls gewaschen. Woher kam das Öl? Ganz einfach: Der Einfüllstutzen des Öltanks der Motorschmieranlage befindet sich neben dem Lufteinlassgitter. Beim Tanken mit Öl wird meist eine Gießkanne verwendet, aber da an den Trainingsmaschinen fehlten in der Regel Gießkannen (jemand hat sich verloren, jemand hat es auf ein Raupenband gelegt, vergessen und durchgefahren usw.), dann gossen die Mechaniker einfach Öl aus Eimern, während Öl verschüttet wurde, fiel zuerst auf das Lufteinlassgitter und dann in den Luftfilter. Auch beim Einfüllen von Öl durch eine Gießkanne, aber bei windigem Wetter, spritzte der Wind das Öl auf das Luftfiltergitter. Daher forderte ich beim Auftanken des Öls von meinen Untergebenen, eine Matte aus den Ersatzteilen und Zubehör des Tanks auf das Lufteinlassgitter zu legen, wodurch ich Probleme mit dem Staubverschleiß des Motors vermieden habe. Anzumerken ist, dass die staubigen Bedingungen in Deutschland im Sommer am schlimmsten waren. So war zum Beispiel bei den Divisionsübungen im August 1982 bei einem Marsch durch die Waldlichtungen Deutschlands wegen des hängenden Staubes nicht einmal zu sehen, wo der Lauf des Geschützes des eigenen Panzers endete. Der Abstand zwischen den Autos in der Kolonne wurde buchstäblich durch Duft gehalten. Als bis zum vordersten Panzer buchstäblich noch wenige Meter übrig waren, konnte man den Geruch seiner Abgase wahrnehmen und rechtzeitig bremsen. Also 150 Kilometer. Nach dem Marsch hatte alles: Panzer, Menschen und ihre Gesichter, Overalls und Stiefel die gleiche Farbe - die Farbe von Straßenstaub.
Diesel 6TD
Gleichzeitig mit dem Design und der technologischen Weiterentwicklung des 5TDF-Dieselmotors begann das KKBD-Designteam mit der Entwicklung des nächsten Modells eines 2-Takt-Dieselmotors bereits in 6-Zylinder-Bauweise mit einer Leistungssteigerung von bis zu 735 kW (1000 PS). Dieser Motor war, wie auch der 5TDF, ein Dieselmotor mit horizontal angeordneten Zylindern, gegenläufigen Kolben und direkter Anblasung. Der Diesel wurde 6TD genannt.
Die Aufladung erfolgte von einem mechanisch (Feder) mit der Gasturbine verbundenen Verdichter, der einen Teil der Wärmeenergie der Abgase in mechanische Arbeit zum Antrieb des Verdichters umwandelte.
Da die von der Turbine entwickelte Leistung nicht ausreichte, um den Verdichter anzutreiben, wurde dieser über ein Getriebe und einen Getriebemechanismus mit beiden Kurbelwellen des Motors verbunden. Als Verdichtungsverhältnis wurde 15 angenommen.
Um die erforderlichen Ventilsteuerzeiten zu erhalten, bei denen die notwendige Reinigung des Zylinders von Abgasen und die Befüllung mit Druckluft erfolgen würde, wurde eine Winkelverschiebung der Kurbelwellen (wie bei 5TDF-Motoren) in Kombination mit einer asymmetrischen Anordnung der Ansaugung vorgesehen und Auslassöffnungen der Zylinder entlang ihrer Länge. Das den Kurbelwellen entnommene Drehmoment beträgt 30 % für die Einlasswelle und 70 % für das Ablassen des Motordrehmoments. Das an der Einlasswelle entwickelte Drehmoment wurde über das Zahnradgetriebe auf die Auslasswelle übertragen. Das Gesamtdrehmoment könnte von beiden Enden der Auspuffwelle über die Zapfwellenkupplung abgenommen werden.
Im Oktober 1979 bestand der 6TD-Motor nach einer gründlichen Überarbeitung der Zylinder-Kolben-Gruppe, der Kraftstoffausrüstung, des Luftversorgungssystems und anderer Elemente erfolgreich abteilungsübergreifende Tests. Seit 1986 werden die ersten 55er-Motoren gefertigt. In den Folgejahren stieg die Serienproduktion und erreichte 1989 ihren Höhepunkt.
Der Anteil der stückweisen Vereinigung des 6TD mit dem 5TDF-Dieselmotor lag bei über 76 %, die Betriebssicherheit war nicht geringer als die des seit vielen Jahren in Massenproduktion hergestellten 5TDF.
Die Arbeit des KHKBD unter der Leitung des Chefkonstrukteurs N. K. Ryazantsev zur weiteren Verbesserung des 2-Takt-Tankdieselmotors wurde fortgesetzt. Einheiten, Mechanismen und Systeme wurden finalisiert, nach denen einzelne Fehler im Betrieb identifiziert wurden. Das Drucksystem wurde verbessert. Mit der Einführung von Konstruktionsänderungen wurden zahlreiche Prüfstandstests von Motoren durchgeführt.
Eine neue Modifikation des Dieselmotors, 6TD-2, wurde entwickelt. Seine Leistung betrug nicht mehr wie beim 6TD 735 kW (1000 PS), sondern 882 kW (1200 PS). Seine detaillierte Vereinigung mit dem 6TD-Dieselmotor wurde zu mehr als 90% und mit dem 5TDF-Dieselmotor zu mehr als 69% erreicht.
Im Gegensatz zum 6TD-Motor verwendete der 6TD-2-Motor einen 2-stufigen axialen Radialverdichter des Drucksystems und Änderungen in der Konstruktion von Turbine, Faltenbalg, Zentrifugalölfilter, Abzweigrohr und anderen Aggregaten. Das Verdichtungsverhältnis wurde ebenfalls leicht reduziert - von 15 auf 14,5 und der durchschnittliche effektive Druck wurde von 0,98 MPa auf 1,27 MPa erhöht. Der spezifische Kraftstoffverbrauch des 6TD-2-Motors betrug 220 g / (kW * h) (162 g / (PS * h)) statt 215 g / (kW * h) (158 g / (PS * h)) - für 6TD. Aus Sicht des Einbaus in einen Tank war der 6TD-2-Dieselmotor vollständig mit dem 6DT-Motor austauschbar.
1985 bestand Diesel 6TD-2 abteilungsübergreifende Tests und es wurden Konstruktionsunterlagen für die Vorbereitung und Organisation der Serienproduktion vorgelegt.
In KKBD wurden unter Beteiligung von NIID und anderen Organisationen die Forschungs- und Entwicklungsarbeiten am 2-Takt-6TD-Dieselmotor mit dem Ziel fortgesetzt, seine Leistung auf 1103 kW (1500 PS), 1176 kW (1600 PS), 1323 kW (1800 PS) zu steigern. mit Musterprüfungen, sowie die Erstellung einer Motorenfamilie für VGM- und Volkswirtschaftsmaschinen. Für VGM der leichten und mittleren Gewichtsklasse wurden 3TD-Dieselmotoren mit einer Leistung von 184 … 235 kW (250-320 PS), 4TD mit einer Leistung von 294 … 331 kW (400 … 450 PS) entwickelt. Außerdem wurde eine Variante eines 5DN-Dieselmotors mit einer Leistung von 331…367 kW (450-500 PS) für Radfahrzeuge entwickelt. Für Transporter von Traktoren und Technikfahrzeugen wurde ein Projekt für einen 6DN-Dieselmotor mit einer Leistung von 441 … 515 kW (600-700 PS) entwickelt.
Diesel 3TD
ZTD-Motoren in Dreizylinderbauweise sind Mitglieder einer einheitlichen Baureihe mit den Serienmotoren 5TDF, 6TD-1 und 6TD-2E. In den frühen 60er Jahren wurde in Charkow eine Motorenfamilie auf Basis von 5TDF für leichte Fahrzeuge (Panzerwagen, Schützenpanzer usw.) und schwere Kategorie (Panzer, 5TDF, 6TD) geschaffen.
Diese Motoren haben ein einziges Konstruktionsschema:
- Zweitaktzyklus;
- horizontale Anordnung der Zylinder;
- hohe Kompaktheit;
- geringe Wärmeübertragung;
- die Fähigkeit, bei Umgebungstemperaturen zu verwenden
Umgebungen von minus 50 bis plus 55 ° С;
- geringe Leistungsreduzierung bei hohen Temperaturen
Umfeld;
- Multi-Kraftstoff.
Neben objektiven Gründen wurden bei der Schaffung einer Familie von Zweitakt-Boxer-Dieselmotoren 3TD Mitte der 60er Jahre Fehler gemacht. Die Idee eines 3-Zylinder-Motors wurde anhand eines 5-Zylinders getestet, bei dem zwei Zylinder gedämpft wurden. Gleichzeitig waren der Luft-Gas-Weg und die Druckhalteeinheiten nicht aufeinander abgestimmt. Natürlich wurde auch die Kraft der mechanischen Verluste erhöht.
Das Haupthindernis für die Schaffung einer einheitlichen Motorenfamilie in den 60er und 70er Jahren war das Fehlen eines klaren Programms für die Entwicklung des Motorenbaus im Land; die Führung "warf" zwischen verschiedenen Konzepten von Dieselmotoren und Gasturbinenmotoren hin und her. In den 70er Jahren, als Leonid Breschnew an die Führung des Landes kam, verschärfte sich die Situation noch mehr, die parallele Produktion von Panzern mit verschiedenen Motoren - T-72 und T-80, die aufgrund ihrer Eigenschaften "analoge Panzer" der bereits produzierter T-64. Von der Vereinheitlichung der Panzermotoren, Schützenpanzer und Schützenpanzer war keine Rede mehr.
Leider war die gleiche Situation in anderen Zweigen des militärisch-industriellen Komplexes - gleichzeitig wurden verschiedene Konstruktionsbüros in der Raketentechnik und im Flugzeugbau entwickelt, wobei nicht die besten ausgewählt wurden, sondern ähnliche Produkte aus verschiedenen Konstruktionsbüros (Design Bureau) wurden parallel produziert.
Eine solche Politik war der Anfang vom Ende der Binnenwirtschaft, und der Grund für die Verzögerung im Panzerbau, anstatt sich zu einer "einzigen Faust" zusammenzuschließen, wurden die Bemühungen auf die parallele Entwicklung konkurrierender Konstruktionsbüros verstreut.
Light Vehicles (LME), die in den 60er … 80er Jahren des letzten Jahrhunderts hergestellt wurden, verfügen über Motoren veralteter Konstruktion und bieten eine Leistungsdichte im Bereich von 16-20 PS / t. Moderne Maschinen sollten eine spezifische Leistung von 25-28 PS / t haben, was ihre Manövrierfähigkeit erhöht.
In den 90er, 2000er Jahren wurde die Modernisierung der LME relevant - BTR-70, BTR-50, BMP-2.
Während dieser Zeit wurden Tests dieser Maschinen durchgeführt, die die hohen Eigenschaften des neuen Motors zeigten, aber gleichzeitig wurden nach dem Zusammenbruch eine große Anzahl von UTD-20S1-Motoren auf dem Territorium der Ukraine gelagert und produziert der UdSSR.
Generalplaner für Panzerbau der Ukraine M. D. Borisyuk (KMDB) beschloss, die vorhandenen Serienmotoren - SMD-21 UTD-20 und deutsche "Deutz" - zu verwenden, um diese Maschinen zu modernisieren.
Jedes Fahrzeug hatte seine eigenen Motoren, die nicht miteinander vereinheitlicht waren und mit Motoren bereits in der Armee. Denn für die Reparaturwerke des Verteidigungsministeriums lohnt es sich, die in den Lagern des Kunden verfügbaren Motoren zu nutzen, was die Arbeitskosten senkt.
Aber diese Position beraubt die Arbeit des Staatsunternehmens „Werk benannt nach V. A. Malysheva “und vor allem die Zuschlagstoffanlage.
Diese Position erwies sich als zweideutig - einerseits Einsparungen, andererseits Perspektivverlust.
Es ist erwähnenswert, dass in KMDB in Bezug auf 3TD eine Reihe von Ansprüchen (für Lärm und Rauch) erhoben wurden, die akzeptiert und beseitigt wurden.
Um die Rauchentwicklung beim Start und in den Übergangsmodi zu reduzieren, wurde der ZTD-Motor mit einer geschlossenen Kraftstoffanlage ausgestattet und der Ölverbrauch wurde erheblich reduziert. Die Geräuschreduzierung wird durch die Reduzierung des maximalen Verbrennungsdrucks und die Reduzierung des Spiels im Kolben-Zylinder-Paar bei 280- und 400-PS-Motoren sowie die Reduzierung der Drehschwingungsbreite gewährleistet
Die Reduzierung des Ölverbrauchs bei ZTD-Motoren wurde durch folgende Faktoren erreicht:
- Reduzierung der Zylinderzahl;
- die Verwendung eines Kolbens mit einem Gusseisenkörper anstelle einer Aluminiumlegierung;
- Erhöhung des spezifischen Drucks des Ölabstreifrings um
Zylinderwand.
Durch die getroffenen Maßnahmen nähert sich der relative Ölverbrauch der Motoren ZTD dem volkswirtschaftlichen Verbrauch der Motoren an.