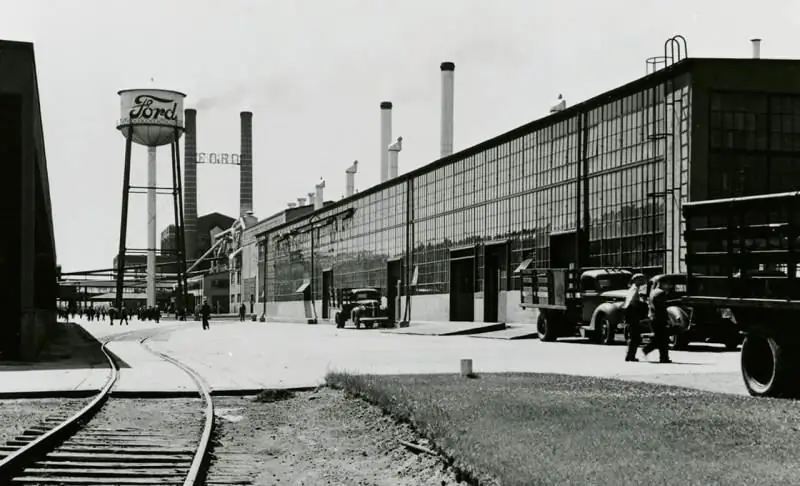
Strategische Technologien
Bevor Sie sich mit den Merkmalen der Panzerproduktion im Michigan Ford-Werk in Detroit (USA) vertraut machen, sollten kurz die Bedingungen erläutert werden, unter denen die Panzerindustrie in der UdSSR aufgebaut wurde. Wie Sie wissen, lernt man alles durch Vergleich.
Die Rüstungsproduktion während des Zweiten Weltkriegs war einer der wichtigsten Faktoren für den strategischen Vorteil. Mit Kriegsbeginn befand sich die Sowjetunion in einer katastrophalen Lage - die gesamte Panzerproduktion konzentrierte sich auf den europäischen Teil des Landes. Der schnelle Vormarsch der deutschen Armee könnte die Produktion von Panzerpanzern im Land vollständig lahmlegen. Nur um den Preis unglaublicher Anstrengungen, einen Teil der Fabriken zu Beginn des Krieges nach Osten zu evakuieren, konnte die Rüstungsproduktion wiederhergestellt werden. Die wichtigsten "Panzerfabriken" waren die Hüttenwerke Kuznetsk, Nischni Tagil und Magnitogorsk.
Aber die Sache beschränkte sich nicht auf eine einfache Verlagerung der Produktion an einen neuen Standort hinter der Front. Die meisten neuen Fabriken waren nicht an das Schmelzen von Panzerpanzern angepasst - vor dem Krieg arbeiteten die Fabriken für den Bedarf des Volkskommissariats für Eisenhüttenkunde. Wartime hat seine eigenen Anpassungen hinzugefügt. Da die Herdöfen jetzt oft mit geringqualifizierten Arbeitern beschäftigt waren, bestand ein akutes Problem des Mangels an speziellen Wärme-, Press- und Metallbearbeitungsgeräten. Daher ging die Verlagerung der Rüstungsproduktion mit einer ernsthaften Umstrukturierung der Technologie selbst zum Schmelzen von Militärstahl einher. Daher war es notwendig, die Produktion an die wichtigsten Offenherdöfen für 120-180 Tonnen anzupassen, ohne den Prozess der Diffusionsdesoxidation. Das Aushärten von Panzerplatten und Panzerteilen musste in Wasser erfolgen.
Eine solche Vereinfachung konnte die Qualität der erhaltenen Rüstung nur beeinträchtigen. Dies gilt insbesondere für den am schwierigsten herstellbaren hochfesten Tankstahl 8C. Die allerersten Proben von Panzerplatten bei Tests zeigten deutliche Schiefer- und Schichtung des Bruchs, eine hohe Neigung zur Rissbildung beim Schweißen und Richten. Darüber hinaus zeigten Feldtests die übermäßige Zerbrechlichkeit der Panzerproben bei Granatenbeschuss.
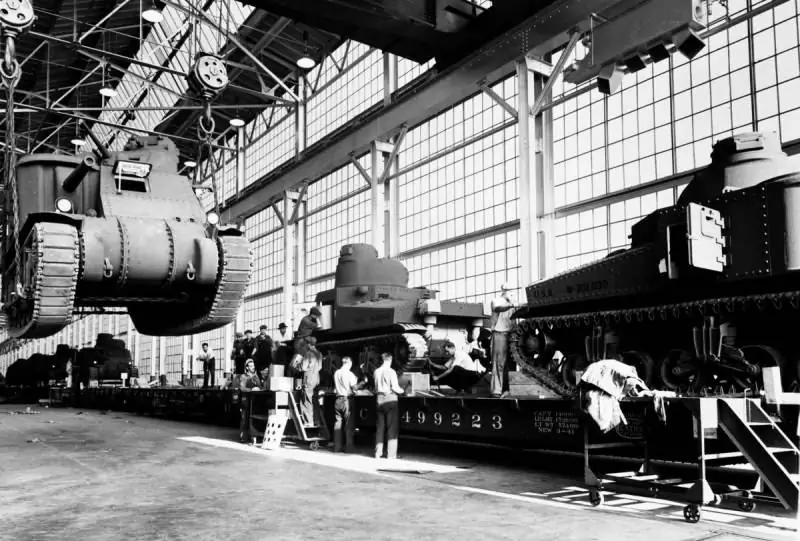
Solche Mängel konnten nicht ignoriert werden. Und im spezialisierten TsNII-48 haben sie eine Reihe von Verbesserungen entwickelt. Zunächst sollte Panzerstahl von nun an nur noch in vorgeheizten Öfen nach dem Schmelzen von "zivilen" Stahlsorten geschmolzen werden. Der Stahl musste mindestens anderthalb Stunden im offenen Schmelzbad kochen und in quadratische oder konvexe Formen gegossen werden. Darüber hinaus achteten Metallurgen besonders auf den Schwefelgehalt im ursprünglichen Roheisen (maximal 0,06 %) sowie auf Kohlenstoff und Mangan. In Kombination mit anderen Maßnahmen konnte dadurch die Qualität der Panzerung verbessert werden. Insbesondere um den Schiefer und die Schichtung der Fraktur zu reduzieren.
Ein wichtiges Problem war die Technologie der Wärmebehandlung von Haushaltsrüstungen. Einfach ausgedrückt kostete das Härten und Anlassen der Panzerplatten zu viel Zeit und Energie und es fehlte an der notwendigen Ausrüstung. Es war notwendig, den Prozess zu vereinfachen. Dazu geben wir ein typisches Beispiel.1942 gelang es den Metallurgen von TsNII-48, den Prozess der thermischen Vorbereitung so weit zu vereinfachen, dass sie nur für Teile des Bodens von KV- und T-34-Tanks etwa 3230 Ofenstunden pro 100 Rümpfe sparten.
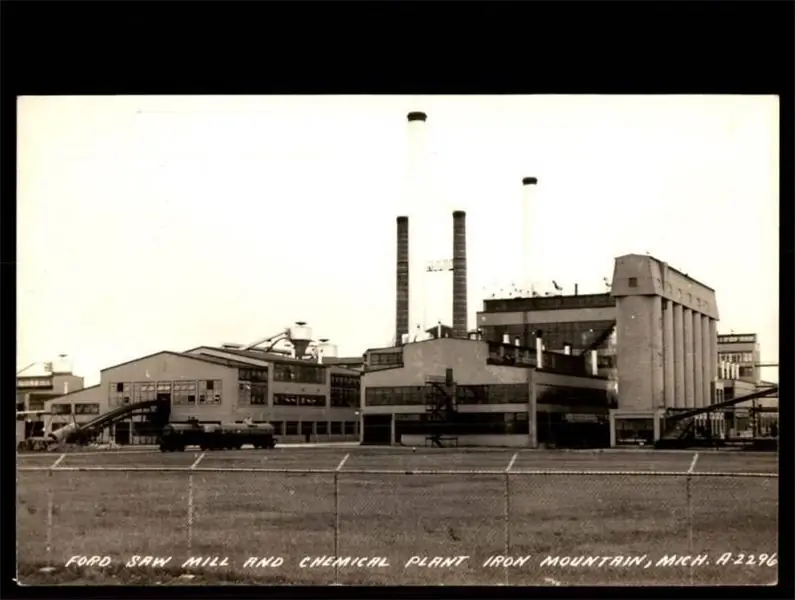
Dennoch waren bis zum Ende des Krieges in der Sowjetunion die Voraussetzungen für die Produktion strategisch wichtiger Panzerpanzer alles andere als erforderlich. Das gleiche gilt nicht für die Militärindustrie des ausländischen Partners, dessen Territorium vom Weltkrieg nicht betroffen war. Dafür mussten sich die sowjetischen Hütteningenieure am 26. Februar 1945, 72 Tage vor dem Sieg, erneut vergewissern.
Amerikanischer Luxus
Die wenig bekannte Geschichte des Besuchs der sowjetischen Delegation in der Ford-Panzerfabrik in Detroit wurde von Wassili Wladimirowitsch Sapariy, Kandidat für Geschichtswissenschaften des Instituts für Geschichte und Archäologie der Uraler Zweigstelle der Russischen Akademie der Wissenschaften, bekannt gegeben. Das Material des Wissenschaftlers basiert auf dem Bericht sowjetischer Metallurgen über die Ergebnisse einer Reise in die Vereinigten Staaten, der im Russischen Staatsarchiv für Wirtschaft (RGAE) aufbewahrt wird. Es sei darauf hingewiesen, dass die RGAE nur eine Fundgrube von Archivdokumenten aus der Zeit des Großen Vaterländischen Krieges im Zusammenhang mit der Herstellung von militärischer Ausrüstung und Ausrüstung ist. Es bleibt nur zu erraten, wie viele Geheimnisse das Archiv noch in den bisher klassifizierten Beweisen birgt.
Nach Angaben von Ingenieuren, die aus Detroit zurückgekehrt waren, handelte es sich bei der Panzerwerkstatt des Ford-Werks um ein Gebäude mit zwei Spannweiten von 273 Metern Länge, 30 Metern Breite und etwa 10 Metern Höhe. Gleichzeitig roch der Laden keine Rüstung. Es war hauptsächlich für die Wärmebehandlung und das Schneiden von Stahl bestimmt. Dies weckte natürlich bei den sowjetischen Metallurgen angesichts der oben beschriebenen Probleme der heimischen Panzerproduktion besonderes Interesse. Das Hauptproduktionsprofil der Werkstatt von Ford Motors war die Arbeit mit Panzerungen bis zu einer Dicke von 76 mm. In anderen Werken in Detroit wurden wärmebehandelte Stahlbleche verwendet, um die Rümpfe von leichten und mittelschweren Panzerfahrzeugen zu schweißen.
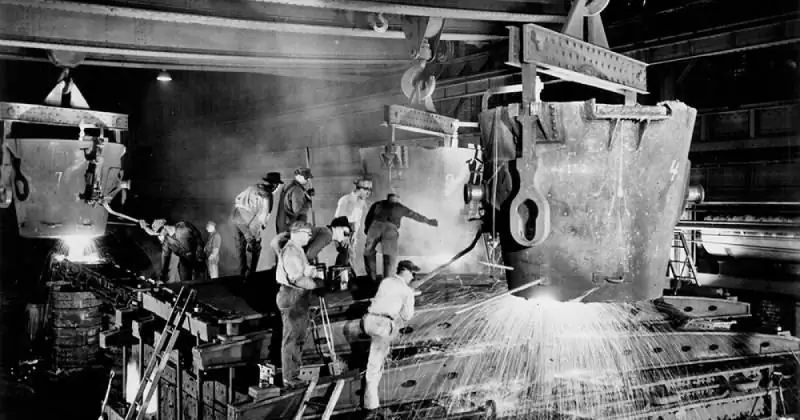
Zunächst beeindruckte die Mechanisierung des Produktionsprozesses die Ford-Werkstätten. Nach dem Schmelzen und Walzen wurden die Panzerplatten auf hydraulischen Tischladern von United an die Wärmebehandlungshalle geliefert. Die Lader wiederum nahmen die Panzerung von den Bahnsteigen in der Nähe der Werkstatt. In der Werkstatt selbst gab es zwei Brückenkräne, die dazu bestimmt waren, Panzerplatten bei allen technologischen Vorgängen mit Ausnahme der Härteprozesse zu bewegen.
Um die notwendige kristalline Struktur der Panzerung zu erzeugen, wurden zwei Pressen mit einem Kraftaufwand von jeweils 2500 Tonnen, fünf 70-Meter-Förderöfen und fünf 100-Meter-Gastemperier-Förderöfen eingesetzt. Wasser wurde den Panzerhärtepressen durch den Betrieb von sechs Pumpen gleichzeitig zugeführt, die über 3700 Liter pro Minute pumpten. Wie russische Ingenieure schrieben, waren die Komplexität und die Kosten der Konstruktion solcher Pressen, die gleichzeitig glühende Panzerung stanzen und kühlen können, unerschwinglich. Gleichzeitig bestanden Zweifel an der Zweckmäßigkeit der Verwendung von Pressen für Rüstungen mit einer Dicke von 30-76 mm. Hier stand die Intensität der Wasserversorgung zur Kühlung im Vordergrund.
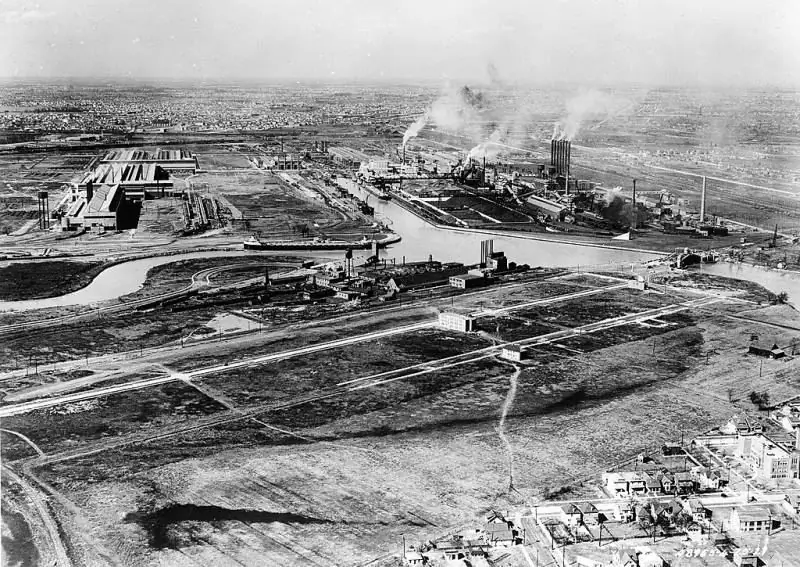
Die 2.500-Tonnen-Pressen waren nicht die einzigen im Ford-Panzerfahrzeug. Toledo-Pressen # 206 waren mit dem Schneiden dünner Panzerungen beschäftigt und entwickelten einen Druck von 161 Tonnen. Für Rüstungen mit einer Dicke von mehr als 2,5 cm wurde ausschließlich Feuerschneiden verwendet.
Bei einem Besuch im Unternehmen konnten Metallurgen den Prozess des Härtens dünner kugelsicherer Panzerung mitverfolgen. Es blieb 15 Sekunden lang unter einer Presse von 1000 Tonnen, dann wurde das Blech 2,5 Stunden lang zum Abschrecken bei 900 Grad Celsius und für vier Stunden Urlaub bei 593 Grad Celsius geschickt.
All dieser technische Reichtum wurde von sowjetischen Ingenieuren beobachtet, abgesehen von verschiedenen "kleinen Zubehörteilen": Schweißmaschinen, Fräsmaschinen, Scheren und dergleichen.
Das Hauptmerkmal der Wärmebehandlung der Panzerung war der kontinuierliche Produktionsfluss. In fast allen Verarbeitungsstufen waren Stahlbleche auf Rollen- und Kettenförderern unterwegs. Das Förderband wurde von einer zentralen Konsole aus gesteuert. In einem der letzten Schritte wurden alle Panzerplatten auf den Grad der Brinell-Härte untersucht. In diesem Fall sollte die Schwankung des Prüfparameters von Blatt zu Blatt minimal sein - nicht mehr als 0,2 mm.
Von besonderem Interesse für die sowjetische Delegation waren zwei Strahlanlagen, die fast nach jeder technologischen Operation die Panzerplatten reinigten. Solch ein Perfektionismus und solch ein Luxus konnten sich nur Amerikaner leisten, weit weg von den Härten des Krieges.