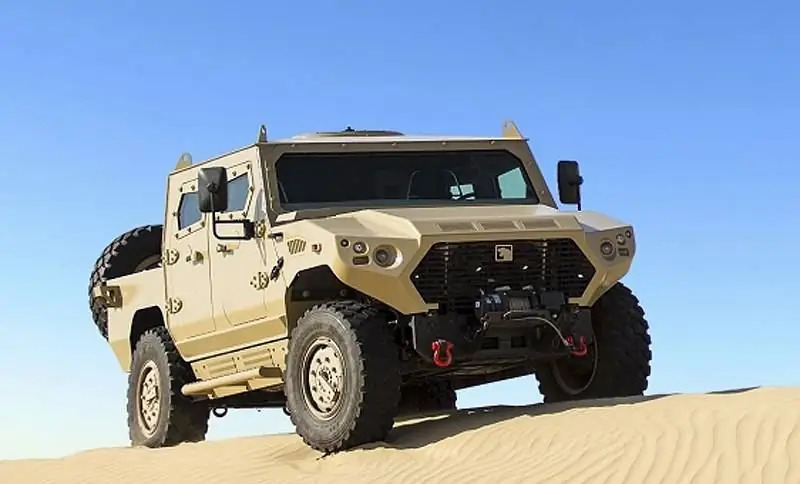
Rüstungen sind Millionen Jahre älter als die Menschheit und wurden hauptsächlich zum Schutz vor Kiefern und Klauen entwickelt. Es ist möglich, dass Krokodile und Schildkröten den Menschen teilweise dazu inspirieren könnten, schützende Elemente zu schaffen. Alle Waffen mit kinetischer Energie, sei es eine prähistorische Keule oder ein panzerbrechendes Projektil, sind darauf ausgelegt, große Kraft auf kleinem Raum zu konzentrieren, ihre Aufgabe besteht darin, das Ziel zu durchdringen und ihm maximalen Schaden zuzufügen. Aufgabe der Panzerung ist es folglich, dies zu verhindern, indem sie die Angriffsmittel ablenkt oder zerstört und/oder die Aufprallenergie möglichst großflächig verteilt, um Schäden an Arbeitskräften, Transportsystemen und Strukturen, die sie schützt, zu minimieren.
Moderne Panzerung besteht typischerweise aus einer harten Außenschicht, um das Projektil zu stoppen, abzulenken oder zu zerstören, einer Zwischenschicht mit einer sehr hohen „Brucharbeit“und einer viskosen Innenschicht, die Risse und Ablagerungen verhindert.
Stahl
Stahl, der das erste weit verbreitete Material bei der Herstellung von gepanzerten Fahrzeugen wurde, ist trotz des Aufkommens von Panzerungen auf der Grundlage von Leichtmetalllegierungen aus Aluminium und Titan, Keramik, Verbundwerkstoffen mit Polymermatrix, verstärkt mit Glasfasern, Aramid. immer noch gefragt und Polyethylen mit ultrahohem Molekulargewicht sowie Verbundmaterialien mit einer Metallmatrix.
Viele Stahlwerke, darunter auch SSAB, entwickeln weiterhin hochfeste Stähle für eine Vielzahl gewichtskritischer Anwendungen wie zum Beispiel zusätzliche Ummantelungen. Die Panzerstahlsorte ARM OX 600T, erhältlich in Dicken von 4-20 mm, ist mit einer garantierten Härte von 570 bis 640 HBW-Einheiten (Abkürzung für Härte, Brinell, Wolfram; ein Test, bei dem eine Wolframkugel mit Standarddurchmesser gepresst wird) erhältlich in eine Materialprobe mit bekannter Kraft, dann wird der Durchmesser der geformten Vertiefung gemessen; dann werden diese Parameter in die Formel eingesetzt, die es Ihnen ermöglicht, die Anzahl der Härteeinheiten zu erhalten).
SSAB betont auch, wie wichtig es ist, das richtige Gleichgewicht zwischen Härte und Zähigkeit für Penetrations- und Berstschutz zu erreichen. Wie alle Stähle besteht ARMOX 600T aus Eisen, Kohlenstoff und einer Reihe anderer Legierungsbestandteile wie Silizium, Mangan, Phosphor, Schwefel, Chrom, Nickel, Molybdän und Bor.
Es gibt Einschränkungen bei den verwendeten Herstellungstechniken, insbesondere wenn es um die Temperatur geht. Dieser Stahl ist nicht für eine zusätzliche Wärmebehandlung vorgesehen; wenn er nach der Lieferung auf über 170 ° C erhitzt wird, kann SSAB seine Eigenschaften nicht garantieren. Unternehmen, die diese Art von Einschränkung umgehen können, werden wahrscheinlich die genaue Prüfung der Hersteller von gepanzerten Fahrzeugen auf sich ziehen.
Ein weiteres schwedisches Unternehmen, Deform, bietet Herstellern von gepanzerten Fahrzeugen, insbesondere solchen, die den Schutz von Nutzfahrzeugen und Zivilfahrzeugen verbessern möchten, warmumgeformte Teile aus durchschusshemmendem Panzerstahl.
Im Nissan PATROL 4x4, dem Volkswagen T6 TRANSPORTER Minibus und dem Isuzu D-MAX Pickup sind einteilige Deform-Firewalls sowie eine solide Bodenplatte aus dem gleichen Material verbaut. Das von Deform entwickelte und in der Blechfertigung eingesetzte Warmumformverfahren hält eine Härte von 600HB [HBW].
Das Unternehmen behauptet, die Eigenschaften aller auf dem Markt befindlichen Panzerstähle unter Beibehaltung einer strukturell definierten Form wiederherstellen zu können, während die resultierenden Teile traditionellen geschweißten und teilweise überlappenden Strukturen weit überlegen sind. Bei dem von Deform entwickelten Verfahren werden die Bleche nach dem Warmschmieden vergütet. Dank dieses Verfahrens ist es möglich, dreidimensionale Formen zu erhalten, die durch Kaltumformung ohne die in solchen Fällen obligatorischen "Schweißnähte, die die Integrität der kritischen Punkte verletzen" nicht erhalten werden können.
Auf den BAE Systems BVS-10 und CV90 sowie seit Anfang der 90er Jahre auf vielen Maschinen von Kraus-Maffei Wegmann (KMW) kommen verformte warmumgeformte Stahlbleche zum Einsatz. Aufträge zur Herstellung von dreidimensionalen Panzerplatten für den Panzer LEOPARD 2 und mehreren Formplatten für die BOXER- und PUMA-Fahrzeuge sowie für mehrere Rheinmetall-Fahrzeuge, darunter wieder den BOXER, sowie eine Luke für das WIESEL-Fahrzeug kommen. Deform funktioniert auch mit anderen Schutzmaterialien wie Aluminium, Kevlar / Aramid und Titan.
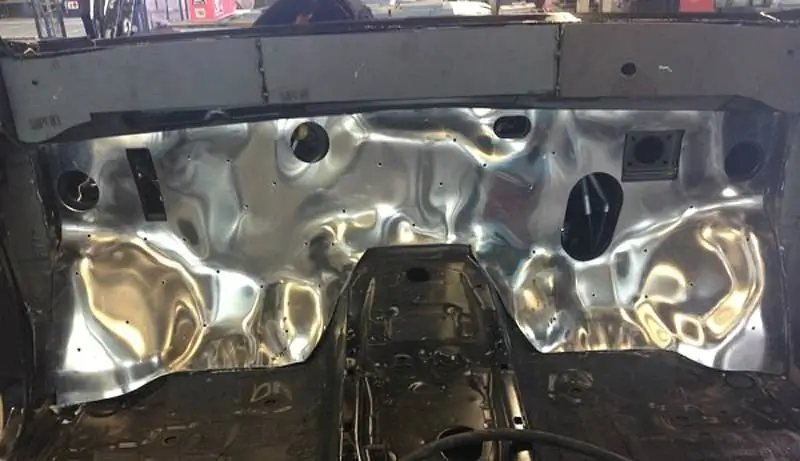
Aluminium-Fortschritt
Bei gepanzerten Fahrzeugen wurde zum ersten Mal eine Aluminiumpanzerung bei der Herstellung des seit 1960 hergestellten Schützenpanzers M113 weit verbreitet. Es war eine Legierung mit der Bezeichnung 5083, die 4,5% Magnesium und viel kleinere Mengen Mangan, Eisen, Kupfer, Kohlenstoff, Zink, Chrom, Titan und andere enthielt. Obwohl 5083 seine Festigkeit nach dem Schweißen gut behält, ist es keine wärmebehandelbare Legierung. Es hat keine so gute Beständigkeit gegen 7,62-mm-Panzerungsgeschosse, aber, wie offizielle Tests bestätigten, stoppt es 14,5-mm-Panzerungsgeschosse im sowjetischen Stil besser als Stahl, während es gleichzeitig Gewicht spart und die gewünschte Stärke hinzufügt. Für dieses Schutzniveau ist das Aluminiumblech dicker und 9-mal stärker als Stahl mit einer geringeren Dichte von 265 r / cm3, was zu einer Reduzierung des Gewichts der Struktur führt.
Die Hersteller von gepanzerten Fahrzeugen begannen bald, leichtere, ballistisch stärkere, schweißbare und wärmebehandelbare Aluminiumpanzerungen zu verlangen, was zu Alcans Entwicklung von 7039 und später 7017 führte, beide mit höherem Zinkgehalt.
Wie bei Stahl kann auch das Stanzen und die anschließende Montage die Schutzeigenschaften von Aluminium negativ beeinflussen. Beim Schweißen erweichen die Wärmeeinflusszonen, ihre Festigkeit wird jedoch durch die Aushärtung während der natürlichen Alterung teilweise wiederhergestellt. In engen Zonen in der Nähe der Schweißnaht verändert sich das Gefüge des Metalls, wodurch bei Schweiß- und/oder Montagefehlern große Eigenspannungen entstehen. Folglich sollten sie durch Fertigungstechniken minimiert werden, während auch das Risiko von Spannungsrisskorrosion minimiert werden sollte, insbesondere wenn die Lebensdauer der Maschine voraussichtlich mehr als drei Jahrzehnte betragen wird.
Spannungsrisskorrosion ist ein Prozess des Auftretens und des Wachstums von Rissen in einer korrosiven Umgebung, der sich mit zunehmender Anzahl von Legierungselementen verschlechtert. Die Rissbildung und deren nachfolgendes Wachstum erfolgt durch Diffusion von Wasserstoff entlang der Korngrenzen.
Die Bestimmung der Rissanfälligkeit beginnt mit der Entnahme einer geringen Menge Elektrolyt aus den Rissen und deren Analyse. Spannungskorrosionstests mit niedriger Dehnungsrate werden durchgeführt, um festzustellen, wie stark eine bestimmte Legierung beschädigt wurde. Das mechanische Dehnen von zwei Proben (eine in einer korrosiven Umgebung und die andere in trockener Luft) erfolgt, bis sie versagen, und dann wird die plastische Verformung an der Bruchstelle verglichen - je mehr die Probe bis zum Versagen gedehnt wird, desto besser.
Die Beständigkeit gegen Spannungsrisskorrosion kann während der Verarbeitung verbessert werden. Laut Total Materia, das sich selbst als „die weltweit größte Materialdatenbank“bezeichnet, hat Alcan beispielsweise die Leistung des 7017 bei beschleunigten Spannungsrisskorrosionsprüfungen um das 40-fache verbessert. Die erzielten Ergebnisse ermöglichen auch die Entwicklung von Korrosionsschutzmethoden für Zonen von Schweißkonstruktionen, in denen Eigenspannungen nur schwer zu vermeiden sind. Die Forschung zur Verbesserung von Legierungen zur Optimierung der elektrochemischen Eigenschaften von Schweißverbindungen ist im Gange. Die Arbeiten an neuen wärmebehandelbaren Legierungen konzentrieren sich auf die Verbesserung ihrer Festigkeit und Korrosionsbeständigkeit, während die Arbeiten an nicht wärmebehandelbaren Legierungen darauf abzielen, die durch Schweißbarkeitsanforderungen auferlegten Einschränkungen zu beseitigen. Die härtesten Materialien in der Entwicklung werden 50 % stärker sein als die besten heute verwendeten Aluminiumpanzerungen.
Legierungen mit niedriger Dichte wie Lithium-Aluminium bieten gegenüber früheren Legierungen mit vergleichbarer Durchschussfestigkeit etwa 10 % Gewichtseinsparungen, obwohl die ballistische Leistung gemäß Total Materia noch nicht vollständig bewertet werden muss.
Auch Schweißverfahren, einschließlich Roboter, werden verbessert. Zu den gelösten Aufgaben gehören die Minimierung der Wärmezufuhr, ein stabilerer Schweißlichtbogen durch die Verbesserung der Energie- und Drahtversorgungssysteme sowie die Überwachung und Steuerung des Prozesses durch Expertensysteme.
MTL Advanced Materials hat mit ALCOA Defence, einem renommierten Hersteller von Aluminiumpanzerplatten, zusammengearbeitet, um einen "zuverlässigen und wiederholbaren Kaltumformprozess" zu entwickeln, den das Unternehmen beschreibt. Das Unternehmen stellt fest, dass die für Panzerungsanwendungen entwickelten Aluminiumlegierungen nicht für die Kaltumformung entwickelt wurden, was bedeutet, dass sein neues Verfahren dazu beitragen sollte, häufige Fehlerarten, einschließlich Rissbildung, zu vermeiden. Das ultimative Ziel ist es, den Maschinenbauern zu ermöglichen, den Schweißbedarf zu minimieren und die Anzahl der Teile zu reduzieren, so das Unternehmen. Die Reduzierung des Schweißvolumens, betont das Unternehmen, erhöht die strukturelle Festigkeit und den Schutz der Besatzung und senkt gleichzeitig die Produktionskosten. Ausgehend von der bewährten Legierung 5083-H131 entwickelte das Unternehmen ein Verfahren zur Kaltumformung von Teilen mit einem 90-Grad-Biegewinkel entlang und quer zu den Körnern und ging dann zu komplexeren Materialien über, beispielsweise den Legierungen 7017, 7020 und 7085, auch gute Ergebnisse erzielen.
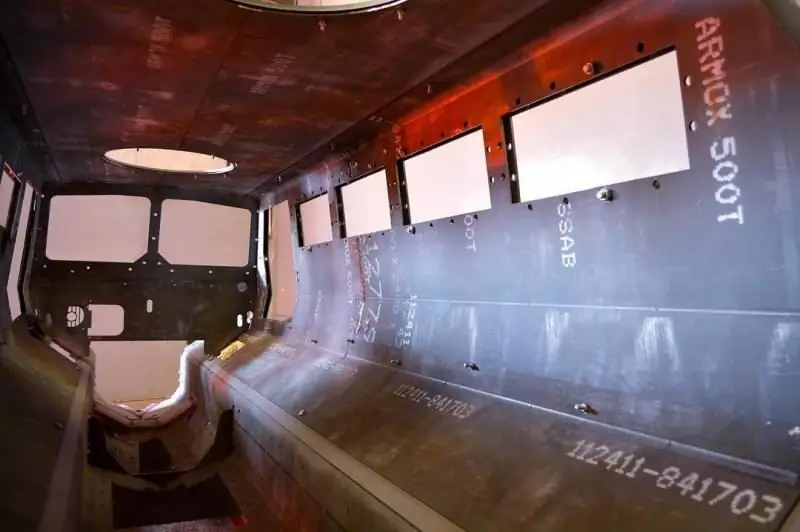
Keramik und Verbundwerkstoffe
Vor einigen Jahren kündigte Morgan Advanced Materials die Entwicklung mehrerer SAMAS-Panzersysteme an, die aus einer Kombination aus fortschrittlicher Keramik und strukturellen Verbundwerkstoffen bestanden. Die Produktlinie umfasst klappbare Panzerung, Splitterschutzauskleidungen, Überlebensfähigkeitskapseln aus Strukturverbundwerkstoffen zum Ersetzen von Metallrümpfen und zum Schutz von bewohnten und unbewohnten Waffenmodulen. Alle können an spezifische Anforderungen angepasst oder auf Bestellung gefertigt werden.
Bietet STANAG 4569 Level 2-6-Schutz, zusammen mit Multi-Impact-Leistung und Gewichtseinsparungen (das Unternehmen behauptet, dass diese Systeme halb so viel wiegen wie ähnliche Stahlprodukte) und passt sich an spezifische Bedrohungen, Plattformen und Missionen an. … Splitterschutzauskleidungen können aus flachen Paneelen mit einem Gewicht von 12,3 kg für eine Fläche von 0,36 m2 (ca. 34 kg / m2) oder aus massiven Beschlägen mit einem Gewicht von 12,8 kg für 0,55 m2 (ca. 23,2 kg / m2) hergestellt werden.
Laut Morgan Advanced Materials bietet eine zusätzliche Panzerung, die für neue und die Modernisierung bestehender Plattformen entwickelt wurde, die gleichen Fähigkeiten bei halbem Gewicht. Das patentierte System bietet maximalen Schutz gegen eine Vielzahl von Bedrohungen, darunter Klein- und Mittelkaliberwaffen, improvisierte Sprengkörper (IEDs) und raketengetriebene Granaten, sowie Multi-Impact-Performance.
Für Waffenmodule (neben Luft- und Seeanwendungen) wird ein "semi-strukturelles" Panzerungssystem mit guter Korrosionsbeständigkeit angeboten, das neben der Gewichtseinsparung und der Minimierung von Schwerpunktproblemen im Gegensatz zu Stahl weniger Probleme mit der elektromagnetischen Verträglichkeit verursacht.
Der Schutz von Waffenmodulen ist ein besonderes Problem, da sie ein attraktives Ziel darstellen, da ihre Deaktivierung die Situationsbeherrschung der Besatzung und die Fähigkeit des Fahrzeugs, mit Bedrohungen in der Nähe umzugehen, drastisch beeinträchtigt. Sie haben auch empfindliche Optoelektronik und anfällige Elektromotoren. Da sie meist oben am Fahrzeug verbaut werden, sollte die Panzerung leicht sein, um den Schwerpunkt möglichst tief zu halten.
Das Schutzsystem der Waffenmodule, das Panzerglas und Schutz des oberen Teils umfassen kann, ist vollständig zusammenklappbar, zwei Personen können es in 90 Sekunden wieder zusammenbauen. Zusammengesetzte Überlebensfähigkeitskapseln werden aus dem hergestellt, was das Unternehmen als „einzigartige robuste Materialien und Polymerformulierungen“bezeichnet, sie bieten Splitterschutz und können vor Ort repariert werden.
Soldatenschutz
Das von 3M Ceradyne entwickelte SPS (Soldier Protection System) umfasst Helme und Einsätze in Körperpanzerungen für das Integrated Head Protection System (IHPS) und VTP (Vital Torso Protection) - ESAPI (Enhanced Small Arms Protective Insert) Komponenten - verbesserter Einsatz zum Schutz gegen Kleinwaffen) des SPS-Systems.
Zu den IHPS-Anforderungen gehören ein geringeres Gewicht, ein passiver Gehörschutz und ein verbesserter Schutz vor stumpfem Aufprall. Das System umfasst auch Zubehör wie eine Komponente zum Schutz des Unterkiefers eines Soldaten, ein Schutzvisier, eine Halterung für Nachtsichtbrillen, Führungen für beispielsweise Taschenlampe und Kamera sowie einen zusätzlichen modularen Kugelschutz. Der Vertrag im Wert von mehr als 7 Millionen US-Dollar sieht die Lieferung von rund 5.300 Helmen vor. Inzwischen werden im Rahmen des 36-Millionen-Dollar-Vertrags mehr als 30.000 ESAPI-Kits - leichtere Einsätze für Körperpanzer - geliefert. Die Produktion dieser beiden Kits begann im Jahr 2017.
Ebenfalls im Rahmen des SPS-Programms wählte KDH Defence die Materialien SPECTRA SHIELD und GOLD SHIELD von Honeywell für fünf Subsysteme aus, darunter das Subsystem Torso and Extremity Protection (TEP), das für das SPS-Projekt geliefert werden soll. Das TEP-Schutzsystem ist 26% leichter, was letztendlich das Gewicht des SPS-Systems um 10% reduziert. KDH wird SPECTRA SHIELD, das auf UHMWPE-Fasern basiert, und GOLD SHIELD, basierend auf Aramidfasern, in seinen eigenen Produkten für dieses System verwenden.
SPECTRA-Faser
Honeywell verwendet ein proprietäres Polymerfaser-Spinn- und -Streckverfahren, um UHMWPE-Rohmaterial in SPECTRA-Fasern einzubetten. Dieses Material ist in Bezug auf das Gewicht 10 Mal stärker als Stahl, seine spezifische Festigkeit ist 40% höher als die von Aramidfasern, es hat einen höheren Schmelzpunkt als Standard-Polyethylen (150° C) und eine höhere Verschleißfestigkeit im Vergleich zu anderen Polymeren, z Beispiel Polyester.
Das starke und steife SPECTRA-Material zeigt beim Bruch eine hohe Verformung, dh es dehnt sich vor dem Bruch sehr stark; Diese Eigenschaft ermöglicht es, eine große Menge an Aufprallenergie zu absorbieren. Honeywell behauptet, dass SPECTRA-Faserverbundwerkstoffe bei Stößen mit hoher Geschwindigkeit wie Gewehrkugeln und Stoßwellen sehr gut funktionieren. „Unsere fortschrittliche Faser reagiert auf Stöße, indem sie kinetische Energie schnell aus der Aufprallzone entfernt …, Wasser und UV-Licht."
Bei seiner SHIELD-Technologie breitet Honeywell parallele Faserstränge aus und verbindet sie durch Imprägnieren mit einem fortschrittlichen Harz, um ein unidirektionales Band zu erzeugen. Anschließend werden die Lagen dieses Bandes über Kreuz in den gewünschten Winkeln gelegt und bei vorgegebener Temperatur und Druck zu einem Verbund verlötet. Für weiche tragbare Anwendungen wird es zwischen zwei Schichten dünner und flexibler transparenter Folie laminiert. Da die Fasern gerade und parallel bleiben, leiten sie Aufprallenergie effizienter ab, als wenn sie zu einem Gewebe verwoben wären.
Short Bark Industries verwendet SPECTRA SHIELD auch im BCS (Ballistic Combat Shirt) Bodyguard für das SPS TEP System. Short Bark ist auf weichen Schutz, taktische Bekleidung und Accessoires spezialisiert.
Laut Honeywell wählten Soldaten aus diesen Materialien hergestellte Schutzelemente, nachdem sie eine überlegene Leistung gegenüber ihren Gegenstücken aus Aramidfasern gezeigt hatten.