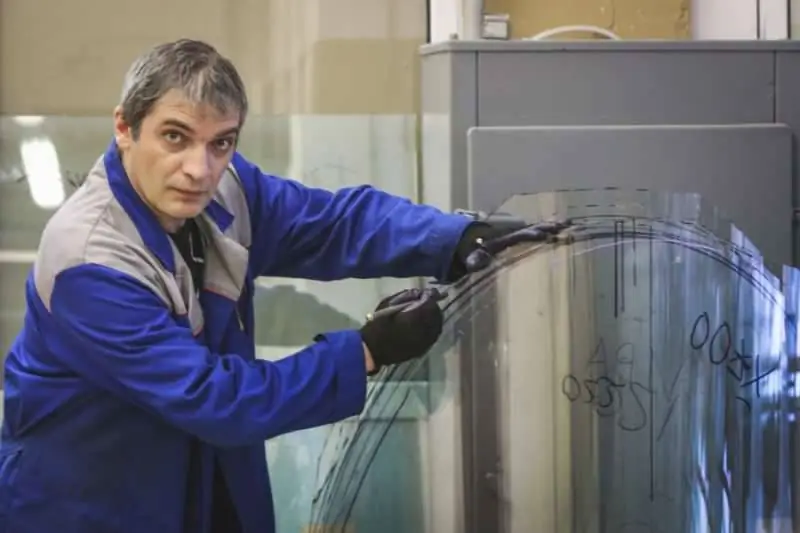
In Russland wurden neue Technologien zur Herstellung von Verglasungen der Kabinen von Militär- und Zivilflugzeugen aus Silikatglas entwickelt. Solche Produkte erweisen sich als leichter und fester, als wenn sie aus zuvor verwendeten organischen Materialien hergestellt wurden. Silikatglas wird auch in anderen Bereichen eingesetzt, von der Weltraumforschung bis zum Wohnungsbau.
Seit einigen Jahren wird unter Weltraumforschern über die Sicherheitsbewertung und den Betrieb der Internationalen Raumstation ISS diskutiert. Tatsache ist, dass im russischen Segment der ISS 13 Fenster installiert sind. Bei gemeinsamen Diskussionen auf der ISS wird vorgeschlagen, die Fenster im russischen Segment wegen der Gefahr von Glasdefekten durch Mikrometeoriteneinschläge mit Blindstopfen zu verschließen - die Sicherheit der Station könnte sich verbessern, heißt es. Aber der Vertreter der russischen Seite - der Direktor des Wissenschaftlichen Forschungsinstituts für Technisches Glas (NITS), Verdienter Wissenschaftler, Vizepräsident der Akademie der Ingenieurwissenschaften der Russischen Föderation, Doktor der Technischen Wissenschaften, Professor Wladimir Solinow - steht auf seinem Standpunkt - über viele Jahre blieb die Restfestigkeit nach dem Einschlag von Weltraummikropartikeln erhalten und verschiedene Strahlungen und andere Bedrohungen aus dem Weltraum haben die Sicherheit der am Institut erstellten Fenster sowie der Besatzung nicht beeinträchtigt, daher gibt es keinen Grund zur Einschränkung die Beobachtung unseres Planeten, "verdunkelt" die Arbeit der Kosmonauten in den russischen Modulen der Orbitalstation.
Bullaugen für die Orbitalstation sind nur eines der wenigen Produkte von NITS. Der Hauptteil der Arbeit von Wissenschaftlern und Technologen des im Südwesten von Moskau gelegenen Instituts ist natürlich mit der Schaffung von Strukturoptiken, Verglasungen oder, wie sie hier sagen, "komplexen transparenten optischen Systemen" für Kampfflugzeuge verbunden der vierten und fünften Generation, die von den UAC-Werken produziert werden. Und jedes Jahr gibt es viel mehr Arbeit für die Luftfahrt.
Silikat oder organisch
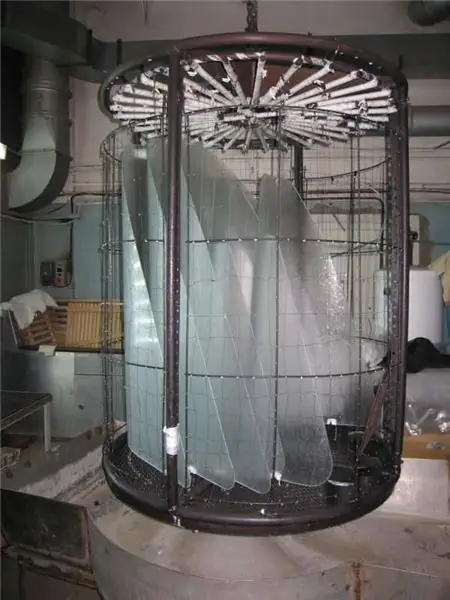
Auf dem Foto: T-50 Windschutzscheibenrohlinge in einer Härtekassette.
Silikatglas ist ein Material mit einzigartigen Eigenschaften. Seine Transparenz, hohe Optik, Hitzebeständigkeit, Festigkeit und die Möglichkeit, verschiedene Beschichtungen zu verwenden, machen es für die Flugzeugverglasung unverzichtbar. Aber warum wurde bei der Verglasung von Flugzeugkabinen im Ausland und in unserem Land organischen Stoffen der Vorrang gegeben? Nur aus einem Grund - es ist einfacher. Sie sagen auch, dass Silikatglas zu zerbrechlich ist.
In den letzten Jahren haben die Entwicklungen der NITS-Materialwissenschaftler es ermöglicht, das Konzept von Silikatglas als sprödem Material radikal zu verändern. Moderne Verstärkungsmethoden ermöglichen es, Verglasungen für moderne Kampfflugzeuge eine ausreichende Festigkeit zu verleihen, um dem Aufprall eines etwa zwei Kilogramm schweren Vogels bei einer Geschwindigkeit von 900 km / h standzuhalten.
„Heute hat sich die Methode der Aushärtung in der Randschicht erschöpft. Es ist an der Zeit, die innere Struktur des Glases, seine Fehlerhaftigkeit, zu ändern “, sagt Vladimir Solinov. So seltsam es klingen mag, dies wird durch die vom Westen verhängten Sanktionen erleichtert. Tatsache ist, dass ausländische Firmen auch in der Zeit vor der Sanktion nach NATO-Beschluss keine Silikatgläser mit verbesserter Qualität nach Russland lieferten, die dort für spezielle Zwecke verwendet wurden. Dies zwang NITS dazu, Architekturglas zu verwenden. Obwohl russische Hersteller Millionen von Quadratmetern dieses Glases produzieren, ist seine Qualität nicht für den Einsatz in der Luftfahrt geeignet.
Abhilfe schaffte die Importsubstitution: In Moskau wurde ein für die Glasindustrie grundlegend neues Projekt für Forschung und Entwicklung sowie Konstruktion von Anlagen ins Leben gerufen.
Alle Glassyntheseverfahren mit russischer Priorität werden darauf getestet.
Das Projekt wurde der jungen Wissenschaftlerin Tatiana Kiseleva anvertraut. 26-jähriger Absolvent der Russischen Universität für Chemische Technologie. D. I. Mendeleeva leitet das Labor, 2015 verteidigte sie ihre Dissertation. In der Glasabteilung in Mendeleevka studierte Tatiana die Eigenschaften transparenter Rüstungen. Eine ihrer beruflichen Herausforderungen besteht darin, ein Glas zu entwickeln, das in seinen Eigenschaften einem der besten Analoga der Welt überlegen ist - Herkulitglas, das Russland noch nicht produziert hat.
Das Projekt basiert auf einem neuen ursprünglichen Verfahren des Glasschmelzens. Bereits heute hat das Labor Glasproben erhalten, deren strukturelle Festigkeit dreimal höher ist als die der nach der traditionellen Methode erhaltenen Analoga. Wenn man die bestehenden Härtungsmethoden hinzufügt, erhält man Glas, dessen Festigkeit um ein Vielfaches höher ist als bei vielen Arten von legiertem Stahl. Dauerhafteres Glas macht leichtere Produkte. Anzumerken ist jedoch, dass die Entwickler von organischem Glas die technische Leistungsfähigkeit ihrer Produkte ständig verbessern, der Streit um das bessere Glas ist noch nicht beendet.
Laterne für T-50
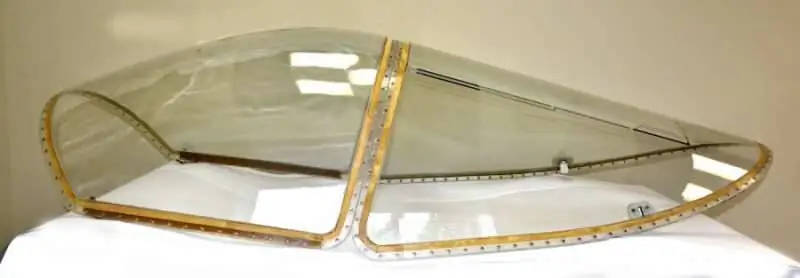
Auf dem Foto: ein Verglasungssatz für ein T-50-Flugzeug - ein Frontvisier und ein Klappteil.
Stellen Sie sich ein Paket aus mehreren Quarzglasplatten vor, mit denen Sie das Frontvisier eines Hochgeschwindigkeitsflugzeugs optimieren möchten.
Vor etwa vierzig Jahren entwickelten NITS-Spezialisten die Technologie des Tiefbiegens. Mehrere Glasschichten werden in einen speziellen Ofen gelegt. Über mehrere Stunden bei hohen Temperaturen biegt sich das Glas unter seinem eigenen Gewicht und nimmt die gewünschte Form und Krümmung an. Bei Bedarf schieben spezielle Mechanismen das Werkstück und zwingen es, sich nach einem speziellen Zeitplan zu biegen.
Zum ersten Mal auf der Welt hat der MiG-29-Jäger mit dieser Technologie die aus drei Gläsern bestehende Laterne durch ein silikatfreies Glas ersetzt.
Mit zunehmender Geschwindigkeit stiegen die Anforderungen an die Hitzebeständigkeit der Verglasung, denen organisches Glas nicht mehr gewachsen war. Gleichzeitig wurden die optischen und visuellen Anforderungen verschärft. Vor einigen Jahren wurde in Zusammenarbeit mit der Sukhoi Company, der United Aircraft Corporation, eine neue Technologie zur Herstellung von Glas für die T-50 entwickelt.
Die Entwicklung wurde von Flugzeugherstellern, teilweise vom Ministerium für Industrie und Handel, finanziert. Erhebliche Unterstützung bei der technischen Umrüstung des Unternehmens wurde geleistet, sagt Yuri Tarasov, Direktor des UAC Technology Center.
Dadurch ist die Windschutzscheibe des T-50-Flugzeugs fast doppelt so groß wie das Visier der MiG-29, und die Form des Produkts aus einem klassischen Zylinder hat sich in ein komplexes 3D-Format verwandelt.
Das Ergebnis - zum ersten Mal auf der Welt wurde der vordere und klappbare Teil der T-50-Flugzeugkappe (hergestellt von Sukhoi) aus Silikatglas im 3D-Format hergestellt. Außerdem erwies sich das Gewicht dieser Teile als geringer als wenn sie aus organischem Glas wären.
Die erzielten Ergebnisse gaben den Anstoß, Flugzeuge anderer Fabriken und Konstruktionsbüros, die Teil des UAC sind, mit ähnlichen Verglasungen auszustatten. Sofort bestand Modernisierungsbedarf, um beispielsweise bei den Flugzeugen Yak-130, Su-35, MiG-31, MiG-35 organische Verglasungen durch Silikat zu ersetzen. Nach einem solchen Austausch (dh Verbesserung der Festigkeitseigenschaften der Verglasung) erreichte beispielsweise die MiG-35 erstmals eine Geschwindigkeit von bis zu 2000 km / h, konnte also 40% schneller fliegen im Durchschnitt als jedes andere Flugzeug der Welt.
In den letzten Jahren hat sich der Arbeitsstil der Moskauer Wissenschaftler stark verändert. Etwa dreihundert NITS-Spezialisten führen einen vollständigen Zyklus durch - von den technischen Spezifikationen bis zur Kleinserienfertigung. Dazu gehören die Entwicklung der Technologie und die Auswahl der Schlüsselmaterialien beim Einsatz von Glas sowie ein großer Testzyklus für alle Faktoren, die das Flugzeug am Boden und in der Luft beeinflussen.
An modernes Glas werden mehrere wesentliche Anforderungen gestellt, darunter neben hoher Festigkeit optische Transparenz, hohe Lichtdurchlässigkeit, Vergrößerung der Sichtweite, Entspiegelung, Schutz vor Sonneneinstrahlung und anderer Strahlung, Vereisungsschutz Eigenschaften, wodurch ein einheitlicher elektrischer Widerstand gewährleistet wird.
All dies wird durch Aerosol-, Vakuum- oder Magnetronbeschichtung erreicht. Leistungsstarke und ausgeklügelte Ausrüstung, die Metall verdampft und auf der Glasoberfläche abscheidet, ermöglicht es NITS, beliebige Beschichtungen aufzubringen, einschließlich solcher, die gegen spezielle Faktoren schützen.
Diese Eigenschaftskombination macht es möglich, von einem Verglasungsprodukt als einem komplexen optischen System zu sprechen, und die hohen Festigkeitseigenschaften von Glas, das Teil des Flugzeugcockpits ist, haben ein neues Gebiet von Wissenschaft und Technik geschaffen und den Begriff „Strukturoptik“eingeführt Produkte“(ICO).
Neue Technologien
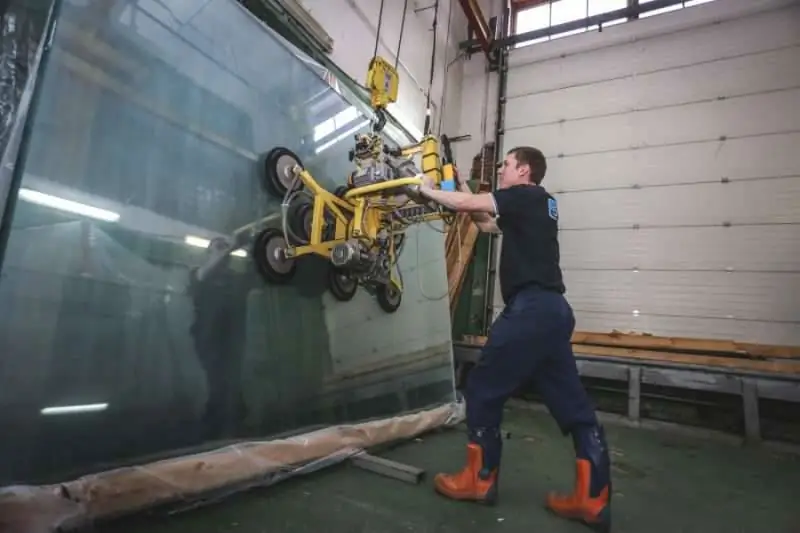
Auf dem Foto: Laden einer Glasscheibe zur Weiterverarbeitung.
Wenn das Produkt - der aufklappbare Teil der Laterne für den T-50 - zur Weiterverarbeitung aus dem Ofen entladen wird, gleicht es kaum noch einem zukünftigen Produkt. Beim Biegen von Glas werden die Kanten des Werkstücks verformt und können mit einem Diamantwerkzeug nicht von einem großformatigen Werkstück mit komplexer geometrischer Form entfernt werden. Der Laser kam zur Rettung. Der Laserstrahl des Roboterkomplexes schneidet das Werkstück nicht nur nach dem darin festgelegten Programm, sondern erhöht durch das Schmelzen der Kante auch die Festigkeit der Kante der Produkte und verhindert das Auftreten von Rissen. Das Laserschneiden von großformatigen 3D-Produkten wurde erstmals in Moskau eingesetzt. Diese Methode wurde im März 2012 patentiert. Mit dem Laserstrahl wird auch die elektrisch leitfähige Schicht auf der Glasoberfläche abgeschnitten, wodurch Heizzonen entstehen. Nach der Laserbearbeitung sieht das Werkstück immer mehr aus wie eine T-50-Taschenlampe.
Nach dem Zuschnitt wird jedes Werkstück auf einer 5-Achs-Maschine bearbeitet. Die einzigartige Anordnung ermöglicht es, keine anfänglichen Montagebelastungen darauf auszuüben. Der Cheftechnologe des Instituts, Alexander Sitkin, sprach über die Aussichten, den Komplex zum Schleifen und Polieren der Glasoberfläche zu nutzen: Arbeiten, die bei Bedarf nur noch manuell ausgeführt werden. Die entwickelten Technologien sind der Stolz des Instituts.
In jüngerer Zeit wurde ein fertiger Glasblock mit Hilfe einer Versiegelung in einen Metallrahmen montiert. Der Übergang zu Verbundwerkstoffen, die von NITS entwickelt wurden, ermöglichte es, das Gewicht des Produkts um 25 % zu reduzieren, die Vogelsicherheit und die Verglasungsressource auf das Niveau der Verglasungsverglasungsressource zu erhöhen. Es wurde möglich, die Verglasung im Feld zu ersetzen.
Der gesamte Produktionszyklus des ICO dauert etwa eineinhalb Monate. Die meisten Produkte gehen in die UAC-Fertigungswerke, einige zu Reparaturwerken zur Modernisierung und einige zu den Flugplätzen der Luftwaffe, in sogenannten Erste-Hilfe-Kästen. Der Hauptteil der NITS-Produkte wird im Rahmen der Landesverteidigungsordnung durchgeführt.
NITS gibt keine Informationen über die Eigenschaften von Verglasungen für Kampfflugzeuge weiter. Es ist jedoch klar, dass die für die Cockpits von inländischen Zivilflugzeugen entwickelten Brillen den importierten in einer Reihe von Parametern überlegen sind.
Wie Sie beispielsweise auf der NITS-Website sehen können, beträgt die Dicke des Glases bei der Tu-204 17 mm, die Dicke des Glases mit den gleichen Eigenschaften bei der Boeing 787 beträgt 45 mm.
Generation V
In den letzten Jahren ist es dem Institutsdirektor Vladimir Solinov gelungen, das Team deutlich zu verjüngen. In der Moskauer Produktion, die vor kurzem ihr 60-jähriges Bestehen feierte, arbeiten sowohl junge Leute als auch erfahrene Fachkräfte. Ältere Studenten von Mendeleevka kommen gerne hierher. Wenn sie am Institut praktizieren und erfahren, dass es Gehälter von 70.000 Rubel gibt, werden sie zuerst von einfachen Arbeitern beschäftigt, dann werden sie schnell zum Technologen. Es gibt auch viele erfahrene Arbeiter.
Einer von ihnen, Nikolai Yakunin, verarbeitet Glas für Hubschrauber. „Ich bin direkt nach der Armee hierher gekommen, vor vierzig Jahren. Aber ohne den hohen Automatisierungsgrad hätte es wahrscheinlich nicht überlebt. Es fällt mir schwer, den ganzen Tag selbst in guter körperlicher Verfassung mit einem Produkt mit einem Gewicht von 30 kg zu arbeiten“, sagt Yakunin.
Menschen und Nägel
Weltweit werden für den Flugzeugbau entwickelte Technologien, die die Herstellung von Gläsern mit der erforderlichen Festigkeit ermöglichen, in vielen anderen Sektoren der Volkswirtschaft eingesetzt.
Um die hohe Festigkeit von Silikatglas nachzuweisen, fertigte das Institut vor einigen Jahren … Glasnägel. Sie haben mich mit einem Hammer geschlagen. Sie könnten in Produkten mit antimagnetischen Eigenschaften Anwendung finden.
Außerdem wurden diese Nägel während des Baus getestet, anstelle von Klammern beim Verkleben von Yachtrümpfen. Aber die Nägel blieben nur exotisch. Jetzt muss niemand mehr die hohe Festigkeit von Glas beweisen - alle Arbeiten von NITS zeugen von der hohen Qualität dieses uralten und zugleich völlig neuen Materials.
Der Institutsdirektor Vladimir Solinov setzt alle seine Fähigkeiten ein, um die Notwendigkeit einer hohen Festigkeit von Glas, einschließlich Architektur und Konstruktion, nachzuweisen.
Er ist Mitglied der russisch-amerikanischen Kommission für Weltraumsicherheit, die zu Beginn dieses Artikels diskutiert wurde, sowie der Kommission für Stadtentwicklung unter der Staatsduma - immerhin beim Bau moderner Gebäude ein zunehmender Anteil der Materialien ist Glas. Damit werden für die Luftfahrt entwickelte Technologien und Materialien in naher Zukunft das Leben von Millionen Menschen komfortabler und sicherer machen.