Patriotismus der sowjetischen Industrieelite wurde mit gemeinsamer Verantwortung für das Endergebnis kombiniert
Die interindustrielle Interaktion zu allen Zeiten - sowohl im Russischen Reich als auch in der UdSSR und heute - gehörte nicht zu den Stärken der heimischen Industrie. Im Gegensatz zu Deutschland oder den Vereinigten Staaten, wo vertragliche Verpflichtungen eine unveränderliche und fast heilige Kraft hatten und haben.
Nehmen wir zum Beispiel das Verhältnis zwischen russischen Metallurgen und Maschinenbauern. In der zweiten Hälfte des 19. Jahrhunderts erhielten neue verkehrstechnische Anlagen und Werften von den Uraler Bergleuten nicht die erforderliche Menge an Industriemetallen. Letztere hielten es für unrentabel, viele relativ billige Walzprodukte herzustellen, da derselbe Gewinn durch eine viel geringere Menge an teurem Dacheisen erzielt wurde. Das fehlende Metall für Autoachsen, Motorwellen und Schiffshaut musste im Ausland gekauft werden. Erst gegen Ende des Jahrhunderts wurde das Problem von den südrussischen Hüttenwerken gelöst, die von belgischen oder französischen Industriellen gegründet wurden. Im Ural bauten die Franzosen auch ein Werk - Chusovskaya.
Es scheint, dass zu Sowjetzeiten solche Launen nicht in Frage kamen. Zudem versorgten die in den 30er Jahren errichteten Hüttenwerke das Land insgesamt mit Metall. Jedes Mal, wenn Maschinenbauer jedoch neue komplexe Arten von Walzprodukten nachfragten, beherrschten Metallurgen diese über Jahre oder sogar Jahrzehnte.
Abteilungsfeudalismus
Wenden wir uns der Geschichte von Uralvagonzavod zu. Bereits in den ersten Projekten war geplant, massivgewalzte Stahlräder unter den vierachsigen Wagen zu verwenden, als die Konstruktionskapazität ihre Konstruktionskapazität erreichte, deren Lieferant für das nahe gelegene Novo-Tagil Metallurgical Plant geplant war. Letzteres wurde jedoch von der Hüttenabteilung gebaut und verschob den Bau des Räderwalzwerks auf 1938-1942, und zwar nicht von vornherein. Infolgedessen begann der Fall nicht vor dem Krieg. Und nach dem Krieg interessierte sich der Radverleih nicht so sehr für Metallurgen. Ergebnis: Bis Mitte der 50er Jahre verließen Tagil-Autos das Werk auf kurzlebigen Gussrädern statt auf Stahlrädern. Dies brachte den Bahnarbeitern enorme Verluste, aber es gab keine Wahl: entweder solche Wagen oder keine.
Das gleiche geschah mit der Einführung niedriglegierter Stähle im Waggonbau. Sie versprachen eine spürbare Reduzierung des Eigengewichts des Rollmaterials unter Beibehaltung aller Leistungsmerkmale. Die Konstrukteure von Uralvagonzavod begannen Ende der 30er Jahre mit der Entwicklung von Autos aus niedriglegiertem Metall, deren Serienproduktion jedoch erst in der zweiten Hälfte der 50er Jahre begann, da Metallurgen weder geeignete Walzprodukte noch Ferrolegierungen für Gussteile lieferten.
Es muss gesagt werden, dass das Virus des Abteilungsfeudalismus die Maschinenbauer selbst betraf. Im Sommer 1937 ereignete sich eine interessante Geschichte, die die behördenübergreifenden Beziehungen dieser Zeit prägte. Die Hauptdirektion der Hüttenbetriebe hat Uralvagonzavod einen Auftrag über 5000 Tonnen Rohlinge für die kürzlich in Betrieb genommene Bandagenstraße des Werks Novo-Tagil geschickt. Die Hauptdirektion Verkehrstechnik war empört über den Eingriff in ein nachgeordnetes Unternehmen. Stellvertretender Chef der Hauptdirektion G. G. Am 11. Juli schickte Aleksandrov einen Brief an GUMP und Uralvagonzavod mit folgender Aussage: „Wir sind äußerst überrascht, dass die Lösung eines so wichtigen Problems wie der Organisation der Herstellung eines Bandagenrohlings in Uralvagonzavod ohne unsere Beteiligung durchgeführt wurde, und noch mehr - uns wurde nicht einmal eine Kopie des Outfits nach Uralvagonzavod geschickt … Ich bitte Sie, nur nach Absprache mit uns und über Glavtransmash ein festes Verfahren für die Herausgabe von Rohlingen an unsere Fabriken festzulegen."
Infolgedessen wurde den Metallurgen der Verbandsstahl verweigert, angeblich wegen der technischen Unmöglichkeit, qualitativ hochwertige Barren in der offenen Feuerstelle des Uralvagonzavod zu gießen. Inzwischen wurde hier bereits 1936 ein axialer Rohling gegossen und 1937 - Barren zum Blechwalzen. Daher mussten die Barren für die wenige Kilometer vom UVZ entfernte Mantelmühle aus den Werken Vyksa und Kuznetsk transportiert werden. Außerdem ließ ihre Qualität zu wünschen übrig, und die Liefermengen waren unzureichend.
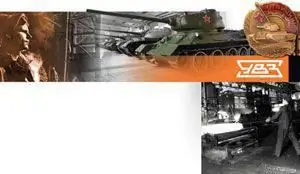
1938 wiederholte sich die Geschichte. Der Hauptabnehmer von UVZ-Barren war das Artilleriewerk Molotov (d. h. Perm), das Ende des Jahres eine Charge von Rohlingen erhielt. Und nur ein kleiner Teil von ihnen ging in die Verbandswerkstatt, die wieder das fehlende Metall für zwei- oder zweieinhalbtausend Kilometer importieren musste. Die Interessen der Industrie am Vertrieb von Uralwagonsawodsk-Stahl überwogen eindeutig.
Auch vor der Rüstungsindustrie blieb die Krankheit des Departements nicht verschont. Zahlreiche Veröffentlichungen zur Geschichte des sowjetischen Panzerbaus sind geradezu vollgestopft mit Beispielen, wie sich der Bau von Prototypen oder der Einsatz der Massenproduktion durch die Nichtlieferung von Metall, insbesondere Panzerung, verzögerte.
Und auch heute noch ist das sektorale Eigeninteresse nirgendwo hingegangen, es hat nur seine Form geändert. Anfragen nach neuen Formen von Walzprodukten werden einfach mit überhöhten Preisen abgewehrt. Über eine koordinierte Politik muss nicht gesprochen werden. Nach dem Einbruch des Rubelkurses zum Jahreswechsel 2014-2015 erhöhten die Hüttenunternehmen die Preise für Rollmaterial um 30-60 Prozent. Und sie fingen sofort an, sich über die Maschinenbauer wegen der gestiegenen Preise zu beschweren - schließlich werden die Maschinen in Russland produziert und sind nicht an den Dollarkurs gebunden.
Für branchenübergreifende Probleme scheint es in unserem Land nur ein Heilmittel zu geben: die Schaffung vertikal integrierter Systeme, bei denen das aus eigener Kraft geförderte Erz zunächst zu Metall und dann zu fertigen Maschinen verarbeitet wird.
Einheit im Krieg
Es gibt jedoch einen kurzen Zeitraum in unserer Geschichte, in dem die Interessen der Industrie in den Hintergrund gerückt sind. Wir sprechen über den Großen Vaterländischen Krieg. Der unbestrittene Patriotismus der damaligen sowjetischen Industrieelite verband sich mit der gemeinsamen Verantwortung aller an der Rüstungsproduktion Beteiligten für das Endergebnis. Das heißt, der Direktor des Panzerwalzwerks war nicht so sehr für die Menge an geschmolzenem und gewalztem Stahl verantwortlich, sondern für die Anzahl der gebauten Panzer.
Der wichtigste Schritt in diese Richtung wurde vom Direktor von NII-48 A. S. Zavyalov gemacht. In der Anfangszeit des Krieges wandte er sich an die Regierung mit dem Vorschlag, das Institut mit der Einführung von Technologien zur Herstellung von Spezialstählen und gepanzerten Konstruktionen bei Betrieben im Osten des Landes zu beauftragen, die sich zunächst mit der Herstellung von Panzern befassten Fahrzeuge. Anfang Juli leiteten Spezialistenteams von NII-48 die technologische Restrukturierung von 14 größten Unternehmen. Darunter waren die Hüttenwerke Magnitogorsk und Kusnezk, Hüttenwerke Novo-Tagil und Tschusowka, Uraler Schwermaschinenbau, Gorki Krasnoje Sormovo, Stalingrader Traktorenwerk, Stalingrader Roter Oktober und Nr. 264 Tabu der Vorkriegszeit: Auf der Liste standen die Betriebe von drei Volkskommissariaten.
Patriotismus und die zwangsweise Unterdrückung des Abteilungsegoismus haben der sowjetischen Metallurgie weder in der Vorkriegszeit noch in der Nachkriegszeit beispiellose Entwicklungsgeschwindigkeiten von Verteidigungsprodukten verschafft. Innerhalb weniger Monate wurde im Osten des Landes (hauptsächlich im Ural) die Produktion von Ferromangan, Ferrosilizium, Ferrochrom, Ferrovanadium und anderen Legierungen organisiert, ohne die es unmöglich ist, Panzerstahl zu erhalten. Nach dem Verlust der westlichen Regionen blieb Tscheljabinsk das einzige Ferrolegierungswerk in der UdSSR. Darauf wurde in kurzer Zeit die Verhüttung um das Zweieinhalbfache erhöht. Es wurden 25 Arten von Produkten hergestellt, die meisten waren jedoch aus verschiedenen Arten von Ferrochrom. Das Schmelzen von Ferromangan wurde in Hochöfen und nicht nur in alten Hochöfen mit niedriger Tonnage der Werke Nischni Tagil und Kushvinsky, sondern auch in einem großen modernen Ofen des Magnitogorsk-Kombinats eingerichtet. Entgegen allen Vorstellungen der Vorkriegszeit wurde Ferrochrom in der zweiten Hälfte des Jahres 1941 von Metallurgen der Werke Nischni Tagil und Serov in ihren Hochöfen geschmolzen, und Wissenschaftler der Uraler Zweigstelle der Akademie der Wissenschaften der UdSSR leisteten große Hilfe bei der Schaffung eines neuen Technologie. Später wurde das Schmelzen von Ferrosilicium in den Serov-Hochöfen gemeistert.
Weder im Ural noch in Westsibirien gab es vor dem Krieg gepanzerte Lager, sie mussten von Unternehmen, die sich in der Kampfzone befanden, hastig verlegt werden.
Im Sommer 1941 war die evakuierte Ausrüstung noch unterwegs. Und dann schlug der Chefmechaniker des Magnitogorsk-Kombinats N. A. Ryzhenko vor, die Rüstung auf einer blühenden Mühle zu rollen. Trotz des großen Risikos wurde die Idee umgesetzt. Und im Oktober wurde ein Panzerlager aus dem Werk Mariupol in Betrieb genommen. Es wurde in nur 54 Tagen zusammengebaut. Nach Vorkriegsstandards dauerte dies ein Jahr.
Das Werk Novo-Tagil bekam das Lager aus Leningrad. Die Vorbereitungen für seine Aufnahme begannen im Juli, zunächst wurde davon ausgegangen, dass es an der Stelle der Bandage montiert werden würde. Das Verbandslager wurde demontiert, es stellte sich jedoch heraus, dass der Altbestand für den Aufbau des Panzerlagers nicht ausreichte und an anderer Stelle platziert werden musste. Der Krieg, der bis vor kurzem als unmöglich galt: Noch vor einem Jahr hatten Versuche, in Nischni Tagil einen Industriebau im integrierten "High-Speed"-Verfahren durchzuführen, allenfalls einen Teilerfolg, im Sommer 1941 den meisten komplexer Baubetrieb war nahezu perfekt. Am 10. September wurde das erste Tagil-Stahlblech einen Monat früher als geplant gewalzt. Insgesamt wurden bis Ende des Jahres 13.650 Tonnen Blech erhalten, darunter etwa 60 Prozent der Panzerung (das Werk wurde auf Kohlenstoffstahl getestet und von Oktober bis Dezember wurde Kohlenstoffstahl mit einem Mangel an Panzerbarren gewalzt).. Infolgedessen überschritt die monatliche Produktion von Panzerplatten in den Ural-Werken bereits im Januar 1942 in der gesamten Vorkriegssowjetunion sechs Monate.
Nicht weniger überraschende Ereignisse fanden bei anderen wenig bekannten Unternehmen statt. Während des Krieges war das Hüttenwerk Zlatoust dem Magnitogorsk-Kombinat in Bezug auf die Menge an Schmelz- und Walzstahl unterlegen, aber es übertraf es deutlich in seinem Produktmix - hier wurden etwa 300 Sorten von legiertem und Kohlenstoffstahl hergestellt. Ohne Lieferungen aus Zlatoust wäre die Produktion vieler Waffentypen, vor allem Panzermotoren, eingestellt worden.
Bei der Produktion von Kleinserien aus besonders hochwertigem Stahl erwiesen sich alte Uraler Fabriken als unverzichtbar. In jeden sowjetischen Panzer wurde beispielsweise Metall von Serov Metallurgical, dem Haupthersteller von kalibrierten Walzprodukten, investiert. Das Werk Nizhnesalda stellte auf Nickel-Eisen- und Stahlverhüttung um. Diese Liste lässt sich endlos fortsetzen - in den Kriegsjahren wurde überall dort, wo es mindestens eine Kuppel gab, waffenfähiges Metall geschmolzen.
Es gibt eine kuriose Geschichte mit Flussmitteln für das automatische Schweißen. Vor und zu Beginn des Krieges wurden sie in einem der Unternehmen von Donbass eingeschmolzen, nach deren Besetzung die zentralisierte Versorgung vollständig eingestellt wurde. Ende 1941 begannen Mitarbeiter des Instituts für Elektroschweißen der Akademie der Wissenschaften der Ukrainischen SSR nach Ersatzmaterialien zu suchen, die im Ural in mehr oder weniger brauchbarem Zustand verfügbar waren. Und sie fanden sie - in Form von Hochofenschlacken des Hüttenwerks Ashinskiy. Es waren nur kleine Verbesserungen nötig: Die Hochöfen reicherten ihre Schlacken mit Mangan an und machten sie dadurch zu einem vollkommen geeigneten Flussmittel. Die zum Testen notwendige Ausrüstung wurde aus Nischni Tagil direkt nach Asha gebracht.
Beispiele für die lokale Zusammenarbeit zwischen Tank- und Hüttenwerken sind sehr bezeichnend. Vor der Inbetriebnahme eigener Anlagen wurde die Wärmebehandlung von Tankteilen des Ural-Tankwerks Nr. 183 im Metallurgiewerk Nischni Tagil durchgeführt.
Die erfolgreiche Arbeit der UTZ-Gießereiarbeiter wurde durch die Unterstützung des benachbarten Schamottewerks Nizhniy Tagil, das die Produktion hochwertiger feuerfester Feuersteinstopfen etablierte, wesentlich erleichtert. Dies ermöglichte ein problemloses Gießen von schweren Panzerstahlschmelzen für den Formguss.
In den Jahren 1942-1945 wurden die Offenherdöfen bei UTZ hauptsächlich mit Koksofen- und Hochofengas aus den Hüttenwerken Novo-Tagil und Kokerei Nischni Tagil betrieben. Die Gaspipeline ist seit Februar 1942 in Betrieb. Das eigene Gaskraftwerk des Werks Nr. 183 deckte nicht mehr als 40 Prozent des Bedarfs.
Manchmal genügte ein einfacher Rat, um ein Problem zu lösen. Die Informationen lokaler Metallurgen über eine kleine Manganmine, die in den 1870er Jahren entwickelt wurde, halfen, mehrere Wochen vor Beginn der Lieferungen von Ferromangan zu überleben, ohne das Gießen von Panzerketten zu stoppen.
Ein weiteres Beispiel: Als die Produktion von Panzerstahl zunahm, konnte die Feuerstelle mit der Metallverhüttung für die Köpfe von Fliegerbomben nicht mehr mithalten. Es war nicht möglich, es von außen zu bekommen. Direktor Yu E. Maksarev erinnerte sich in seinen Memoiren an den weiteren Verlauf der Ereignisse: „Als ich bei einer der Sitzungen im Stadtkomitee war, traf ich den Direktor des alten, noch immer Demidov-Werks und bat, mir die Besetzung von die Bombenköpfe. Er sagte: Mit Stahl kann ich nicht helfen, aber mit Ratschlägen helfe ich. Und als ich zu seinem Werk kam, zeigte er mir einen eineinhalb Tonnen schweren Bessemer-Konverter mit mittlerer Blasung. Er gab mir die Zeichnungen und sagte, dass er weiß, dass wir eine gute mechanisierte Eisengießerei haben und Ihre Konverter schweißen werden. So erschien der Auftrag für das Werk vom 8. September 1942 auf der Organisation in der Griffin-Radwerkstatt des Bessemer-Abschnitts von drei kleinen Konvertern (jeweils anderthalb Tonnen Metall). Bis zum 25. September wurde das Projekt von der Konstruktions- und Technologieabteilung der Kapitalbauleitung vorbereitet, die Spezialisten der Hauptmechanikerabteilung schweißten schnell Konverter und Kessel - Flüssigeisenlagertanks. Der Probelauf der Bessemer-Abteilung und das Gießen einer Versuchscharge von fünf Teilebezeichnungen fanden an der Wende Oktober/November 1942 statt. Ende November begann die Serienproduktion.
Zum Schluss des Themas: Die Zusammenarbeit von Metallurgen und Panzerbauern in Kriegszeiten wirkte in beide Richtungen. Die Monteure des Ural-Tankwerks nahmen an der Inbetriebnahme vieler neuer Einheiten des Hüttenwerks Novo-Tagil teil. Im Mai 1944 wurde in der Panzerturmgießerei eine bedeutende Anzahl von Auskleidungsplatten für die Reparatur des Hochofens hergestellt.
Aber der Hauptassistent der Metallurgen war natürlich das Uraler Schwermaschinenbauwerk. Die Auftragsbücher der UZTM für 1942-1945 sind buchstäblich vollgepackt mit Dokumenten über die Herstellung von Ersatzteilen und Geräten für metallurgische Zwecke - sowohl für den Bedarf der Panzerindustrie als auch für die Betriebe des Volkskommissariats für Eisenhüttenkunde. Im Herbst 1942 wurde am UZTM offiziell eine Sonderabteilung für die Herstellung von Ausrüstungen für Hüttenwerke wiederhergestellt. Es erhielt den Code "Abteilung 15" und war dem stellvertretenden Direktor für Beschaffungsgeschäfte und Rumpfproduktion unterstellt.
Erfolg am Schnittpunkt der Branchen
Die Zusammenarbeit von Metallurgen und Panzerbauern hat zur Entwicklung einer Reihe von Technologien geführt, die ohne Übertreibung als echte wissenschaftliche und technische Durchbrüche bezeichnet werden können.
Nachdem sie Panzerstahl geschmolzen und zu Blechen gewalzt hatten, überführten Metallurgen ihre Produkte in die Panzerrumpfproduktion. Hier wurde das Metall entsprechend der Schablone in die entsprechenden Teile geschnitten. Bei der Produktion von "Vierunddreißig" bereiteten vor allem zwei Teile des Rumpfes viel Ärger: Kotflügel (die schräge Seite der Seite) und die vertikale Seitenplatte. Beide waren lang, sogar in breiten Streifen mit schrägen Schnitten an den Rändern.
Da lag die Idee nahe, einen Messstreifen in der Breite der fertigen Teile zu rollen. Es wurde erstmals im Sommer 1941 von den Panzerwagen des Werks Mariupol formuliert. Für das Probewalzen haben wir uns für ein Brammenwalzwerk in Zaporizhstal entschieden, in das zwei Staffeln von Panzerbarren geschickt wurden. Aber dann hatten sie keine Zeit, zur Sache zu kommen: Die vorrückenden deutschen Truppen nahmen sowohl die Ränge als auch Saporoschje selbst gefangen.
An der Wende von 1941-1942, während der Evakuierung und der Entwicklung der Rüstungsproduktion in den neuen Fabriken, gab es nicht genug Streifen. Im Mai 1942 erhielt das Volkskommissariat für Eisenhüttenkunde jedoch erneut den Auftrag, es für T-34- und KV-Panzer zu mieten. Die Aufgabe stellte sich als schwierig heraus: Die Breitentoleranzen sollten -2/+5 Millimeter nicht überschreiten, die Halbmondform (Biegung) für die Gesamtlänge des Teils betrug 5 Millimeter. An den Rändern waren Risse, Sonnenuntergänge und Delaminationen nicht zulässig, damit das Schweißen ohne spanende Bearbeitung oder Brennschneiden durchgeführt werden konnte.
Die Versuchsarbeiten begannen gleichzeitig in den Walzwerken der Hüttenwerke Magnitogorsk und Kusnezk, zunächst ohne besondere Erfolge. Die Vermietung von Teilen für die KV-Panzer wurde bald aufgegeben, aber der T-34 war schließlich erfolgreich. Das Autorenteam bestehend aus dem Leiter der metallurgischen Abteilung der NII-48 G. A. Vinogradov, dem Chefingenieur der KMK L. E. Vaisberg und dem Ingenieur des gleichen Werkes S. E. steht "900" des Eisenbahn- und Strukturwerks ist eine völlig neue Methode des Rollens "am Rand". Im Januar 1943 wurden 280 Streifen ausgegeben, im Februar - 486, im März - 1636 Stück. Im April begann nach allen erforderlichen Tests die Entwicklung der Bruttoproduktion von Messstreifen für die Radlaufverkleidungen von T-34-Panzern. Zunächst wurden sie an UZTM und das Ural Tank Plant und dann an andere Fabriken - Hersteller von T-34-Panzern - geliefert. Der Schrott, der ursprünglich 9,2 Prozent betrug, war bis Oktober 1943 auf 2,5 Prozent gesunken, und die minderwertigen Streifen wurden zur Herstellung kleinerer Teile verwendet.
Eine vollständige und zutreffende Einschätzung der neuen Technologie gibt der entsprechende Bericht von TsNII-48 vom 25.12.1943: „Eine grundlegend neue Methode zum Walzen eines breiten Panzerstreifens“am Rand „wurde entwickelt, getestet und in die Bruttoproduktion eingeführt“., die bis vor kurzem in der UdSSR und im Ausland als undurchführbar galt. Der Erhalt eines kalibrierten (gemessenen) Streifens mit einer Breite des fertigen Teils des gepanzerten Rumpfes des T-34-Panzers ermöglichte es den NKTP-Fabriken, eine neue Hochleistungstechnologie für die Herstellung von gepanzerten Teilen ohne Schneiden von Längskanten einzusetzen. Dank der Anwendung der neuen Methode auf einen der wichtigsten gepanzerten Teile des T-34-Panzers (Kotflügel) wurde beim Ausschneiden eine sehr erhebliche Zeitersparnis (ca. 36 %) erzielt. Erzielte Einsparungen von 8C-Panzerstahl bis zu 15 Prozent und Sauerstoffeinsparungen von 15.000 cbm pro 1000 Rümpfe“.
Bis Ende 1943 wurde das Rollen eines Messstreifens für einen anderen Teil des T-34-Rumpfs - den vertikalen Teil der Seite - gemeistert. Es bleibt nur hinzuzufügen, dass die Autoren dieser Erfindung 1943 mit dem Stalin-Preis ausgezeichnet wurden.
Im selben Jahr 1943 wurde durch gemeinsame Bemühungen des Labors des Ukrainischen Instituts für Metalle (unter der Leitung von PA Aleksandrov) und der Arbeiter des Kusnezker Metallurgischen Kombinats und des Uraler Tankwerks ein spezielles periodisches Walzprofil entwickelt und in der Produktion für die Beschaffung beherrscht von Masse und kritischen Teilen der "vierunddreißig" - Balancer-Achsen. Die erste Versuchscharge eines periodischen Profils ging im Dezember bei KMK ein, Anfang 1944 begann die Serienproduktion. Bis Oktober stellte das Uraler Panzerwerk komplett auf die Herstellung von Ausgleichsachsen aus einem neuen Rohling um, Ende des Jahres kam UZTM dazu. Dadurch konnte die Produktivität der Schmiedehämmer um 63 Prozent gesteigert und die Anzahl der Teilebrüche verringert werden.
Die erfolgreiche Arbeit der Panzerbauer wurde durch das Rollmaterial des Bandagenwerks des Hüttenwerks Novo-Tagil erheblich erleichtert. Ab Frühjahr 1942 lieferten sie gerollte Schultergurte mit reduzierten Bearbeitungszugaben, 1943 wurden die Zulagen wieder reduziert. In Kombination mit dem neuen Schneidwerkzeug war es so möglich, das zeitaufwendige Abisolieren der Schultergurte termingerecht und stressfrei durchzuführen. Ein seltener Fall: Der Volkskommissar der Panzerindustrie V. A. Malyshev hielt es in seinem Befehl vom 28. September 1943 für notwendig, den Tagil-Metallurgen einen besonderen Dank auszusprechen.
Und schließlich das letzte Beispiel: 1943 wurden die Felgen der T-34-Stützpanzer zunächst im Werk Tscheljabinsk Kirov und dann in anderen Unternehmen aus speziellen profilierten Walzprodukten hergestellt. Dieser Erfolg wurde auch im Auftrag von V. A. Malyshev festgestellt.
Es bleibt hinzuzufügen, dass die Spezialisten der amerikanischen Firma "Chrysler", die den in Korea erbeuteten Panzer T-34-85 untersucht hatten, insbesondere die Perfektion der Stahlrohlinge bemerkten, aus denen das Kampffahrzeug hergestellt wurde. Und auch die Tatsache, dass sie den Produkten der US-Metallurgieunternehmen oft zahlenmäßig überlegen waren.