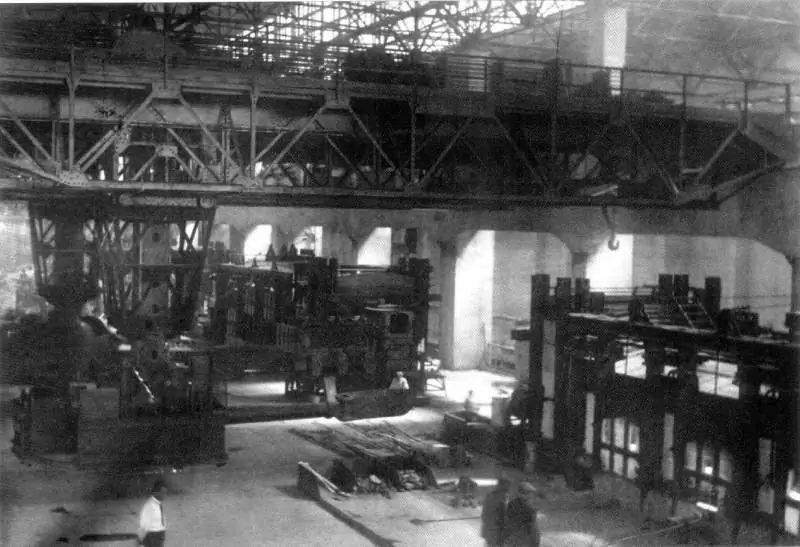
Strategische Ressource
Die Produktion von hochwertigem Stahl für den militärisch-industriellen Komplex unter Kriegsbedingungen ist schwer zu überschätzen. Dies ist einer der wichtigsten Faktoren für den Erfolg von Armeen auf dem Schlachtfeld.
Wie Sie wissen, gehörten die Metallurgen von Krupp zu den ersten, die die Herstellung von hochwertigem Waffenstahl gelernt haben.
Ende des 19. Jahrhunderts übernahmen die Deutschen das Thomas-Fertigungsverfahren. Diese Methode der Stahlschmelze ermöglichte es, Phosphorverunreinigungen aus dem Erz zu entfernen, was automatisch die Qualität des Produkts erhöhte. Hochwertiger Rüstungs- und Waffenstahl sorgte im Ersten Weltkrieg oft für die Überlegenheit der Deutschen auf dem Schlachtfeld.
Um eine solche Produktion zu organisieren, waren neue feuerfeste Materialien erforderlich, die die Innenflächen der Öfen auskleideten. Die Deutschen verwendeten für ihre Zeit die neuesten Magnesit-Feuerfestmaterialien, die Temperaturen von über 2000 Grad standhielten. Solche Stoffe höherer Feuerfestigkeit basieren auf Magnesiumoxiden mit geringen Beimengungen von Aluminiumoxiden.
Zu Beginn des 20. Jahrhunderts konnten sich Länder mit Technologien zur Massenproduktion von Magnesit-Feuerfesten die Herstellung hochwertiger Panzer- und Geschützrohre leisten. Dies kann mit einem strategischen Vorteil verglichen werden.
Niedriger in Bezug auf die Feuerbeständigkeit waren die sogenannten hochfeuerfesten Materialien, die Temperaturen von 1750 bis 1950 Grad standhalten. Dies sind feuerfeste Materialien aus Dolomit und Aluminiumoxid. Schamotte, Halbsäure, Quarz und feuerfeste Materialien von Dinas können Temperaturen von 1610 bis 1750 Grad standhalten.
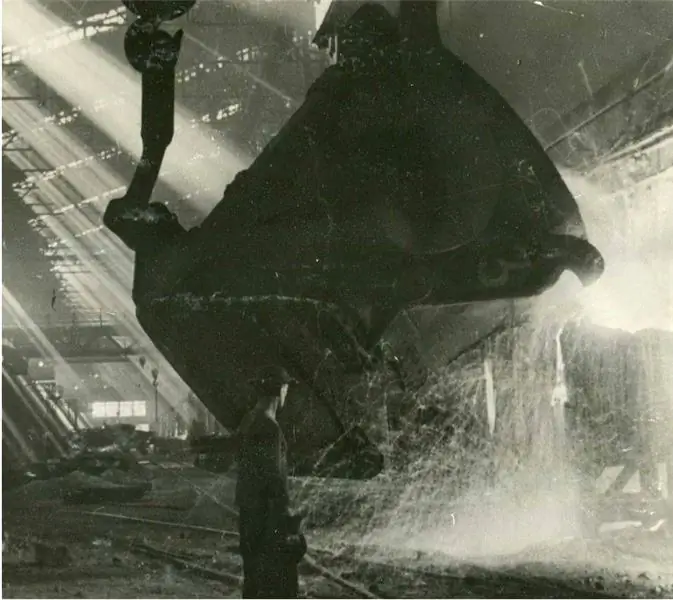
In Russland tauchten übrigens bereits im Jahr 1900 erstmals Technologien und Standorte zur Herstellung von Magnesit-Feuerfestmaterialien auf.
Der feuerfeste Satka-Magnesitstein wurde 1905 auf der Weltindustrieausstellung in Lüttich mit einer Goldmedaille ausgezeichnet. Es wurde in der Nähe von Tscheljabinsk in der Stadt Satka produziert, wo sich eine einzigartige Magnesitlagerstätte befand.
Das Periklas-Mineral, aus dem die feuerfesten Materialien im Werk hergestellt wurden, war von hoher Qualität und erforderte keine zusätzliche Anreicherung. Dadurch war das Magnesit-Feuerfest von Satka seinen Pendants aus Griechenland und Österreich überlegen.
Schließung der Lücke
Trotz des recht hochwertigen Magnesitziegels aus Satka waren bis in die 30er Jahre die wichtigsten feuerfesten Materialien der sowjetischen Metallurgen Dina-Materialien aus Ton. Natürlich hat es nicht funktioniert, eine hohe Temperatur zum Schmelzen von Waffenstahl zu erreichen - die Auskleidung der Innenseiten von Offenherdöfen bröckelte und erforderte außergewöhnliche Reparaturen.
Es gab nicht genug Satka-Ziegel, und in der Zeit nach der Revolution gingen die wichtigsten Produktionstechnologien verloren.
Gleichzeitig gingen die Europäer voran - beispielsweise zeichnete sich der österreichische Magnesit Radex durch eine hervorragende Feuerbeständigkeit aus.
Die Sowjetunion kaufte dieses Material. Aber es war unmöglich, ein Analogon ohne Produktionsgeheimnis zu bekommen. Dieses Problem wurde von einem Absolventen der Moskauer Staatlichen Technischen Universität aufgegriffen. N. E. Bauman Alexej Petrowitsch Panarin. Im Magnetwerk (ehemals Satka-Kombinat) leitete er 1933 das Zentrale Pflanzenlabor. Und fünf Jahre später startete er die Massenproduktion von Periklas-Chromit- oder Chromomagnesit-Feuerfestmaterialien für Offenherdöfen.
Im Hüttenwerk Zlatoust und im Moskauer Hammer und Sichelwerk ersetzte Panarins feuerfestes Material die veralteten Dinas.
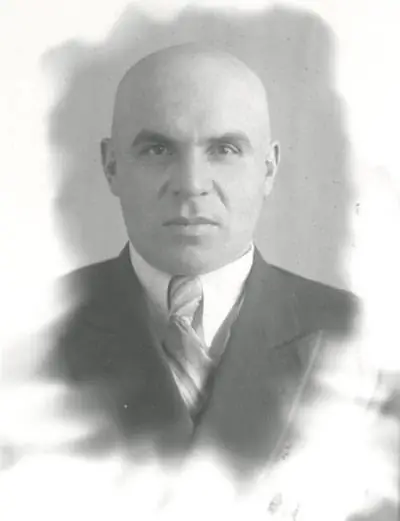
Die seit mehreren Jahren im Labor von „Magnezit“entwickelte Technologie bestand in einer besonderen Zusammensetzung und Partikelgröße.
Bisher produzierte das Werk konventionelle Chrom-Magnesit-Steine, bestehend aus Magnesit und Chrom-Eisenerz, im Verhältnis 50/50. Das von Panarins Gruppe enthüllte Geheimnis lautete wie folgt:
„Wenn Chromiterz in grobkörnigen Körnern mit einem Mindestgehalt an Fraktionen von weniger als 0,5 mm zu einer gewöhnlichen Magnesitcharge hinzugefügt wird, erhöht sich selbst bei einer Zugabe von 10 % eines solchen Erzes die thermische Stabilität des Ziegels stark.
Mit zunehmender Zugabe von Chromiterz grober Körnung wächst die Stabilität des Ziegels und erreicht bei einem bestimmten Komponentenverhältnis ein Maximum."
Chromit für das neue feuerfeste Material wurde in der Mine Saranovskoje gewonnen, und in Satka wurde weiterhin Periklas abgebaut.
Zum Vergleich: Ein gewöhnlicher "vorrevolutionärer" Magnesitziegel hielt Temperaturen 5-6 mal weniger stand als die Neuheit von Panarin.
In der Kupferschmelze Kirovograd hielt das feuerfeste Chrom-Magnesit-Material im Dach eines Hallofens 151 Tage lang Temperaturen von bis zu 1550 Grad stand. Bisher mussten Feuerfestmaterialien in solchen Öfen alle 20-30 Tage gewechselt werden.
Bis 1941 wurde die Herstellung von Großfeuerfesten beherrscht, die es ermöglichten, die Materialien in großen Stahlöfen bei Temperaturen bis zu 1800 Grad zu verwenden. Einen wichtigen Beitrag dazu leistete der technische Leiter von „Magnezit“Alexander Frenkel, der eine neue Methode zur Befestigung des feuerfesten Materials auf den Dächern der Öfen entwickelte.
Feuerfest für den Sieg
Ende 1941 gelang den Metallurgen von Magnitka das bisher Undenkbare - zum ersten Mal in der Geschichte beherrschten sie das Schmelzen von Panzerstahl für T-34-Panzer in den wichtigsten schweren Herdöfen.
Der Hauptlieferant von Feuerfestmaterial für einen so wichtigen Prozess war Satka "Magnezit". Über die Schwierigkeiten des Krieges braucht man nicht zu sprechen, als ein Drittel der Fabrikarbeiter an die Front gerufen wurde und der Staat eine Übererfüllung des Plans forderte. Trotzdem machte das Werk seine Arbeit, und Panarin 1943
„Für die Beherrschung der Herstellung hochfeuerfester Produkte aus heimischen Rohstoffen für die Eisenmetallurgie“
wurde mit dem Stalin-Preis ausgezeichnet.
1944 wird dieser Metallurg-Forscher eine Technologie zur Herstellung von hochwertigem Magnesit-Pulver "Extra" entwickeln. Aus diesem Halbzeug wurde ein gepresstes Feuerfestmaterial hergestellt, das bei der besonders wichtigen Herstellung von Panzerstahl in Elektroöfen verwendet wird. Die Temperaturgrenze für solche Feuerfestmaterialien erreichte 2000 Grad.
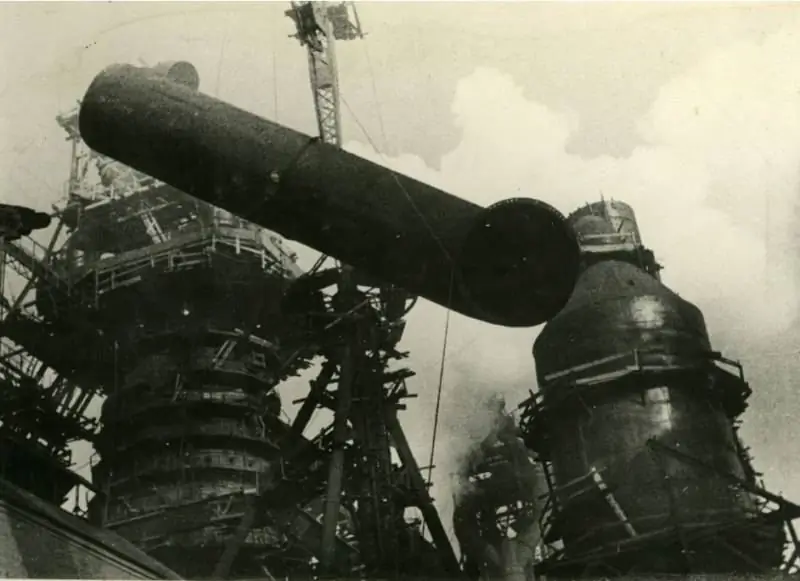
Aber man sollte nicht davon ausgehen, dass sich das Beispiel einer allgemein erfolgreichen Magnezit-Anlage auf die gesamte Feuerfestindustrie der Sowjetunion erstreckte.
Eine besonders schwierige Situation entwickelte sich im Ural, wo 1941-1942 praktisch das gesamte Panzergebäude des Landes evakuiert wurde.
Die Hüttenwerke Magnitogorsk und Novotagilsk wurden auf die Herstellung von Rüstungen umorientiert und lieferten Produkte an Swerdlowsk Uralmasch, Tscheljabinsk "Tankograd" und Nischni Tagil Tankwerk Nr. 183. Gleichzeitig hatten die Hüttenwerke eine eigene Produktion von feuerfestem Material aus lokalen Rohstoffen.
In Magnitka zum Beispiel produzierte das Dinas-Schamotte-Werk 65-70 Tausend Tonnen Ziegel pro Jahr. Dies reichte nicht einmal für den eigenen Bedarf, von der Lieferung an andere Unternehmen ganz zu schweigen.
Die ersten Schwierigkeiten traten auf, als Tankfabriken begannen, eigene Heiz- und Wärmeöfen zu bauen. In der Uraler Metallurgie gab es bereits kaum genug Feuerfestmaterialien, und dann erforderte die Rumpfproduktion von Panzerfabriken hochwertige Materialien für die Auskleidung der Öfen.
Von feuerfestem Chromomagnesit war hier keine Rede - dieses Material war Mangelware und wurde sogar gegen American Lend-Lease exportiert. Zumindest wird dies in einer Reihe von Quellen erwähnt. Ural-Historiker schreiben, dass Panarins teures Chromomagnesit im Austausch gegen knappe Ferrolegierungen für Panzerpanzerung ins Ausland gehen könnte. Aber es gibt noch keine direkten Beweise dafür.
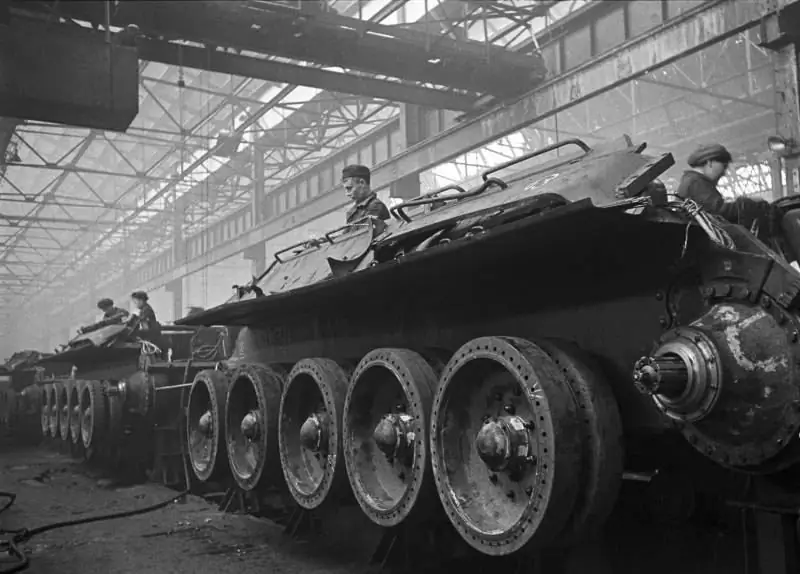
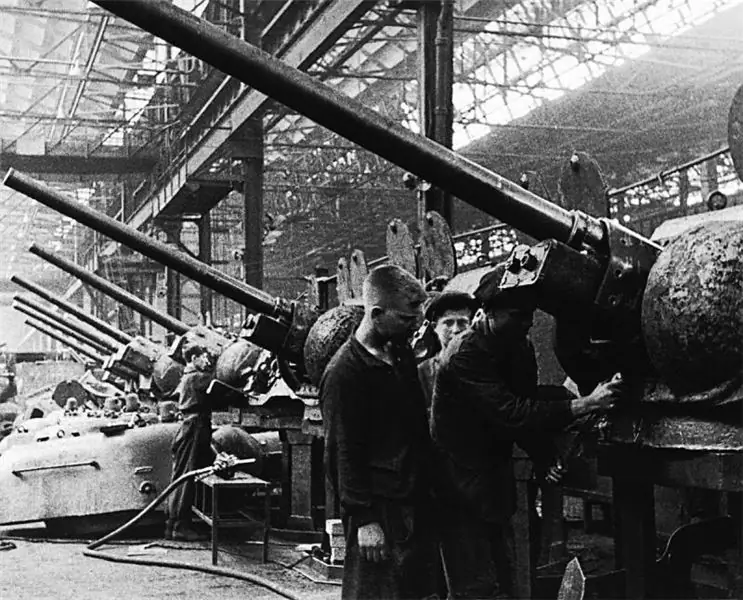
Die Tankfabriken verließen sich hauptsächlich auf das feuerfeste Material von Dinas, das im Werk Pervouralsk hergestellt wurde. Aber erstens wurden nur 12 Tausend Tonnen pro Monat produziert, und zweitens nahmen Metallurgen den Löwenanteil ein.
Der Ausbau der Produktion im Werk Perwouralsk verlief sehr langsam. Und bis Mitte 1942 erschienen nur 4 neue Öfen. Der Rest war entweder nicht fertig oder existierte im Allgemeinen nur in Projekten.
Feuerfeststoffe für Offenherdöfen von Tankfabriken kamen oft von schlechter Qualität, nicht vollständig und zum falschen Zeitpunkt. Allein für die Reparatur der Uralmasch-Öfen im vierten Quartal 1942 wurden 1035 Tonnen feuerfeste Ziegelsteine benötigt, und nur etwa 827 Tonnen gingen ein.
Im Jahr 1943 wurde die Feuerstelle von Uralmash im Allgemeinen aufgrund des Mangels an feuerfesten Materialien für die Reparatur fast eingestellt.
Die Qualität der während des Krieges gelieferten Feuerfestmaterialien ließ zu wünschen übrig. Wenn der Dinas-Ziegel des Offenherdofens unter normalen Bedingungen 400 Hitzen standhalten konnte, überstieg er in Kriegszeiten 135 Hitzen nicht. Und bis März 1943 war dieser Parameter auf 30-40 Vorläufe gesunken.
Diese Situation zeigt deutlich, wie der Mangel an einer Ressource (in diesem Fall Feuerfest) die Arbeit der gesamten Verteidigungsindustrie ernsthaft verlangsamen kann. Wie der Kandidat der Geschichtswissenschaften Nikita Melnikov in seinen Werken schreibt, hielten im März 1943 immer noch drei offene Herdöfen von Uralmasch an und führten einen vollständigen Reparaturzyklus durch. Es brauchte 2346 Tonnen Dinas, 580 Tonnen Schamotte und 86 Tonnen Magnesit.
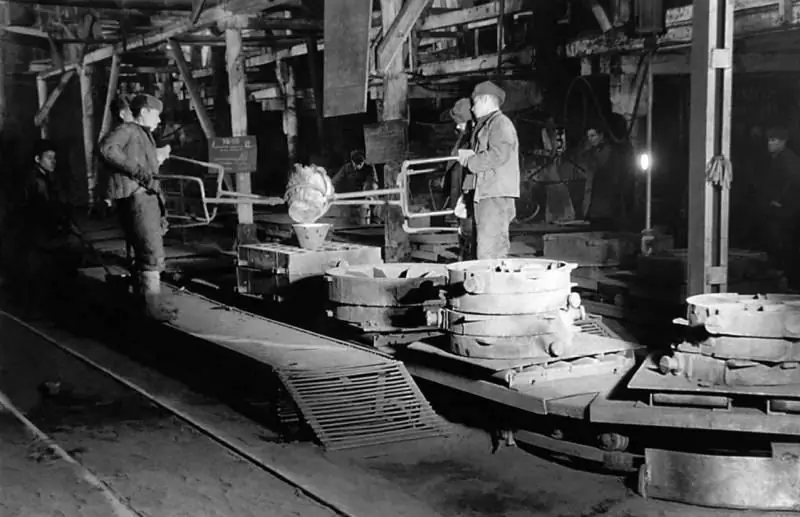
Mitte 1942 entwickelte sich die Situation im Panzerwerk Nr. 183 ähnlich - die Stahlproduktion hinkte der mechanischen Montage hinterher. Und wir mussten die T-34-Rümpfe aus Uralmash "importieren".
Einer der Gründe war das Fehlen von Feuerfestmaterial für die Reparatur von Herdöfen, die im Frühjahr 1942 an ihre Grenzen liefen. Infolgedessen waren im Herbst nur noch 2 von 6 Offenherdöfen in Betrieb, die Schmelzmengen wurden erst in der zweiten Jahreshälfte 1943 wiederhergestellt.
Die Situation mit feuerfesten Materialien in der Struktur des sowjetischen Verteidigungskomplexes während des Großen Vaterländischen Krieges verdeutlicht die Komplexität der Situation im Hinterland des Landes.
Ein chronischer Mangel an im Allgemeinen nicht dem Hightech-Produkt wirkte sich direkt auf das Produktionstempo von gepanzerten Fahrzeugen aus.