Krieg ist bekanntlich der beste Motor des Fortschritts. Die Panzerindustrie der Sowjetunion hat in nur wenigen Kriegsjahren einen schwindelerregenden Qualitätssprung gemacht. Die wahre Krone davon waren die Panzer der IS-Serie.
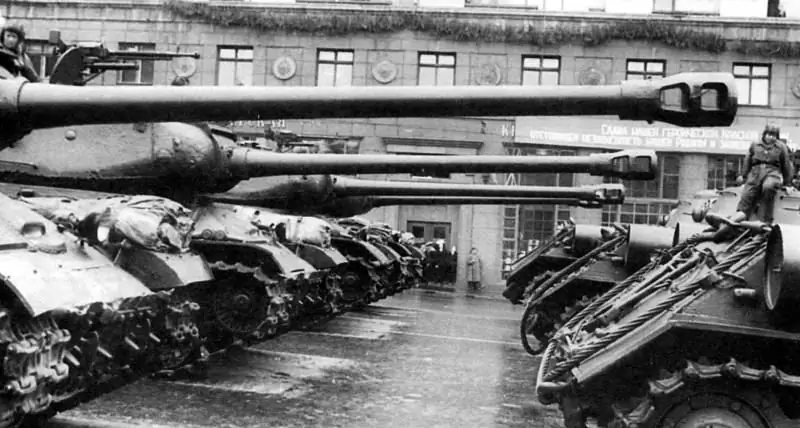
Rezepte für Magnitogorsk
Im vorherigen Teil der Geschichte ging es um die 70-Liter-Gusspanzerung mit hoher Härte, die für die Türme der IS-Panzer verwendet wird. Die Panzerentwickler von TsNII-48 hatten noch lange nicht die ersten Erfahrungen mit dem Schutz schwerer Panzer.
Vor der Kursker Ausbuchtung, die zu einem Katalysator für die Entwicklung des inländischen schweren Panzerbaus wurde, war das Hauptobjekt der Modernisierung der KV-Panzer. Alle Arbeiten zielten zunächst darauf ab, den Anteil knapper Legierungszusätze in der Zusammensetzung der Panzerung zu reduzieren. Schon der Name in TsNII-48 hat einen passenden gefunden - wirtschaftlich legierter Stahl. Die Originalpanzerung der Marke FD-7954, mit der der KV-Panzer in den Großen Vaterländischen Krieg eintrat, enthielt nach technischen Anforderungen bis zu 0,45% Molybdän, 2,7% Nickel und Chrom.
Ende 1941 erstellte eine Gruppe von Forschern unter der Leitung von Andrei Sergeevich Zavyalov am Armored Institute ein Rezept für den Stahl FD-6633 oder 49C, bei dem Molybdän nicht mehr als 0,3%, Chrom - bis zu 2,3% und Nickel - benötigte. bis zu 1,5%. Wenn man bedenkt, dass die Panzer der KV-Serie aus der zweiten Hälfte von 1941 bis 1943 etwa 4 Tausend Exemplare gesammelt haben, kann man sich die tatsächlichen Einsparungen bei Legierungsmetallen vorstellen.
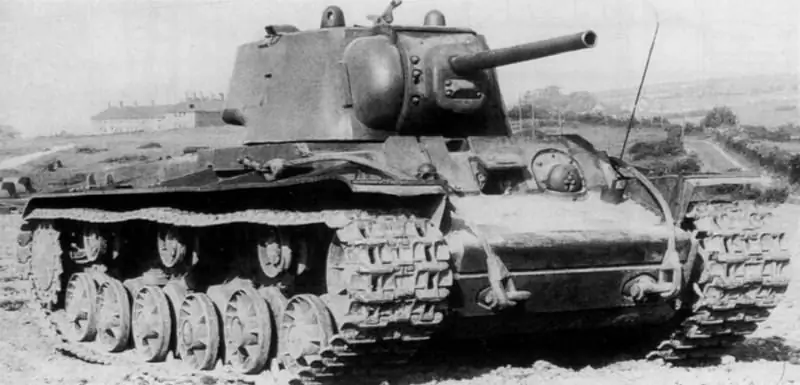
Das Erfolgsgeheimnis
Das Erfolgsgeheimnis der Metallurgen liegt in der Untersuchung der Parameter der Bildung von Faserbruch der Panzerung - dem Hauptparameter der Projektilbeständigkeit. Es stellte sich heraus, dass man durch einfaches Ändern der Abkühlgeschwindigkeit der Panzerung beim Abschrecken auf einen erheblichen Anteil an Legierungselementen verzichten kann. Aber das ist einfach in Worten gesagt - wie viele Vorversuche und Schmelzen Metallurgen machen mussten, werden nur die jetzt klassifizierten Archive sagen können.
Im Metallurgiewerk Magnitogorsk wurden 1941 die ersten Prototypen aus 49C-Stahl hergestellt, die der traditionellen "Vorkriegspanzerung" nicht nachstanden. Insbesondere der Beschuss durch die 76-mm-Kanone zeigte die vollständige Einhaltung der taktischen Anforderungen an den Panzer. Und seit 1942 wurden für die KV-Serie nur Rüstungen mit der Bezeichnung 49C verwendet. Es sei daran erinnert, dass der Verbrauch von Chrom, Molybdän und Nickel deutlich zurückgegangen ist.
Die Suche nach neuen Formulierungen von Rüstungen für schweres Gerät endete damit nicht. 1942 wurde der Stahl GD-63-3 „geschweißt“, völlig frei von knappem Chrom und Nickel. Nickel wurde teilweise durch Mangan ersetzt - sein Anteil hat sich mehr als verdreifacht (bis zu 1,43%). Prototypen der neuen Rüstung wurden beschossen. Und sie erwiesen sich im Design des KV als durchaus massentauglich. Aber die Panzer von Klim Woroshilov mit mittelharter Panzerung gingen in den Ruhestand. Und an die Stelle der schweren Fahrzeuge traten „Joseph Stalin“-Fahrzeuge mit hoher Panzerung.
Gerollte Rüstung 51C
Wenn die 70L Panzerung für den IS-2-Turm gegossen werden konnte, dann funktionierte dieser Trick bei den Wannenteilen des Panzers nicht. Hier standen die Ingenieure vor zwei Problemen gleichzeitig - der Herstellung einer hochfesten Panzerung mit großer Dicke und der Notwendigkeit, sie in einen fertigen Rumpf einzuschweißen.
Jeder Interessierte kennt wahrscheinlich bereits die Probleme, die durch das Schweißen der T-34-Panzerung entstehen - es besteht eine hohe Risswahrscheinlichkeit im Bereich der Schweißnähte. Der IS-2 war keine Ausnahme. Und sein Körper sollte ursprünglich aus endgültig wärmebehandelten Teilen gekocht werden.
Die TsNII-48-Spezialisten erkannten, welche Schwierigkeiten und Gefahren eine solche technologische Lösung bei militärischen Operationen mit sich bringen würde, und änderten den Panzerproduktionszyklus. Infolgedessen wurde 1943 im Ural-Schwermaschinenbauwerk und im Tscheljabinsk-Werk Nr. 200 beschlossen, den Rumpf des IS-2 aus Panzerplatten zu kochen, die nach dem Rollen nur einen hohen Urlaub hinter sich hatten. Das heißt, der Rumpf eines schweren Panzers wurde aus "rohem" Stahl zusammengebaut. Dies reduzierte Schweißfehler auf dem 51C-Walzpanzer mit hoher Härte erheblich.
Die abschließende Wärmebehandlung durch Erhitzen vor dem Abschrecken wurde bereits am geschweißten Tankkörper durchgeführt, nachdem dieser zuvor mit inneren Streben verstärkt wurde. Die Leiche wurde drei Stunden im Ofen aufbewahrt. Und dann wurden sie mit speziellen Geräten in einen Wasserabschreckbehälter überführt und 15 Minuten darin aufbewahrt. Außerdem stieg die Wassertemperatur im Abschreckbehälter von 30 auf 55 °C. Die Oberflächentemperatur des Körpers nach der Entnahme aus dem Wasser betrug 100-150 ° C. Und das ist nicht alles.
Nach dem Abschrecken wurde der Körper sofort in einem Umluftofen bei einer Temperatur von 280-320 ° C niedrig angelassen, wobei nach Erreichen dieser Temperatur 10-12 Stunden lang gehalten wurde. Das Niedrigtempern von gegossenen Türmen aus 70L Panzerung wurde in ähnlicher Weise durchgeführt. Interessanterweise dauerte die Rissbekämpfung in den experimentellen IS-2-Rümpfen vier Monate, als die ersten Produktionstanks die Fabriktore verließen.
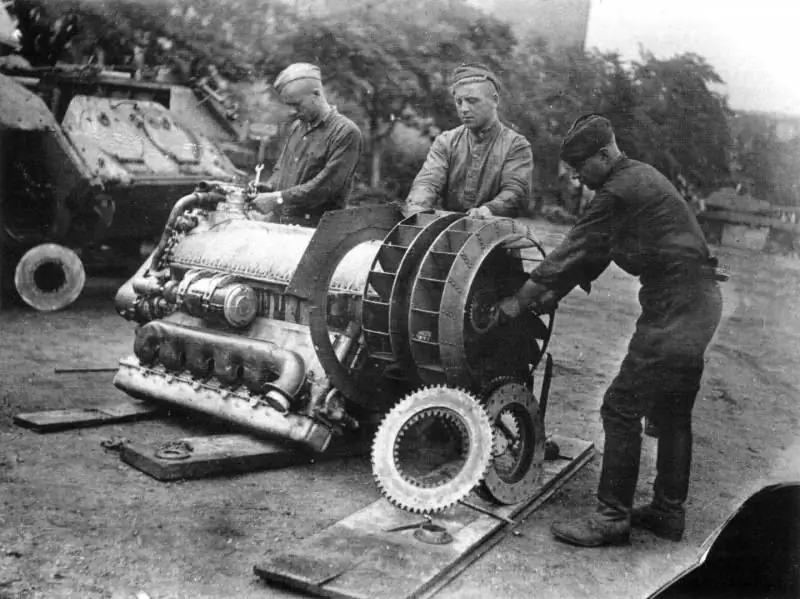
Chemische Zusammensetzung
Was war die gerollte 51C-Panzerung, die für den IS-2, ISU-122 und ISU-152 zur wichtigsten wurde? Es ist ein tiefhärtender Stahl für große Panzerungsdicken mit folgender chemischer Zusammensetzung (%):
C 0, 18-0, 24
Mn 0, 70-1, 0
Si 1, 20-1, 60
Cr 1, 0-1, 5
Ni 3.0-3.8
Mo 0, 20-0, 40
P ≤0,035
S ≤ 0,035.
Im Vergleich zur Gusspanzerung 70L hatte der 51C-Walzstahl einen höheren Anteil an Molybdän und Nickel, was eine Erhöhung der Härtbarkeit auf bis zu 200 mm garantierte. Als die Rümpfe schwerer Panzer mit 88-mm-Granaten beschossen wurden, stellte sich heraus, dass die Panzerung mit hoher Härte ihren Vorgängern mit mittlerer Härte in der Haltbarkeit weit überlegen war. Das Problem mit dem Platzieren der gerollten Panzerung 51C wurde sofort behoben.
Intelligentes Schweißen
Ein wichtiger Beitrag zum Erfolg der Entwicklung der Panzerproduktion von Panzern der IS-Serie wurde durch das automatische Schweißen von Stahl unter einer Flussmittelschicht geleistet. Da es Anfang 1944 nicht möglich war, den gesamten Herstellungsprozess eines Panzerrumpfes auf ein solches Schweißen zu übertragen, konzentrierten sich die Ingenieure auf die Automatisierung der am meisten ausgedehnten und mechanisch belasteten Nähte.
Im Werk Tscheljabinsk Nr. 200 konnten bei der Montage des Rumpfes des schweren Panzers IS-2 nur 25% aller Schweißnähte automatisiert werden. Bis Mitte 1944 war Tankograd in der Lage, 18 % aller möglichen 25 % der Schweißnähte zu automatisieren. Die Gesamtlänge der Schweißnähte entlang des Rumpfes des schweren Panzers IS-2 betrug 410 lfm, davon 80 lfm im automatisierten Schweißverfahren.
Dieses Ergebnis hat zu erheblichen Einsparungen bei knappen Ressourcen und Strom geführt. Es konnten bis zu 50 qualifizierte Handschweißer (deren Arbeitskosten in Höhe von 15.400 Arbeitsstunden) freigesetzt und 48.000 Kilowattstunden Strom eingespart werden. Verringerter Elektrodenverbrauch (ca. 20.000 kg, austenitisch - 6.000 kg), Sauerstoff (um 1.440 Kubikmeter).
Auch der Zeitaufwand für das Schweißen wurde deutlich reduziert. Das Anschweißen des Bodens und des Turmkastens an den Seiten mit einer sechzehn Meter langen Naht dauerte im manuellen Modus 9,5 Arbeitsstunden und nur 2. Eine Naht ähnlicher Länge, die den Boden mit den Seiten des Panzerrumpfs im Automatikmodus verbindet, erforderte 3 Mannstunden (im Handbuch sofort 11, 4). Gleichzeitig könnten beim automatischen Schweißen hochqualifizierte Schweißer durch ungelernte Arbeiter ersetzt werden.
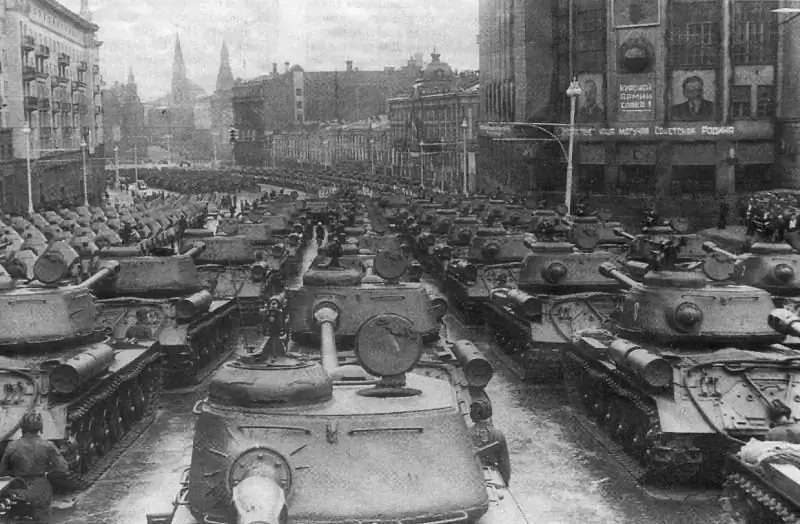
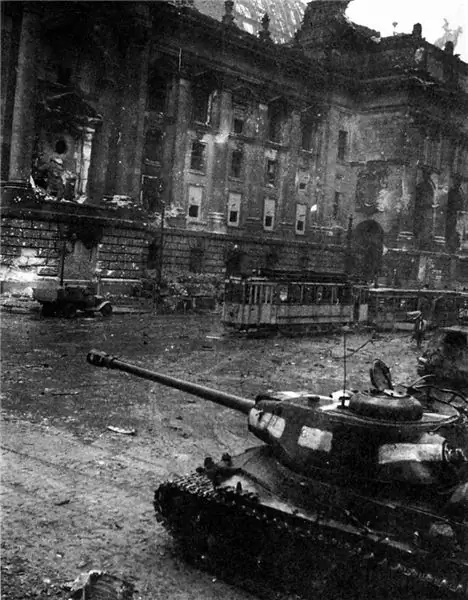
Ural-SAGs
Der Forscher der sowjetischen Panzerindustrie, Kandidat der Geschichtswissenschaften Zapariy Vasily Vladimirovich vom Institut für Geschichte und Archäologie der Uraler Zweigstelle der Russischen Akademie der Wissenschaften beschreibt in einem seiner Werke sehr detailliert die automatischen Schweißgeräte, die im Ural für Panzerfahrzeuge verwendet werden Rumpfproduktion.
Am weitesten verbreitet war ein Sturmgewehr vom Typ "ACC" mit Bushtedt-Kopf. In Uralmash gab es acht solcher Installationen. Die Drahtvorschubgeschwindigkeit bei dieser Maschine war abhängig von der Spannung im Lichtbogen. Es erforderte 5 Einheiten, darunter 3 kinematische Elektromotoren und 1 Motor-Generator.
Mitte 1943 wurde die Schweißmaschine SA-1000 für die Bedürfnisse der schweren IS-2-Panzer entwickelt. Oder ein Schweißgerät mit einer Leistung von bis zu 1000 A.
Um die Produktion von gepanzerten Rümpfen für den neuen schweren Panzer IS-3 von Tscheljabinsk zu beherrschen, entwarfen die Ingenieure des Werks 1944 den Apparat "SG-2000". Diese Maschine wurde für die Verarbeitung von kohlenstoffarmen Schweißdrähten mit vergrößertem Durchmesser (6-8 mm) entwickelt und fand ihre Anwendung bei der Herstellung des IS-3-Turms. Die Anlage verfügte über einen Dispenser zum Einbringen einer speziellen Zusammensetzung (verschiedene Ferrolegierungen) in die Schweißnaht, um das darin befindliche Metall zu desoxidieren (wiederzugewinnen). Insgesamt wurden nach dem Prinzip der Selbstregulierung des Schweißlichtbogens an der UZTM bis 1945 9 automatische Schweißanlagen dreier Typen geschaffen: "SA-1000", "SG-2000", "SAG" ("Automatisches Schweißen") Kopf").
Schöner als deutsche Rüstung
Das Ergebnis der ganzen Geschichte mit der Panzerung schwerer IS-Panzer war eine überraschend schnelle Entwicklung einer Stahlrezeptur, die in ihren taktischen Eigenschaften die deutsche Panzerung übertraf. TsNII-48 erhielt einen härtbaren 120-mm-Stahl, dessen Dicke bei Bedarf auf 200 mm erhöht werden konnte.
Dies wurde die Hauptgrundlage für die Entwicklung der Nachkriegsfamilie schwerer sowjetischer Panzer.